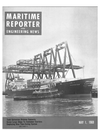
Page 10: of Maritime Reporter Magazine (May 1969)
Read this page in Pdf, Flash or Html5 edition of May 1969 Maritime Reporter Magazine
Puget Sound Tug And Barge Converts To Pilot Controlled Tugs Robert M. Keenholts* The principle of reduced manning for vessels properly equipped to operate with an unattend-ed engine room was agreed on between the Northwest Towboat Association and labor rep-resentatives during the 1968 contract negotia-tions. As a result of this agreement, several ves-sels have been equipped with the necessary and required equipment and are presently being operated with unattended engine rooms. Many of these vessels are capable of being operated on international ocean voyages; how-ever, their principal trade routes have been the Pacific Coast and Alaskan waters. This paper is based on the actual develop-ment, design, installation and operation of the alarm systems and automatic equipment in-stalled in several seagoing tugs by the Puget Sound Tug and Barge Company in 1968. Several systems for vessel automation being marketed were reported to be capable of do-ing the job. Each of these systems had to be engineered for each vessel. Of these package systems, none were available without consid-erable lead time, which meant they could not be installed for the summer season of 1968. In view of the above, the Puget Sound Tug and Barge Company chose to work out a sys-tem designed for their particular vessels. The Harris Electric Company, Seattle, Wash., was retained to design and manufac-ture pilothouse and engine-room panels, elec-trical circuitry for installation of the panels and the required alarm systems. They were also required to furnish the electricians to in-stall the equipment. There were basically three different types of vessels to be pilot controlled, the difference being the powerplants. Type 1?Heavy-duty four-cycle, direct re-versible Enterprise diesel engines, Model D.M.R.38, 2,000 hp with a-c auxiliary gener-ating plant. Type 2 ? High-speed opposed-piston, two-cycle, direct reversible with a reduction gear Fairbanks-Morse diesel engines. 1,500 hp with a d-c auxiliary generating plant equipped with batteries. Type 3?High-speed two-cycle, with reverse reduction gear Electro-Motive diesel engines up to 3,500 hp. Single and twin-screw installa-tions with a-c auxiliary generating power. Type 1 Modifications?The main engine on these vessels comes equipped with cylinder lubricators that must be refilled every few hours. A tank large enough to hold enough lube oil to last at least 24 hours was installed adjacent to the lubricator and piped directly to it. The tank was fitted with a low-level sen-sor. No other modifications to the engine were required. High-level alarms were also installed on the lube-oil service tank and the fuel-oil day tank to prevent overflowing when refilling. For the remote start of the auxiliary gen-erator engines, a solenoid pilot air valve actu-ating a piston-operated 'Airmatic' valve was installed in the existing air-start piping. A *Mr. Keenholts of Puget Sound Tug and Barge Company, Seattle, Wash., presented the paper con-densed here before a recent meeting of the British Columbia Area of The Pacific Northwest Section, The Society of Naval Architects and Marine En-gineers. pressure switch installed in the fuel or lube line automatically opens the cranking circuit when the engine starts. The generator discon-nect and load transfer was accomplished with installation of an Allen Bradley magnetic con-tactor, timing relays and 'Square D' voltage sensitive relays. A major problem with these particular plants was the inability of one generator to carrv the full vessel load under all circumstances. Rather than install a costly complicated sys-tem for remotely paralleling the generators, a circuit was designed to split the ship's lighting and power bus load between the two genera-tors. This was accomplished by using an addi-tional contactor similar to the transfer system, and was controlled with a pushbutton 'tie' switch installed in conjunction with the gen-erator transfer system. These start and transfer buttons were in-corporated in the engine room and pilothouse alarm panels. The pilothouse alarm panel was also fitted with voltmeter and ammeters for each generator. In the event of a generator engine or electrical failure, the standby gen-erator can be started from the pilothouse by pushing the start button. As soon as the unit comes u]) to full voltage it will automatically assume the ship's power load. In the event the generator operating becomes overloaded, which can be noted by ammeters in the pilothouse, the other generator can be started up. When this generator comes up to full voltage it is cut in by pushing the bus-tie button. The tie button activates the automatic transfer con-tactors which divides the ship's load between the two generators. The tow winch on these vessels is powered with hydraulic motors. The hydraulic pump for this system is driven by a diesel