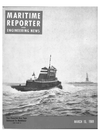
Page 62: of Maritime Reporter Magazine (March 15, 1969)
Read this page in Pdf, Flash or Html5 edition of March 15, 1969 Maritime Reporter Magazine
Comparative Considerations Steam Power Vs Gas Turbines V. A. Johnson* It would be presumptuous to represent myself as an expert on the subject of marine propulsion systems. I have, therefore, taken the opportunity to review studies recently made by authorities on the subject. Thus, I propose to interpret the ob-servations of some competent information sources which will allow us to make an analysis of the advisability of switching from a proven and im-proving system of marine propulsion, to one which is still substantially in the experimental stages of development. Let me first make you aware that there have been many significant advances in marine boiler technology in recent years. Since the boiler is such a major and significant component of the total steam-propulsion system, it is being continually studied for improvements. A depth study of over 500 selected service reports on recent designs has led to the conclusion that virtually all problems associated with marine boilers has resulted from one, or a combination of the following causes: 1. An inadequate combustion process. 2. Inadequate boiler water chemistry control. 3. Poor operating techniques and neglect. Let us focus on a few of the components. There is now being developed a register and steam atomizing Racer-type oil-burner combination that will result in a turn-down range in the order of 75 to 1. The marine steam-atomizing oil burner is capable of burning fuels direct from previously ballasted tanks and can, without difficulty, burn fuels that contain up to approximately 10 percent seawater. The modern marine boiler design includes the maximum practical amount of water cooling in the furnace, basically to protect the refractories in the furnace envelope. Recent designs have increased furnace water cooling by additional waterwalls in the furnace rear wall, front wall, and floor and have tightened tube pitch centers all around. The superheater vulnerability to vanadium at-tack has been tackled by giving rigid attention to the tube-metal temperature of superheater surface and improved combustion. Slagging has been con-trolled by employing mass-action sootblowers and more judicious bending of superheater pass tubes into the inter-pass lane area in order to restrict flow of gas into this area. With automatic feed and boiler water chemistry monitoring and treatment we can virtually elimi-nate the need to mechanically or chemically clean the boiler watersides. Thus we now have boilers that can effectively burn any common grade of fuel oil, a minimum of gas-side fouling, virtual elimination of waterside cleaning, and related economy advantages. It is encouraging to us that the trend is to an interest in systems since so many steam-plant problems of the past have resulted from lack of system integration and inherent divided responsi-bility. The real challenger as a new prime mover for ship propulsion is the aircraft gas-turbine plant and we propose to compare this plant with the modern steam plant. Principal desired features of a modern ship-*Mr. Johnson, sales promotion manager, Babcock & Wilcox Canada Ltd., presented the paper con-densed here before a recent meeting of the Eastern Canadian Section of The Society of Naval Archi-tects and Marine Engineers held in Saint John, N.B. propulsion plant can be enumerated as: fast re-sponse rates for all desired maneuvers, any avail-able fuel can be utilized, minimum needs for operating manpower and efficient fuel consump-tion rate. The steam turbine is inherently reversible with its integrally attached reversing turbine. Thus, no additional components are required to effect the reversing function. The steam plant can have an extremely fast re-sponse capability for any maneuvers required. This can be categorized as less than a 30-second response rate for any required maneuver from dead stop to flank speed or from ahead to astern. This response rate is achieved significantly by the single boiler and wide-range burner concepts, since all equipment is on the line all the time assisted by the substantial thermal storage in the boiler drum. The low temperature cycle of the steam plant, in the order of 850° to 950°F. in modern svstems, allows for the use of rugged, proven materials within comfortable margins of safety. In addition, the existence of boilers provides a convenient, flexible and efficient source of energy for essential auxiliary functions in the engine room. Reduced manning is achieved by the single boiler per shaft principle and by the use of optimum de-gree of automation. It is not sufficient that we extoll the virtues of one system without considering the attributes of the closest contender, the aircraft gas-turbine pro-pulsion plant. Our comparison is directed at the growing commitments for propulsion gas turbines in larger horsepower vessels and, in particular, warships of the destroyer