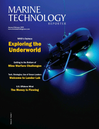
Page 31: of Marine Technology Magazine (January 2022)
Read this page in Pdf, Flash or Html5 edition of January 2022 Marine Technology Magazine
Shelf. This was risky work. Having made one journey under the Fimbal Ice Shelf, in 2005 Autosub-2 made a second jour- ney – never to return. Luckily, aware of the risks of under-ice deployment, Autosub 3 was already being built and quickly replaced Autosub 2, says Furlong. Its crowning glory was work under the Pine Island Glacier in 2009. A total track of 887 km was covered over 167 hours, of which 510 km was beneath the glacier, mapping the underside of the ice with an upwards looking multibeam system.
However, one of the problems with Autosub-3 was that it was quite shallow rated, at 1600 m, and it still used primary batter- ies, says Furlong. So work started on Autosub6000 – a 6000 m-rated system. It used a lot of the technologies in Autosub 3, but moved over to rechargeable pressure tolerant lithium batteries, enabling the depths targeted. “Initially there were real concerns over the compressibility of the syntactic foam used,” says Furlong. “These vehicles are ballasted, so they are pretty close to just slightly positively buoyant. The worry was that the foam would compress faster than the seawater which could result in the vehicle becoming negatively buoyant and potentially sinking if it stopped moving. The other concern was how to accurately locate yourself at the seabed. You start at the surface with a GPS ? x, then dive through 6km of water drifting with the current, and ? nally about 150m from the bed you can navigate using a Doppler Velocity Log and compass.
So there was some early work done on to address this naviga- tion offset problem, using a Linkquest USBL system to locate and send navigation offsets to the sub.
Autosub6000’s ? rst science mission was bathymetric sur- veys of scours in the Agadir Canyon, in 4000 m water depth northwest of Morocco in 2008. It also went hydrothermal vent hunting in the mid-Cayman rise in 5000 m water depth and discovered world’s deepest hydrothermal vent at the time. Au- tosub6000 has also worked on the Darwin mounds in Rockall
Trough area, undertaking high frequency side scan and pho- tography surveys, looking at cold water coral, and also work in marine protected areas, says Furlong. “It’s also done work mapping the walls of Whittard Canyon, which involved rota- tion the multibeam sonar and angling it so it would image the canyon sides.”
However, there were still challenges with Autsub6000. “It’s a great vehicle, and has been really successful, but it is still limited to deployment from Research Vessels. We wanted to go further, as there are many missions which you just couldn’t do with Autosub6000. One example is a full Arctic cross- ing from Svalbad (Norway) to Barrow (Alaska) monitoring under the ice as you go, a second is surveying ocean choke points, such as Drakes Passage, which are currently dif? cult to routinely monitor.” The result was the Autosub Long Range (ALR) development in 2010-11. “It was quite different to the existing subs,” says Furlong. “A lot of new developments were required to enable the increased endurance with a lot of focus www.marinetechnologynews.com 31
MTR #1 (18-33).indd 31 1/25/2022 10:04:56 AM