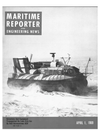
Page 44: of Maritime Reporter Magazine (April 1969)
Read this page in Pdf, Flash or Html5 edition of April 1969 Maritime Reporter Magazine
A Report On The Operation Of The GTS Wm. M. Callaghan Charles E. Hoch* About 13 months ago, the GTS Adm. Wm. M. Callaghan, under charter to the Military-Sea Transportation Service and operated for its owners, Sunexport, by the American Ex-port Isbrandtsen Lines, Inc., entered the North Atlantic service carrying roll-on/roll-off cargo between the ports of Philadelphia and Brem-erhaven. The Callaghan is, frankly, an experimental ship, and during her first year in service has contributed greatly to the knowledge and un-derstanding of the use of aircraft-type gas tur-bines in marine service. A roll-on/roll-off ship, such as the Callaghan, provides an excellent test bed for gas-turbine engines, which combine the desirable char-acteristics of high horsepower, low weight and small space requirements. The machinery plant is based on the use of two FT-4A2 gas turbines manufactured by Pratt & Whitney Aircraft in Hartford, Conn. These units incorporate the FT-4 jet engine, together with a two-stage free-power turbine, all mounted axially in a common casing. The FT-4A2 engines burn JP-4, JP-5 and other high-quality distillate fuels. The Cal-laghan is currently using a military specifica-tion marine diesel fuel. Fuel meeting these specifications is available worldwide. Fuel con-sumption is about 0.51 lb./shp hour at 20,000 hp/shaft. In her first year of operation, the Callaghan has made 17 round trips between either Phila-delphia and Bremerhaven or New York and Bremerhaven. In that time the ship has steam-ed over 130,000 nautical miles, carried a total of 477, 159 measurement tons of cargo consist-ing of 23,227 vehicles. As yet, we have not been able to develop fully, on a continuing basis, the service speed of the Callaghan. How-ever, we have sufficient records to indicate that the Callaghan will probably have a service speed generally in excess of 24 knots, and dur-ing good weather speeds in excess of 25V. knots will be available to us witHn the 40.000-hp rating. At a drydocking shortly after the Callaghan was launched, three buckled areas were found in her bottom amidships, probably resulting from high way-end pressure during launching. These buckles were faired; however, at the guarantee-survey drydocking, approximately the same buckles had reappeared. It is my opin-ion that this buckling is due to a combination of relatively high hull stresses due to light loading, together with the use of relatively thin high-tensile strength plating on the ship's bot-*Mr. Hoch, superintendent engineer, Military Sea Transportation Service, Washington, DC., pre-sented the paper condensed here before a recent meeting of the Society of Marine Port Engineers New York, N.Y., Inc. torn. As a result, it was necessary to repair some plates and to replace others and in-stall panel breakers running longitudinally be-tween the floors over a good portion of the ship's bottom area. The outboard shafting is a torque tube. Dur-ing the guarantee survey, all the protective fiberglass and resin coating was missing from the torque tube and the exposed sections of the solid tailshaft with the result that the end fittings of the torque tube operating in a hostile atmosphere had cracked. It was necessary to reweld these extensive cracks and recoat the shaft. How satisfactory this fix is will not be known until the ship is drydocked for examina-tion within the next several months. The Callaghan was designed to handle a weight cargo of approximately 7,000 tons. It is expected that in service handling military vehi-cles that the actual cargo carried will weigh between 4,500 and 7,000 tons. However, to date, our average loading has been of 'balloon' cargo and, except for one trip in which we carried 3,000 tons and another trip in which we carried 4,320 tons, our average loading has been less than 2,500 tons and this has proved to be a problem. With this light loading in the North Atlantic, the Callaghan has been less than a seakindly ship. In an attempt to reduce pound-ing in very heavy weather, the master has felt it necessary to quarter the seas, and under such conditions has reported extremely heavy roll-ing. However, during the trip in which the Cal-laghan carried 4,300 tons of cargo, the master reported that she rolled easily and regularly in moderate weather with a total roll period of about 12 seconds. This is a high-sided ship and, unless laden in excess of 4,000 tons, it really does not have sufficient grip on the water to insure seakindliness under North Atlantic con-ditions. It is primarily for this reason that we are now contemplating the installation of solid ballast of a type which can be readily removed should the ship move into another service. In addition, we are experimenting with the use of seawater ballast in the fuel oil tanks, both of which, in my opinion, will greatly im-prove the seakindliness. There is a secondary reason for this ballasting. In this big ship, lightly laden and with deeptanks forward and settling tanks aft, high hull stresses can be achieved unless the ship is carrying a fairly good load spread. The addition of the 1,500 tons of ballast, plus the ballasting of double bottom fuel tanks will markedly reduce the hull stresses. The performance of the gas turbines is, to my mind, outstanding. Except for one major incident, the performance of these engines, par-ticularly in an experimental ship, has been at-tended with a lesser number of problems than we would expect to experience in a steamship of like horsepower. On September 6-7, during a passage to Bremerhaven, the temperatures downstream of the compressor turbines showed a sudden and marked rise to an extent that it became neces-sary to secure the starboard engine. Investiga-tion showed that a fire had started within the engine and it was necessary to replace that en-gine in Bremerhaven with the spare which we always carried aboard. You might be interested to know that this engine change-out was made in about 30 hours by shipyard employees who had never done this before and at a total cost of approximately $1,700. What had happened is that a heat shield attached to the fuel manifold had vibrated loose and had cut the fuel mani-fold in the engine with a resultant fire. These heat shields are not necessary in marine serv-ice and we have subsequently removed the heat shields on both engines. At the time of this fire we had 5,018 hours on the engine with no significant failures. By the same token, both engines have provided continuous, completely satisfactory service with minimum maintenance. At the moment, I do not know what the overhaul cycle of the gas generator will be because we are still build-ing experience in this area, but my estimate is that it will not be necessary to overhaul these engines at lesser intervals than 8,000-10,000 hours. Overhaul will be done either by the manu-facturer or by firms specializing in this work for the aircraft industry. The substitution of a rebuilt gas generator is a very simple problem and one which can be accomplished during a normal turnaround, without delay to the ship. I cannot be too enthusiastic at this time about these engines. They have proved, to date, their worth in a continuous-duty service under rug-ged service conditions. This is not to say, however, that we have not had problems with the machinery installa-tion in the Callaghan. We have had lots of problems, but those associated with the en-gines have been, primarily, in the area of in-strumentation and control. The instrumenta-tion and control console, in my opinion, leaves much to be desired. The quality of the instru-mentation, the provision of power to the in-strumentation, the shutdown features of the instrumentation, have all given operational problems of no mean consequence. The reversing/reduction gears employed, al-though an extension of existing technology, are by far the largest by horsepower ever built for marine use and we are highly pleased with the maneuvering features provided by these gears. This reversing system, in conjunction with the rapid response of gas-turbine engines, is remarkable. The starboard high-speed idler gear lost por-tions of several teeth at a time which we have been unable to pin down and it was only through routine examination that we found this defect. The gears were dressed and con-tinued in service with the starboard engine running slightly below full horsepower. Dur-ing the guarantee survey a new gear was in-stalled and the ship is now back up to full speed on both engines. We expect that the reversing/reduction gears will continue to give us satisfactory service for many years to come. Based on the wear experienced to date, on the clutch bands, we believe that the original bands may very well last the life of the ship. In any event, it is not much of a job to replace these units. We look forward to continued profitable use of this ship in our service for many years. It is our hope that the lessons we have learned with respect to gas-turbine propulsion will be of value to the American merchant marine. 46 Maritime Reporter/Engineering News