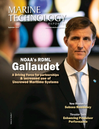
Page 41: of Marine Technology Magazine (September 2020)
Read this page in Pdf, Flash or Html5 edition of September 2020 Marine Technology Magazine
this type of work, it’s not about the length of deployment, it’s about what it can do while it’s there, he says. That’s why
Gemini has been designed for month-long deployments, with some signi? cant advances around tooling and automation (as well as having two manipulators as standard).
An ROV with a tool belt
In terms of tooling, Gemini comes with an inbuilt tooling carousel, with 15 tools, and a further 15 on the tether man- agement system. These have a new interface; instead of the traditional manipulator jaws that grab a T-bar on a tool, the manipulator tip is a stab that picks up a tool and provides a hydraulic, electric and communications interface. The vehicle also has up to ? ve machine vision cameras, so the vehicle knows what it’s looking at and can more accurately measure distance; the machine vision cameras help ? ne-tune station keeping capability to within 25mm (better than what can be achieved with current navigation sensors, MacInnes says).
Together, these capabilities enable the vehicle to perform pre- determined tasks, such as tool selection, helping to overcome any issues with latency. The pilot (remote or otherwise) sim- ply taps a touch screen to select the tool (an “intent based instruction”) and the ROV does the rest – instead of having to bring the ROV to surface to recon? gure the tooling, says
MacInnes. These capabilities take it a step closer towards op- erating under a level of supervised autonomy. And it means there’s more consistency in the performance of these tasks (it could take anywhere between 10 minutes to two hours to insert a hot stab, depending on experience, with the current -500m generation ROVs, says MacInnes). “It’s the similar technology to companies such as Tesla but more complex,” he says, “because, for a car, all it has to do is avoid hitting something. As long as it avoids being within
SEEKER - Acoustic Directional Receiver 2-3cm, it’s done its task. We need to physically engage with things, such as insert a hot stab, and that creates additional
The small and rugged RJE SEEKER is used -1,000m complexity.” to assist AUV and ROV operators in tracking underwater beacons and transponders,
The move towards supervised autonomy will support a re- from 25kHz to 45kHz at full ocean depth.
duction in the amount of support required offshore, includ- ing ROV crew, says MacInnes. But whether full autonomy is needed – and if it could justify the investment that would be required – is questionable, he says. One thing that is viable, with the level of supervised autonomy that TechnipFMC is -6,000m moving towards, is operating these systems from a USV, he says. “With supervised autonomy, we can start to interface this new generation of work class ROV technology with new -8,000m generation of USVs,” says MacInnes. “It’s achievable and we
IKM Subsea has notched up 100 days continuous operations at Snorre B with its Merlin UCV R-ROV.
Photo from IKM Subsea
Enabling ROV and AUV operators to track and relocate www.marinetechnologynews.com
RJEInt.com | 949-727-9399
MTR #7 (34-49).indd 41 9/11/2020 11:11:35 AM