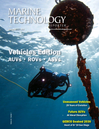
Page 23: of Marine Technology Magazine (January 2019)
Underwater Vehicle Annual
Read this page in Pdf, Flash or Html5 edition of January 2019 Marine Technology Magazine
design is a combination of ? nding the is also being made available to other best propeller and nozzle (also called naval architects and engineers as new duct or shroud) while keeping track of hydro-acoustic features are developed their interaction. In other words, you for our tools. A project’s sensitivity to must use design tools that include this noise is now always part of discussion interaction, such as NavCad for system with our UUV propulsor design engi- modeling or PropElements® for pro- neering clients.
peller-nozzle component design. All hydroacoustic excitation is from
In all UUV propulsor design proj- mass ? uctuation (the periodic move- ects, one universal objective is to de- ment of ? uid mass). Propulsor-driven velop a geometry that generates the hydroacoustics is generally caused by highest thrust-to-power ratio (its ef? - variations in the low-pressure zones of ciency), which we achieve using well- the propeller as it rotates in-and-out of established practices. It is generally “shadowed” regions, such as behind a the in? uence of external design drivers strut or control ? n. Part of the ? uctua- that can make successful UUV propul- tion is simply from the change in ? ow sor design so challenging. For exam- direction around the blade caused by ple, the RPM can be too high (as noted the varying in? ow, but more signi? - above). Geometric constraints can cantly by the rapid expansion and col- limit the maximum diameter (to ensure lapse of cavitation on the blade. Each it remains within the body diameter) of these is evaluated as part of our or they can in? uence the design to ac- propulsor design, with mitigation as count for slope of the vehicle’s tail. needed by changes to a blade’s outline
It is important to take a moment and its camber-pitch distribution.
and mention the implications of UUV Excessive hydroacoustic excitation – propulsor manufacture. There is sub- and transmission – can also be aided stantial discussion in the press about with a creative nozzle design. Using additive manufacturing (AM) for our background in nozzle performance propellers. While this may be attrac- modeling, we can consider if particular tive from a ? nancial and deliverabil- noise-quieting nozzle geometry can of- ity standpoint, we must take care that fer the necessary suppression, as well performance is not compromised by as any loss of propulsor ef? ciency.
inappropriate surface texture (which So, while UUV propulsor design has can have a huge in? uence for propul- its collection of unique challenges, is sor of the small size found on most it still just a component task within a
UUVs), fatigue strength failures, or larger system problem. It can offer a by hydro-elastic ? exure in the blade. satisfying engineering challenge, one
HydroComp has developed successful that can be successfully completed practices for the use of AM for small with a little care, proper tools, and propulsors through a variety of in- practical experience.
house research projects.
About the Author
Beyond these practical design con- siderations, one of the most interesting Donald MacPherson, a leading spe- contemporary design drivers the topic cialist in propulsion system simulation, of radiated noise. As part of a broader is HydroComp’s Technical Director, sustainability initiative, HydroComp where he oversees all software devel- has developed expertise in the predic- opment and engineering services. A tion and mitigation of propulsor hy- graduate of Webb Institute, he is a Fel- droacoustics (the term that captures low of SNAME and member of its Pro- noise and vibration). This knowledge pulsion Hydrodynamics Panel.
www.marinetechnologynews.com
MTR #1 (18-33).indd 23 MTR #1 (18-33).indd 23 2/6/2019 3:36:33 PM2/6/2019 3:36:33 PM