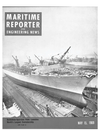
Page 40: of Maritime Reporter Magazine (May 15, 1969)
Read this page in Pdf, Flash or Html5 edition of May 15, 1969 Maritime Reporter Magazine
Gotaverken To Build Eleven 227,000-DWT Tankers New Flat Section Shop Adds To Yard's Capacity. Single-Side Welding Used For Shell, Bulkheads And Decks. Gotaverken's Arendal yord new flat section shop for one-side welding of plates. a high degree and all heavy work has been mechanized. The new shop thus represents a logical evolution of the Arendal concept of modern industrialized shipbuilding. The new shop is devoted entirely to flat sections. They comprise two or more strakes welded edge-to-edge and to which lengths of framing or stiffeners are welded. In shops further along the production line, these sec-tions?shell plating, bottom, deck and bulk-head units?are assembled together with other components to form the major "cubic" hull sec-tions. Plate and sections are delivered by rail right inside the shop, all unloading and storage be-ing under cover. At 14 functionally delineated work-stations the plates are first welded edge-to-edge in two, three or four strakes by means of automatic single-side welding. Certain flats are then turned 90° in the horizontal plane in readiness for the welding of stiffeners or frames by another automatic machine. The lengths of steel section are projected over the plates from the side by a special feeding station. All movement between stations is by roller conveyors. The only lifts involved are the placing of the plates on the conveyor at the first station and their removal at the end. The overhead crane which runs along the length of the shop is intended purely for the delivery of material to the welding ma-chines. The combination of single-side welding, which was a basic feature in the planning of the shop, and advanced mechanization prob-ably makes Arendal's flat-section shop unique at the present. The application of single-side welding in this instance was developed by Gotaverken and ESAB. Briefly, the system works as follows. The plates are located with the weld joint over a copper channel which is filled with welding powder. The entire arrangement comprising the copper channel and the plate-locating mag-nets is below the conveyor plane. Above this, the welding machine moves with its electrode and the weld is thus made from this side. Once the weld is complete the copper channel is lowered to a position at which slag is auto-matically removed and a new charge of powder applied. The entire process is fully mechanized and controlled from an operating console. The arrangements in the existing shops and the building docks are fully adequate for the work associated with this size of ship. In fact, the current 227,000-tonners will be the first hulls to utilize all the rows of bottom blocks in the building docks and the first for which it will be necessary to employ more than one of the hydraulic rams which push the growing hull down the ways as new sections are added in the covered assembly shed. In new workshop at Gotaverken's Arendal yard, profiles are welded to the plates by a fully automatic machine. Although the production system remains largely unchanged and shipbuilding continues in accordance with the 'traditional' Arendal method, the latest series of ships will none-theless involve certain novelties for the em-ployees. A number of meetings have there-fore been organized at the yard to ensure that all concerned, and particularly supervis-ory staff, safety officers and union representa-tives, are fully informed as to the future tasks. The novel features are mainly due to the large dimensions of everything associated with the ships. The effects make apparent the necessity of resetting piece rates. After all, what passes for a bracket in a 70,000-tonner must be regarded for rate-setting purposes as a plate in the case of a 227,000-tonner. The keelson of a 70,000-tonner is less than 13 feet deep. In the new ships the same part is 23 feet deep. In hulls of this size distances become so great as to introduce communication problems. A number of arrangements have therefore been made to assist access to the hull and movement within it. For example, 25-man lifts have been arranged for transport between the dock-sides and the upper deck, which will be 56 feet above quay level. A number of access holes will be cut in the deck and hull plating; and an additional lift will be suspended from the ship's counter and will remain in place until the completion of fitting-out. The result will be quicker movement in and around these big hulls than are normally expected in much smaller hulls. It is planned to complete each of the new tankers within about 140 working days total building time. This means a potential output in excess of four ships of this size per year. Maritime Reporter/Engineering News Recently the first section of the lead ship in Gotaverken's series of 227,000-tonners was erected in one of the two building docks at Arendal. Thus, the yard has made a start on the run of no fewer than 11 such vessels which are on order for owners in Norway, Hong Kong, Sweden, the U.K. and Liberia, with deliveries extending into 1972. The ships will have a length overall of 1,090 feet, breadth molded of 149 feet 7 inches and depth molded of 107 feet 4 inches. All will be powered by Gotaverken/Stal-Laval turbine machinery developing 32,450 shp. Now that the first section of the lead ship? which is for Smedvigs Tankrederi, Stavanger ?has been erected in the building dock, one can say that the Arendal yard has truly come into its own. The biggest ship previously built there, which incidentally is also the biggest yet built in Sweden, measured 120,000 dwt. Although Arendal was planned at a time when ships of over 200,000 tons seemed a relatively remote possibility, the production system can be smoothly adapted to the current series. A new shop for flat sections, which was recently inaugurated and represents an in-crease in yard output capacity, will ensure the maintenance of short delivery times, even for these big tankers. The 800-foot-long build-ing housing the new shop is aligned parallel with the materials flow through the existing shops. Together with machinery, roads, etc., the new shop involves the investment of over $3.5-million. In comparison with traditional shipbuilding methods, the latest addition to Arendal is a conspicuously advanced facility. Very big hull sections are built on genuine assembly-line principles. Specialization has been carried to First 227,000 tonner starts to project from the hull as-sembly hall as sections are added inside the building. 44