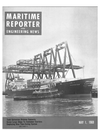
Page 7: of Maritime Reporter Magazine (May 1969)
Read this page in Pdf, Flash or Html5 edition of May 1969 Maritime Reporter Magazine
Motorized buildings equipped with plant services enabte workmen to subassemble sections under ideal conditions. Traveling carriers move subassemblies from the motorized buildings to the pier for installation on the ship. May 1, 1969 9 Special rolling rings hold box girder and position it for down-hand welding. Galveston Delivered? (Continued from page 7) wings, air-conditioned quarters, and special girders running almost the full length of the port and star-board sides. The normal conver-sion time is six months and Todd-Galveston has bettered the contract time by 30 to 40 days in some cases. When a vessel is so stripped, the question arises as to how the shell can be strengthened to prevent the hull from buckling. Not all engi-neers agree on the best way to do this. Some, for example, feel that doublers should be installed above and below the main deck and on the sheer strake. Todd-Galveston has come up with what it believes is a better way to do the job. Its principal ob-jection to installing doublers is that the work has to be done aboard ship and out in the open. The meth-od looks like a long-drawn-out way of solving the problem. The Todd solution consists in building box girders in sections up to 80 feet long ashore and then fitting them into the hull in one piece. The process is a simple one: after ballasting the vessel, sections of the sheer strake are stripped and prepared for receiving the box girder. When the assembly is com-pleted it is positioned on the ship by a crane and welded in place. These girders provide the struc-tural integrity needed while remov-ing the hull's interior structure. Constructing a box girder is also a simple and fast operation. First, structural steel is landed on a platen, and a motorized building rolled over the spot. Equipped with lights, gases, compressed air, and overhead cranes, the building en-ables workers to perform every op-eration from assembly to finishing under ideal plant conditions and without interruptions from the weather. The girder is put together in big motor-driven rolling rings that turn and position it for welding. This setup, besides saving time, enables a welder to work at all times in a down-hand position. The box girders raise the height of the deck two feet and in so do-Quotation from Thomas Edison hangs in the office of Ralph Anselmi, general manager of the Galveston shipyard of Todd. are eliminated. Or, by standing a bulkhead section against a crane-way and turning it as necessary, welders can perform more efficient-ly-At times, engineers at the plant who find they save time by per-forming assemblies ashore, have been able to find better and faster ways of doing a job aboard ship when work has to be carried out there. The heavy cables supplying power for refrigerated containers and hatch lighting, for example, in-stead of being hung overhead are tied together and laid on simple platforms in out-of-the-way places. With three other jobs in the works now, the Galveston yard ex-pects to have another busy conver-sion year. News of the company's know-how in this new shipbuilding specialty has traveled considerable distances?recently as far as Wall Street. Standard & Poor's wrote in February that Todd is "well situ-ated to benefit directly from the oncoming surge of work in convert-ing vessels to containerships." ing facilitate the handling of con-tainers when the ship is put in serv-ice. With the deck height increased two feet, the hatch coamings are only four feet high rather than six feet high. "We subassemble everything we can. It is the key to economy and time savings," says Ralph Anselmi, general manager of the Galveston Division. Besides the girders, the yard subassembles bulkheads, co-amings, hatch covers, the stack, wheelhouse, buttress posts, trans-verse girders, and water tanks. Even accessories are added ashore to save time. On the bulkhead, for example, the guide angle supports, safety rails, electrical fixtures,? even the clips for the fire hose boxes, are put on ashore. "There's a way to do it better?-find it" is a quotation from Thomas Edison that hangs prominently in Mr. Anselmi's office. His staff says he works near it and lives by it. Finding a better way often means the faster way. By assembling the wheelhouse in the motorized build-ing, for example, 14 to 15 crane lifts