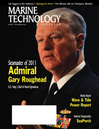
Page 21: of Marine Technology Magazine (June 2011)
Hydrographic Survey
Read this page in Pdf, Flash or Html5 edition of June 2011 Marine Technology Magazine
www.seadiscovery.com manufacturing experts in the country three years ago,”
Power says. Since then, the time it takes to build, paint, and test one LARS has dropped from 4,000 hours to under 2,000 hours, reducing delivery time from two months to one. One example of eliminating wasted man hours is not having to spend 10 minutes a day looking for a tool, which saves 2 hours and 15 minutes a week per per- son in lost time. Profit sharing provides an incentive for employees to participate in the process. Thorarinson and
Power emphasize that safety is priority number one. Before starting work, the employees rate the risk of each job using field level risk assessment cards and then figure out how to mitigate the risk. That could mean using a full harness with double lanyards to weld eight feet in the air, erecting scaffolding, or calling on someone with lifting experience before moving a heavy piece of equipment. “What we’re most proud of is our safety record,” said Thorarinson. “Safety isn’t something you shove down someone’s throat.
It’s a culture we’ve built here,” pointing to a sign on the wall in the front office that reads: “1,115 days without a lost-time accident.”
Drilling and exploration activity in the Gulf of Mexico is still slow following the Macondo Blowout and as the econ- omy recovers from the recession, says Power. “But business has been picking up,” he adds. “Permits are being issued.
I’m pretty optimistic about LARS over the next 12 months.”
Orphan Industries Chief Engineer Torfi Thorarinson beside a structural component of LARS. The white spray paint indicates where a weld has been inspected. (Cr edit: Andr ew Safer)