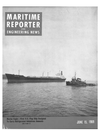
Page 12: of Maritime Reporter Magazine (June 15, 1969)
Read this page in Pdf, Flash or Html5 edition of June 15, 1969 Maritime Reporter Magazine
Center For Maritime Studies Reports U.S. Shipbuilding Costs Can Be Cut 25% Hillman Barge Delivers Six Double-Skin Tank Barges An intensive, in-depth study of the U.S. shipbuilding industry released recently con-cludes that costs of U.S.-built ships in an im-proved procurement environment could be re-duced by as much as 25 percent. The 145-page report, entitled "Improving the Prospects for United States Shipbuilding," was released by the Center for Maritime Stud-ies, a research organization at Webb Institute of Naval Architecture, Glen Cove, N.Y. It culminates an 18 month multi-discipline study involving naval architects, marine engineers, economists, industrial engineers and business executives familiar with shipbuilding and op-eration. The report examines all the direct and in-direct factors which affect shipbuilding prices and efficiency, including quantities and types of ships ordered and effects of possible ship-yard capital improvements. Additionally, the report assesses cost and performance of for-eign shipyards. In a clear concise manner, the report clears up a popular misconception that productivity levels of the domestic shipbuilding industry are inferior to other U.S. construction indus-tries and foreign shipbuilders. Comparing domestic shipbuilding price trends with those of the commercial building industry during the past 10 years, the study found that while build-ing prices rose about 30 percent in this period, prices of new cargo ships remained nearly con-stant and tanker prices decreased considerably. This, it is concluded, attests to the gains in shipbuilding productivity. The comparison of U.S. and foreign ship-building industries, using tanker construction to gauge relative productivity, showed that the U.S. is more efficient than Japanese and British yards and slightly behind the better shipyards in Sweden and West Germany. Despite this favorable level of productivity, higher U.S. wages prevent domestic shipyards from competing in the international shipbuild-ing market. Thus, although Japan's produc-tivity is about 79 percent of the U.S., its wage rate is only about one-fourth that paid by U.S. yards. To meet Japanese shipbuilding prices, currently about 50 percent of the U.S. levels, U.S. yards would have to increase productivity 2J/2 times. Although such an increase was not found to be feasible, significant improvements in U.S. shipbuilding productivity would be expected to follow the inauguration of a long-range building program. The resulting stabilized production conditions in individual shipyards would not only lead to the economies of multi-ple production, but would permit accelerated investment in new capital equipment. It is shown that for different rates of output there are different optimum levels of investment. The report states that with a long-range shipbuilding program?involving at least five or six similar ships per year in each participat-ing yard?substantial cost reductions could be achieved. It notes that in recent years the domestic shipyards have received contracts to build relatively few merchant ships, the num-ber in each yard varying from year to year. These ships involved a wide variation of de-sign which, it is pointed out, precluded the cost savings that accrue from repetitive production of similar ships. Following are some of the key conclusions and recommendations of the study: 1. The single most important requirement for improved efficiency in U.S. shipbuilding is a stable long-range production situation. Only a relatively few merchant ships have been or-dered annually in recent years and the ship construction programs have been uncertain and variable in character. This lack of stability has handicapped U.S. shipyards' efforts to re-duce costs. 2. U.S. shipbuilding programs should be predicated on building ships in quantity. The number of vessels of similar design to be built in each participating yard should be as large as practicable, utilizing to the greatest extent feasible basic designs applicable with minimum differences to different owners?or standard major components, such as powerplant and stern. Significant cost reductions would result from building ships in groups of 30 or more over a five-year period. 3. A stable shipbuilding environment with long-term, multiple construction programs un-derway would encourage shipyards to increase their expenditures for more efficient produc-tion facilities. The optimum is found to be above the present level of investment. 4. A natural consequence of industry stabili-ty would be a trend toward designing ships for production economies. Significant cost re-ductions can be realized by a more rationalized approach to ship design to eliminate features which add measurably to construction costs. Simplification of structure and hull outfitting, and modular construction of crew accommoda-tions and powerplant, also would provide ma-jor cost savings. 