class. The main component, of course, is the gas generator which we familiarly see under an air-craft wing, only a few hours or minutes from skilled ground technicians. However, in our con-text, we must move it into the marine engine room environment where it will be exposed to long periods of demanding performance. First we must provide it with substantial acou-stic and ventilation accouterments. This is par-ticularly significant with the trend to light-weight types of gas-turbine units. Then we must add a power turbine and reduc-tion gear, and, because it is inherently non-revers-ing, we need an external reversing gear assembly. This may involve possibly anywhere up to 21 gear rotors (11 gear rotors for a conventional steam system), clutches (not required in a steam sys-tem), and/or a controllable-pitch propeller. Inherent with a gas-turbine system is the poor part-load performance, necessitating multiple en-gine outputs to each propulsion shaft, with the associated clutching arrangement and a fuel con-sumption penalty at cruising power. Like all high-performance gas turbines it can only use distillate and gaseous fuels. This is the result of gas-turbine high-blade temperatures and sensitivity to contaminates in normal fuel oils. It is known that aircraft gas-turbine electric generators have a high fuel consumption?thus it will likely be found that it is economically essen-tial to supply diesel-electric generators on the gas-turbine ship. A separately fired or waste-heat steam generating unit will be found most effective for other auxiliary engine room functions, such as water distillation and miscellaneous heating. The gas-turbine has a remarkable thirst for clean air in the order of 55 lb./hp-hour, compared to the steam plant requirement of about 12-15 lb./ hp-hour. Characteristically, hot gas-turbine ex-haust gases present a problem in designing flues? relative to insulation and material selection. A ma-jor air-duct design complication is the problem of removing entrained particulate salt water, to limit sodium sulphate attack on hot turbine parts. Now let us make some comparisons between steam and gas propulsion systems. The steam plant's claim for use of proven components for marine service does not hold in the case of the aircraft gas-turbine. With respect to the gas gen-erator itself , only advanced engines still in devel-opment stages can even hope to approach a com-petitive situation from a life-cycle viewpoint. The steam plant has an acknowledged versatility in accommodating a wide range of fuels. The gas turbine cannot accommodate fuel tolerance, and thus is at a disadvantage. As there is continuing talk of a multi-purpose fuel (MPFO), the com-patability of the gas-turbine engine becomes even more unrealistic. The gas-turbine compares unfavorably in its ability to achieve the reversing function. This is a simple inherent capability with the steam turbine. Uncertainties of development, system control complexity and machinery reliability risks all con-tribute to the vulnerability of the gas-turbine sys-tem, in this regard. The high temperature cycle of the gas-turbine, and particularly of the advanced engines, implies the uncertainty of necessary advanced materials technology. The relatively low temperature of the steam cycle allow it to be accommodated with rugged, proven materials void of early deteriora-tion risk. The high-temperature, light-weight characteris-tics of the gas turbine engine classify it as a short time constant system. It is critically dependent upon extremely fast, accurate response from con-trol systems and operators. In this regard it com-pares unfavorably with the self-regulating features of the steam plant. And finally, we have the function of the steam plant to provide a flexible energy source for aux-iliary engine room functions?not available from the gas-turbine plant. The steam plant has ample prospects for future development for marine use with further life-cycle-cost advantages. Conversely, it is reasonable to argue that as aircraft engines reach higher states of development, they will become more tech-nically sensitive and, therefore, less compatible to the marine environment. From an economical point of view, we wish to point out one of the principal advantages of the steam plant and that is the very flat fuel-rate curve from full power down to cruising load. This is in contrast to the increasing fuel-rate curve for the aircraft engine as power is decreased, necessitating multiple engine arrangements with inherent com-plications and redundancy of equipment. In closing, may I comment that it is apparent that nuclear propulsion will play an increasing role in future marine propulsion systems. In acknowl-edgement of this prospect it would seem logical to advance steam plant technology as a main stream development rather than embark on any costly diversion with alternate non-steam powerplant development which would entail expensive dupli-cation of technical training, logistic and financial resources. 64 Maritime Reporter/Engineering News