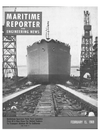
Page 12: of Maritime Reporter Magazine (February 15, 1969)
Read this page in Pdf, Flash or Html5 edition of February 15, 1969 Maritime Reporter Magazine
A New U.S. Designed And Manufactured Diesel Engine The Design And Economics G. F. Schumacher* The Cost Of Fuel And Lubricating Oils And The Maintenance Of Propulsion Plants Are Major Considerations. The Author Calculates Them For A 15,000-Bhp Plant. There have been many European technical papers presented regard-ing the economics of slow-speed and medium-speed diesel engines. The purpose of this paper is to present an American designed and manufactured diesel engine, suit-able for marine propulsion in the same manner. The engine described is the Model 38A20 opposed-piston engine, as produced by Fairbanks Morse Power Systems Division of Colt Industries. The 38A20 diesel engine is a two-cycle, uniflow scavenged, opposed-piston engine with cylinders in line or a 45-deg. 'V.' It has been de-signed with six and nine cylinders in line or 12 and 18 cylinders in 'V,' all rated at 1,250-hp per cyl-inder. For marine propulsion, the engine may be direct reversing. The cylinder block and lower base are mild-steel weldments with low stress levels. A series of trans-verse bulkheads carry the stress be-tween the upper and lower portions of the cylinder block. Power is transmitted to the shaft through a cast-iron cocktail shaker, oil-cooled piston, and a nodular-iron connecting rod. The large low-er piston controls the air inlet parts while the small upper piston con-trols the exhaust parts. Since the valving action of the upper piston develops 15 percent of the rated power, it is connected to the engine output by a rocker arm, rods, upper crankshaft, and vertical gear train. The crankshafts are high-strength, nodular-iron castings with large corings in the mains and pins to reduce weight. Clutch And Couplings In order to give a vessel an opti-mum operating condition when us-ing twin-pinion units (two medium-speed engines geared to a single shaft), disconnect clutches must be provided. The airflex-type clutch furnishes the less expensive means of providing this choice of opera-tion. Torsional flexibility also must be *Mr. Schumacher, manager, marine sales, Fairbanks Morse Power Systems Division, and a retired U.S. Coast Guard captain, presented a paper before a re-cent Great Lakes and Great Rivers Sec-tion of The Society of Naval Architects and Marine Engineers on diesel power-plants. Condensed here is one section of that paper. considered. Fairbanks Morse pre-fers to use torque shafts as a sim-ple solution to most _ propulsion problems. Each propulsion system must stand on its particular merits. When the exact position of ma-chinery has been placed for the vessel and the propeller and shaft-ing have developed their final con-figuration, Fairbanks Morse tKen calculates the torsional problems for the system and recommends ad-ditional torsional couplings if they are required. Fuels Successful operations on heavy-oil fuel have been achieved on cast-iron liners with an untimed cylin-der lubricating-oil system. The suc-cess is attributed largely to the low metal temperatures in the engine. As marine diesel engines must operate on the fuels available in the area in which the vessel is scheduled, the 38A20 engine has been operating on a heavy fuel which has a wide range of chemical and physical characteristics. For the purpose of this study, 3,500 sec. Redwood I at 100°F. has been used. Maintenance schedules for the engine were laid out on this premise. Lubricating Oil The successful operation of a medium-speed, trunk-piston engine burning heavy fuels depends on the correct selection of lubricating oils. On the 38A20 test engine, a medi-um detergent-dispersant oil was used to determine a base operating condition for the engine. The lub-ricators were filled directly from the crankcase. The lube-oil consumption on the Model 38A20 has been between 5.000 to 6,000 bhp-hours per gallon. To date, the pistons and rings have been clean on inspection. The ex-haust ports have shown no signs of plugging with carbon. The yearly fuel and lubricating oil costs calculated by the author for two six-cylinder 38A20 engines (7,500 hp at 450 rpm, each) de-veloping a total of 15,000 bhp and operating 7,200 hours per year are: fuel oil?4,925,880 gallons or $227,-529; lube oil?18,000 gallons or $25,200. Maintenance The Model 38A20 engine has just started its service life. There will be approximately 150,000 hp de-livered for base-load plants by January 1969. The six-cylinder test engine has 7,000 hours of operation with over 1,500 hours of operation on heavy fuel. The maintenance figures (de-veloped in the appendix to this pa-per) for the Model 38A20 have been developed on progressive mainte-nance which is considered ship-force work and can be accomplish-ed by either day workers or watch standers. Manhours required for mainte-nance on a ship for a 25-year pe-riod of 180,000 hours of operation (300 days per year) are 25,404 hours for two six-cylinder 38A20 engines and gear and approximate-ly the same hours for a 12-cylinder engine. This manhour figure breaks down into 15,980 hours for preven-tive maintenance and 9,424 hours for repair and replacement (actual estimate for the latter operations was 4,712, but the author doubled it to be conservative). The material costs are given as $207,065 for pre-ventive maintenance and $402,700 for repair and replacement. This then gives an average material cost of $1.63 per bhp per year for 15,000-bhp twin 38A20 diesel engines op-erating 7,200 hours per year over a 25-year period. For less operating hours, the cost is naturally less But not in direct proportion to the op-erating hours. Conclusions With proper design considera-PROP SHAFT T o V> ' L tions, a 400- to 450-rpm trunk-type, two-cycle engine without valves can operate on residual fuels suc-cessfully. As in other engines, the piston ring and ring groove wear will be slightly more rapid than on light oil. Increased maintenance on the fuel injectors may be required, depending on the fuel filtering and treatment system employed. Ma-neuverability on heavy fuel is not a problem if adequate heating of the fuel system is provided. As direct-drive engine users have experienced, the ability to burn heavy fuel provides a significant economic advantage in long-term savings. Prime movers for ship pro-pulsion can, therefore, be evaluated largely on the basis of specific fuel consumption when an operating profile is established. Lubricating-oil consumption in a medium-speed engine need not be higher than other heavy-fuel en-gines with the application of a good lubricating system and the selec-tion of modern compatible lube oils. The cost of lube oil consumed for heavy-fuel engines is higher since the most successful cylinder lubricants are more expensive. This expense can be reduced by using less expensive lubricating oils during operation on higher-grade residuals. Figure 1 shows a proposed lay-out for twin-pinion, 18-cylinder 38A20 engines used to develop 45,-000 bhp in a twin-screw ship. WEIGHTS - L3S 2 GEARS W/ACC 400,000 4 PROP ENGINES 1,400,000 I SET CONTROLS 3,000 TOTAL 1,803,000 WEIGHT DOES NOT INCLUCE AIR INTAKE FILTER, EXHAUST SILENCER, STARTING AIR SYSTEM AND SHIPS PIPING. ALL DIMENSIONS SHOWN ARE APPROXIMATE 52-0-l\ \\ \\ \\ RJ H j-J uuuuuuuu t RJ H "