engine located in the engine room. A starting system identical to those used on the generator en-gines was installed together with the remote start and stop control in the pilothouse. The existing air compressors were driven by a power take-off from the generator engines and manually operated. Rather than automate their operation, a complete new automatic compressor set, electrically driven, was in-stalled. All the engine room alarm sensor alarm lights were installed in the door of a steel weather-tight electrical panel box on the after bulkhead of the pilothouse, together with the other alarms, generator meters, load-transfer switch buttons, generators and tow-winch-en-gine start buttons, the bus-tie transfer circuit button, alarm horn, engineer's call bell button, and circuit on indicator lights. The engine room alarm panel box is the heart of the system. The relays, timers and test circuit buttons are located in this box. This unit was mounted on the forward bulk-head on the upper engine room level. Operation of this panel is relatively the same as in the pilothouse with the exception of the test-circuit button. Type 2 Modifications?There was no main engine modification necessary. These engines are completely self-sustaining other than start-ing and maneuvering air. They are, of course, controlled from the pilothouse. The major problem in this case was developing a cam mechanism to shut the engine alarms off on stopping the engine. Inasmuch as the auxiliary engines were backed up with a 110-volt battery bank, remote start and transfer was not necessary. All the engine room alarm sensor lights were installed in the door of a steel weathertight panel box in the pilothouse. Because of the batteries, no remote and transfer controls were required. However, a voltmeter and am-meter were installed to monitor the ship's power. The engine room panel is approximately the same size as the one installed in the heavy-duty type. The alarm test circuitry was the same with the exception of the d-c current equipment which had to be used. The tow winch is powered with a d-c electric motor which is operable off the regular ship's power. Therefore, no special equipment was required for this. Type 3 Modifications?No major modifica-tions to the engine were necessary inasmuch as they were completely self-sustaining, other than control and starting air. The alarm re-quirements. however, were much more exten-sive than the engine manufacturer's original equipment. Therefore, a great deal of modi-fication was necessary to fit the required sen-sors and alarm equipment to the engines. The generators on this class vessel handle the full ship's load. Therefore, it was only necessary to install the auxiliary generator start and transfer system. This is identical to the installation in Type 1. The tow winch is powered with hydraulic motors on the winch with the hydraulic pumps driven through an electric clutch from the front end of the generator engines. This in turn is re-motely controlled in the pilothouse. The pilothouse on this class vessel was previously equipped with a console containing gauges, switches, meters and some alarm lights. Two methods were used to make the necessary installation. First was a supple-mental alarm panel similar to the other vessel installation, but much smaller, and containing only the generator start and transfer system, together with the additional alarms not pre-viously installed on the console. This panel was integrated with the console, utilizing the previously installed alarm lights. The second method was to install the new system on the existing aft panel of the console. Both systems worked equally as well. The engine-room panel was relatively the same as the Type 1 installation. However, because of the reverse reduction gears, it was more extensive. The panel was mounted on the forward bulkhead directly in front of the engine. This installation is equipped with an airflex clutch which is controlled from the pilothouse. The engine could be started and shutdown in the engine room only. Because of this, the Technical Committee ruled that an emergency shutdown be incorporated in the pilothouse equipment. This was accomplished by install-ing a pull cable attached to the main engine overspeed trip. it was also required that an emergency start or 'hot start' button be installed in the pilothouse in the event the engine was 'killed' or 'died' while the vessel was maneuvering. This was a simple matter of paralleling an-other start button in the pilothouse with the existing engine start button. For installation of the above alarms and supporting equipment, the best industrial and marine type equipment was used. Top quality industrial relays, oiltight transformer-type pilot lights (vibration resistant), and oiltight pushbuttons were used on all panels. These high quality installations have proven to be extremely reliable and trouble-free and have gained the confidence of the crews oper-ating these vessels. 12 Maritime Reporter/Engineering News