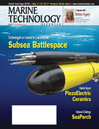
Page 39: of Marine Technology Magazine (May 2011)
Subsea Defense Edition
Read this page in Pdf, Flash or Html5 edition of May 2011 Marine Technology Magazine
www.seadiscovery.com Marine Technology Reporter 39 deployment of sonar or optical imaging payloads. A 3D thrust vectoring propulsion system unique to the SQX- 500 creates an extremely maneuverable platform, allowing for capabilities such as hovering, crabbing and a zero meter turning radius around the vertical axis. The thrust- vectoring system consists of identical forward and aft rud- ders each capable of +360° rotation. On each rudder is mounted a thruster and propeller, which in turn is mount- ed on an elevator assembly capable of +30° pitching rota- tion. In operation the rudders and thruster elevator assemblies can be configured dynamically by the vehicle control computer to provide hovering and a very high degree of maneuverability.
The design process involved extensive use of the expert- ise and facilities of the NRC Institute for Ocean
Technology (IOT) in St. John’s, Newfoundland. These include a 200 meter long, 12 meter wide and 7 meter deep clear water towing tank with a carriage capable of con- trolled speeds between 0.001 meters / second and 10 meters / second and equipped with a planar motion mech- anism (PMM); a cavitation tunnel with a 2.2 meter long, 0.5 meter square test section equipped with propeller thrust and torque dynamometers. Marport worked with
IOT’s staff of AUV researchers, hydrodynamicists and computational fluid dynamics specialists to develop the overall vehicle and thrust-vectoring propulsion system.
To progress from the initial conceptual SQX-500 AUV design to a prototype design for construction, estimates of hydrodynamic drag and power requirements were neces- sary. Previously published scientific literature was reviewed to locate existing hydrodynamic drag data for similar designs of each component. This information was a critical input into the initial propulsion system design – propellers and thrusters — and an essential component for an initial performance estimate of the AUV. In order to simplify the estimation process, the hydrodynamic loads acting on the system were evaluated as separate com- ponents; cylindrical hulls with ellipsoidal nose cones, ver- tical rudders, and horizontal elevators. The contributions from these individual components were then summed to estimate the total vehicle forward drag. Previously pub- lished scientific literature was reviewed to locate existing hydrodynamic drag data for similar designs of each com- ponent.
Cylindrical hull forward drag values were based on pub- lished measured data for single pod vehicles. Rudder and