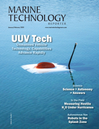
Page 53: of Marine Technology Magazine (January 2020)
Read this page in Pdf, Flash or Html5 edition of January 2020 Marine Technology Magazine
tooling, including the motors, are on the vehicle so that the
Getting a Grip interchangeable tools (suites of which can be kept, ready to
Grip Offshore is also working on a fully electric manipula- use, subsea) can be as simple and robust as possible.
tor, called eManip7. Bjarte Nedrehagen, the company’s CEO, “It’s a mechanical interface with all the smarts inside the points out that most electric ROVs today still use hydraulic AUV,” he says. These “smarts” are comprised of two motors, manipulators. In 2018, the company, signed a LOOP agree- each independently controllable, that can drive multiple func- ment with Equinor Technology Ventures, to develop a seven- tions within the individual tools, including a gripper, cleaning function electric manipulator similar in design and physical brush, CP probe, and softline cutter in one with an output of up capability to a Schilling Titan 4, using Grip Offshore’s stan- to 2700nm. It’s not just handy for tooling; when docking, one dardized smart actuators as robotic joints and motion control motor drives a locking mechanism to hold the vehicle onto its capabilities better than a hydraulic system. docking system. The innovative interface also provides pin-
Core to the project is developing motion control software less power and communications connectivity.
that will enable the use of a Titan 4 control joystick. Another “When we looked at this approach, we saw we could do
Norwegian ? rm, IKM Technology, is a partner on the project. much more,” says Carlsen. “We can even put a propeller on (to
Nedrehagen told OE at Tau, “It is a conservative market,” the interface), for long range operations. This is just the tip of with an ‘if it’s not broken, don’t ? x it’ attitude and contracting the iceberg.” Another idea is to use it to ? y out a small drone models that inhibit new technology adoption.” But, change is from this interface on Freedom, when perhaps an alternative happening and he’s keen to see an industry standard interface viewing angle is needed. Furthermore, because it’s electric, for subsea tooling so that it’s easier for alternative suppliers to when applying torque, it’s able to sense the rotational torque provide equipment. being applied (something that isn’t measured with existing hydraulic driven systems).
A new concept While designed for the Freedom, the idea is for the interface
Oceaneering has developed a completely new concept for to be compatible with the entire Oceaneering ? eet of ROVs, its Freedom vehicle. It has designed a tooling interface that says Carlsen. This roll out will include a handheld version of can either work inline of the vehicle, e.g. facing forward, or the interface for traditional work class ROVs and enable the pointing down, by rotating it 90 degrees. The neat thing, Tor- entire ? eet to make use of the subsea tooling suite.
leif Carlsen, research and design engineer, Oceaneering, told
OE at the Tau event, is that all the “smarts” for operating the – Elaine Maslin
Oceaneering’s electric work class eNovus ROV with handheld tooling interface.
Credit: Oceaneering www.marinetechnologynews.com
Marine Technology Reporter 53
MTR #1 (50-63).indd 53 1/16/2020 1:06:50 PM