5. Shipyards must continue to upgrade their management techniques. Ways and means must be found to attract and retain highly competent young professionals in a variety of disciplines including industrial engineering, production planning control and cost account-ing systems, as well as naval architecture and marine engineering. 6. Accelerated research and development programs aimed at improved ship construction techniques are urgently needed. In addition to projects to produce ship designs for "produci-bility," emphasis should be placed on the de-velopment of improved shipbuilding proce-dures. Significantly, many of the cited advance-ments in shipbuilding facilities and techniques are already employed by American shipyards. These include: numerical lofting and tape con-trol for plate layout and cutting, automatic welding and advance outfitting of subassem-blies. However, the United States, in compari-son with other shipbuilding nations, was found to be deficient in organized shipbuilding re-search and development activities. Such efforts abroad are usually jointly funded by private industry and government. Here in the United States, government support or participation in such projects is virtually nil. Most of the ship-building research is carried out by the in-dividual yards which, for competitive reasons, are reluctant to exchange information with oth-er shipyards. It is recommended that one or more shipbuilding research groups be estab-lished to coordinate the efforts of individual organizations, government agencies and pri-vate shipyards. Miss. Marine Building Two Twin-Screw Towboats Mississippi Marine Corp., Greenville, Miss., is constructing two twin-screw towboats for stock purposes. To be powered with 670-total-bhp die-sels, each towboat will have the following dimen-sions: 65 feet in length, 20 feet in beam and 9 feet in depth. This semi-integrated double-skin tank barge, shown after launching at the Hillman Barge & Construction Company's Brownsville, Pennsyl-vania shipyard, is one of six 200-foot by 35-foot by 12-foot units delivered to the Upper Missis-sippi Towing Corporation and Hennepin Towing Company. Three of these barges are certificated by the U.S. Coast Guard for Lakes, Bays and Sounds Service and have a Special Service Load Line. The other three barges are classed by the American Bureau of Shipping for Unlimited Service and certificated by the U.S. Coast Guard for Ocean Service. The hull is divided into 16 watertight com-partments and two cargo tanks. Between the car-go tanks, is a cofferdam pump room which mini-mizes the length of cargo piping between the two tanks, and permits the carriage of mixed cargoes that require segregation. Both the American Bureau of Shipping and the U.S. Coast Guard have approved these hulls as Type I Tank Barges. The barges are designed to carry a wide range of liquid products, from Grade A petroleum to the heavier liquids of 2.0 specific gravity. The total volume is 10,300 barrels with a cargo ca-pacity of 1,354 tons at an 8-foot 6-inch draft. The cargo tank bottom is coiled with 6-inch ship channels. Each tank has four independent banks of channel coils, complete with drain piping and condensate overboard system. The cargo system, including suction, fill and discharge piping is independent for each tank. All piping and fittings are schedule 10 stainless steel. The cargo pump, a Blackmer model HXLS-8B, is vertically mounted in the cofferdam pump room and is hydraulically driven through a Link Belt gear reducer. Hydraulic power is provided with two Vickers pumps driven by a GM 4-71 diesel engine. This type of double-skin tank barge is consid-ered most versatile in the transportation of liquid chemical products. The isolated piping systems al-low carriage of various combinations of cargoes. The designed tank volume, and heavier scantlings provide for a cargo of maximum tonnage, re-gardless of the specific gravity of the commodity. On the basis of the Type 1 hull design, a wider range of products can be loaded. With minimum conversion, poisonous commodities can be carried. Atlantic Container Promotes Caffaro And van Campenhout Atlantic Container Line, Ltd., New York, N.Y., has announced the appointment of J. T. Caffaro as equipment control manager and W. A. J. van Campenhout as assistant marketing manager. Mr. Caffaro formerly had been assistant manager,equipment control. Mr. van Campen-hout had been manager, ocean rates and con-ferences. The two promotions are the latest in a series of changes taking place at Atlantic Container Line in preparation for the expansion of the company's operations by the addition of six new roll-on/roll-off containerships in the next 12 months. The line currently operates four 14,200-ton ro/ro containerships in trans-At-lantic service. 14 Maritime Reporter/Engineering News