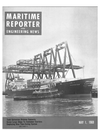
Page 16: of Maritime Reporter Magazine (May 1969)
Read this page in Pdf, Flash or Html5 edition of May 1969 Maritime Reporter Magazine
Advanced Computer Project Will Influence Structural Design Of Large Ships An important research development which is expected to have "a profound influence" on the review of structural designs of large ves-sels was revealed at the Annual Meeting of the American Bureau of Shipping, held recently in New York. Making the announcement, Andrew Neilson, the Bureau's chairman and president, said that the essence of the "Arizona Project", as this venture is called, is that the computer analysis of the entire hull structure of a giant vessel under expected service conditions can be un-dertaken. Although naval architects have used com-puters before to analyze ship plans, they have been able to investigate only individual sec-tions of the hull. However, this project will now make it possible to analyze in fine detail the shearing and bending stresses in the more highly stressed areas throughout the hull. The Arizona Project was started in the spring of 1968 by Chevron Shipping Company. Sub-sequently the Bureau was asked to join and the project is now sponsored by the company and the Bureau. It is under the direction of Dr. H. A. Kamel, professor of aerospace and me-chanical engineering at the University of Ari-zona and consultant to the Boeing Company. Computer analysis used for aircraft (which, like ships, consist of plated surfaces that have internal stiffening) had to be modified and ex-tended to take into account that the structure of a ship, as well as its responses, are somewhat different from those of aircraft. The program developed, called DAISY, which stands for Displacement Automated Integrated System, will be capable of treating the main hull structure. It is the most sophisticated com-puter program specifically created for the anal-ysis of the ship structure. How does this finite element method of in-vestigation actually work? The most important step in the procedure is the replacement of the actual continuous ship structure with a mathe-matical model. By passing longitudinal and transverse vertical planes and horizontal planes through this model, it is divided into a large number of elements of finite size having known elastic and geometric properties. Stresses are then calculated for the points at which these three families of planes or surfaces intersect. These points are located to coincide with the actual vessel's major structural frames and are called "nodal points". The process is perhaps best visualized by imagining a large net being wrapped around the hull of a ship. Each corner of the squares in the net represent a nodal point. Thus, the hull is systematically broken up into smaller pieces which are then mathematically tested for certain assumed operating conditions. The reactions evidenced by these individual seg-ments of the hull can then be used to assemble the resultant properties of the complete struc-ture. The smaller the elements being investigated, the more accurate the final analysis becomes. For example, in order to sharpen the compu-ter's focus on a point of special interest, such as a bulkhead, it is necessary to take the out-put obtained for this particular area from the initial three-dimensional run and then put it through the computer again, this time with a finer, two-dimensional mesh. To receive an ac-curate picture of the stress distribution in a component part of the bulkhead, a third run, utilizing an even finer mesh, might be required. One Chevron ship?Hull 520, a 210,000-dwt tanker under construction to ABS class at Kockums Mekaniska Verkstad AB in Sweden ?has already been intensively analyzed by DAISY. This vessel is also being extensively instrumented as part of a supporting program sponsored by the shipyard and the Bureau to measure the actual stresses occurring at sea in the vessel's hull. DAISY is also being put to work on five other Chevron ships of similar size which are building to Bureau class. Three of these vessels are following Hull 520 on the ways at Kockums, while the remaining two are being constructed by Mitsubishi Heavy In-dustries Ltd. in Japan. As a result of the Arizona Project, the Amer-ican Bureau of Shipping can look forward to the availability of proven three- and two-di-mensional programs of high quality for day-to-day use with designs for the larger vessels. Tubbs Cordage Realigns Operations In order to provide increased customer serv-ices, Tubbs Cordage Company will consolidate sales, accounting, and credit operations at the site of the manufacturing facilities, P.O. Box 709. 501 West Palm Avenue, Orange, Calif 92669 (telephone?714 538-1161). Simultaneous with this relocation, which be-came effective in April, regional sales for north-ern and central California, eastern Nevada, and the Oregon coast, will be handled at the reg-ional warehouse. 1441 16th Street, San Fran-cisco, Calif. 94103 (telephone?415 431-1919). Executive and export offices will continue to operate from 200 Bush Street in San Francisco (telephone?415 421-0927). Plus ? all the modern port facilities of San Juan, Puerto Rico. PUERTO RICO DRYDOCK & MARINE TERMINALS, INC. SAN JUAN, PUERTO RICO 00903 ^ P. O. BOX 2209 ? TELEPHONE 723-6010 ? 723-0769 > CABLE ADDRESS "DRYDOCK" J 1000 ft. concrete outfitting pier ? 691' reinforced concrete graving dock ? Floating drydock ? Four mobile cranes REPAIR at the CROSSROADS Ideally Located For Speed Economy and Convenience TANKER WORK A SPECIALTY ? New 2000 ton steel floating drydock ? Complete machine ? pattern ? boiler-plate ? electrical ? fabricating shops ? Foundry ? Design division Ideally located for voyage or annual repair enroute. A COMPLETE AMERICAN SHIP REPAIR SERVICE 18 Maritime Reporter/Engineering News