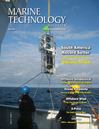
Page 42: of Marine Technology Magazine (April 2018)
Offshore Geophysical
Read this page in Pdf, Flash or Html5 edition of April 2018 Marine Technology Magazine
New Products Buoyancy
Customization for Buoyancy Applications
Subsea vehicles and structures are ROV blocks being machined onsite required to minimize their weight in at Trelleborg’s Boston location.
water, which necessitates the use of a
HGMS but can also carry out testing of lightweight materials that incorporate density, strength, moisture content and hollow glass microspheres (HGMS) that more. Additionally, the ? nished buoy- can resist the crushing pressures of the ancy package should go through its own ocean. These HGMS can be customized testing to ensure the ? nal product meets via surface treatments, material chem- the density, weight and strength param- istry selection, density speci? cations eters for the project. Typical buoyancy or particle size distribution, thereby op- tests include: timizing their impact on the ? nal sub-
Trelleborg sea composite. When combined with a tional uplift while protecting the vehicle • Hydrostatic testing of full cubic host of polymer matrices the resulting from impact and abrasion. Umbilical feet buoyancy blocks and cabling use a thermoplastic sheath- • Cycle testing for 1,000 times composites have spawned a host of high functionality subsea materials such as ing or core to reduce weight while main- • Full testing to hydrostatic pressure taining electrical performance. In addi- on random samples ef? cient static buoyancy, thermal insu- tion to these, are a host of ? oats used on • 10% of manufactured blocks tested lation and buoyant fairing components.
The combination of these solutions the equipment the ROV is servicing or at service pressure for 24 hours deploying. Through customization and testing of can be seen in the operation of an ROV/ high–tech hollow glass microspheres,
AUV vehicle. The static buoyancy packs provide most of the uplift required to Buoyancy Testing deep-sea exploration vehicle manufac-
When choosing a supplier for buoy- turers are able to meet their strength and maintain stable operation. Thermoplas- ancy, manufactures should look for a weight speci? cations for each unique tic fairing components provide addi- company that not only manufactures vehicle.
Balmoral’s Boltless Restrictor
Balmoral Offshore Engineering has launched a new prod- uct for the SURF sector which it claims will reduce cur- rent installation times by up to 80%. The company has ex- tended its range of polyurethane bend restrictors to include a boltless version (patent pending) in response to industry demands for project cost savings and as part of a wider product improvement drive. Designed as interlocking ele- ments, restrictors prevent over-bending at the interface be- tween ? owlines, umbilicals, cables and rigid structures such as wellhead connections, J-tube exits, rigid pipe crossovers and PLET connections by mechanically locking up.
Although there are products on the market that claim to be boltless, Balmoral says none of them actually are. The new boltless restrictor is capable of: • rapid assembly to minimize installation times • performing on ? ying leads, umbilicals, risers and ? owlines • enduring long-term loading conditions • enduring hot, wet conditions • managing large bending loads
Balmoral Offshore Engineering
April 2018 42
MTR
MTR #3 (34-48).indd 42 MTR #3 (34-48).indd 42 4/9/2018 9:56:04 AM4/9/2018 9:56:04 AM