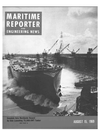
Page 8: of Maritime Reporter Magazine (August 15, 1969)
Read this page in Pdf, Flash or Html5 edition of August 15, 1969 Maritime Reporter Magazine
Bethlehem Sets Early 1970 Completion For Largest U.S. Floating Dry Dock Lilliputian-like trucks and figures of men drawn to scale emphasize the mammoth size of the new all-steel floating dry dock now under construction at Bethlehem Steel Cor-poration's San Francisco shipyard. The largest floating dry dock in the United States, designed to han-dle tankers ranging to approxi-mately 150,000 dwt, is now under construction at Bethlehem Steel Corporation's San Francisco ship-yard. The new multi-million-dollar all-steel dry dock is scheduled for completion early in the spring of 1970. It will have an overall length of 900 feet and will have a clear width of 150 feet between wing-walls. It is designed for 37J4 feet of water over the keel blocks and will have a lifting power of 65,000 tons. The dock is being built in four quarter sections with the first sec-tion scheduled to be launched ap-proximately October 1. The design calls for unit (continuous, nonsec-tionalized) construction with a watertight buoyancy chamber the full depth ami length of the 800-foot-long pontoons. Wingwalls are 66 feet high and 18 feet wide with a watertight safety deck feet below the wingwall weather deck. This area provides space for pump motors, substation equipment, pip-ing and other utilities. At full sub-mergence, the safety deck will be below water and is protected against flooding by watertight compartmentation. The four L-shaped quarter sec-tions will each be 93 feet wide by 400 feet long when launched. After launch, the port and starboard for-ward quarter sections will be joined in the water by a special welding procedure. While this is being accomplished, construction will proceed on the last two quar-ter sections which, when similarly joined, will finally be welded end-to-end with the first two. Then the inboard and outboard aprons will be added to bring the overall length to 900 feet. About 15,000-tons of Bethlehem steel shapes and plate will go into its all-welded construction. Of this, 2,300-tons of Mayari R high-strength steel is used in high stress or corrosion problem areas, with the remainder being ASTM A36. Plate thickness varies from 7/16 to 3/4 inch. Fabrication of this steel has been set up on a production line basis. A feature of the fabrica-tion technique involves using a sin-gle pass, one side, automatic weld-ing process to join the 7/16-inch, 40-foot-long plates into deck and bottom sections 50 feet wide. The flooding and dewatering sys-tem consists of 40 ballast compart-ments. Each compartment is fitted with a motor-operated butterfly flooding valve, and a mixed-flow pump located on the safety deck. Flap valves are used as checks. Both the check and flooding valves are accessible from outside the dry dock for maintenance. All pump motors and valves are operated from a console in a con-trol room located at the weather deck. The console provides in-formation on the position and op-eration of the valves as well as data from the water level indicators and the draft gauges. A complete inter-com system is used to keep the dockmaster in contact with his crew. In order to provide a flush sur-face on the pontoon deck, the. keel block system which supports the drydocked vessel uses a combina-tion of sand, wood and concrete blocks. These blocks can be preset by forklift trucks to reduce dock-ing time. Control of corrosion is provided by a four-part system. The system uses cathodic protection in the low-er 10 feet of the pontoon compart-ments, polar oil in the upper por-tions, and cathodic protection on the outer underwater hull area with coal tar epoxy specified for the upper exterior areas. Construction of four mooring dolphins and about 30,000-square-feet of high water approach plat-forms is scheduled. Both the plat-forms and the dolphins will be con-structed of steel-reinforced con-crete supported by steel piling. The heaviest of these pilings will be made of 24-inch-diameter concrete-filled pipe, 186 feet long, driven to support loads of 200 tons each. On the top of each of the two wingwalls, a 60-ton-capacity travel-ing crane will be installed. Each crane will be equipped with a 90-foot boom with a 20-foot jib. With a spreader bar, the two cranes will be able to handle a load of 120 tons at the center line of the dry dock. Fourteen capstans will be used to handle the lines for positioning the ship in the dry dock. The dry dock will be well serv-iced with all necessary utilities. Advanced types of mercury light-ing will be used on the dry dock, including submersible floodlights in the wingwalls at the pontoon deck to provide night-time illumi-nation of ship's bottoms. Consideration has been given to the pollution problems of San Francisco Bay by the designing of a sewage disposal system into the dry dock which can accept dis-charges from ship scuppers and transport it into the yard's sewer system and then to the city's dis-posal plant. This is believed to be the first such system ever to be incorporated into a floating dry dock. West Coast Firms Order Three Barges From Todd-Houston Awards totaling approximately $3,500,000 for the construction of three large barges have been re-ceived from West Coast interests by the Houston Division of Todd Shipyards Corporation, according to General Manager Arthur W. Stout Jr. Mr. Stout's Division also will share in the $25,000,000 award re-cently made to the Todd Corpora-tion by United States Lines for the conversion of three Mariner-class cargo ships into containerized ves-sels. The Houston Division expects to build the hatch covers and do other miscellaneous fabrications for the lead conversion yards. This container conversion work plus the three new barge construc-tion contracts should keep the em-ployment demand at Todd-Hous-ton at current levels through the end of calendar year 1970. Cunningham Named Marine Fuel Sales Manager For IPS Ernest E. Cunningham Jr. Ernest E. Cunningham Jr. has been named manager, marine fuel sales of Independent Petroleum Supply Company (IPS) according to Edmond J. Dusesoi, vice-presi-dent. Mr. Cunningham's responsibili-ties include advancing IPS' world-wide bunkering interests and, in particular, supervising the sale of marine bunker fuels for The West Indies Oil Company, Limited (WIOC) at Antigua, West Indies. IPS is a Natomas Company sub-sidiary handling petroleum trans-actions and tanker activities for the Natomas Group. This includes the buying and selling of petroleum crude and products and acting as petroleum and tanker brokers, both for affiliates and others. The firm's New York office is at 277 Park Avenue and other offices are located in San Francisco and London. Mongo Becomes V-P At T. I. Stevenson Eugene S. Mongo has joined T. J. Stevenson & Co., Inc., of New York as vice-president, the steam-ship agency announced. Mr. Mon-go who formerly served as vice-president of Jan C. Uiterwyk & Co., Inc., will now be concerned with the west coast of South Amer-ica trade in which Stevenson acts as general agents for Peruvian State Line. REPAIR DIVISION OF ASTILLEROS DE CADIZ, S.A. has maintained a high level of activity at the firm's Cadiz, Spain, yard. Shown in this recent photograph are the 103,700-dwt British tanker Bamford, the 97,350-dwt tanker Zaragoza of Cia. Espanola de Petroleos and the 40,290-dwt Norwegian tanker Jakinda being repaired at one time. 10 Maritime Reporter/Engineering News