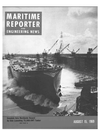
Page 32: of Maritime Reporter Magazine (August 15, 1969)
Read this page in Pdf, Flash or Html5 edition of August 15, 1969 Maritime Reporter Magazine
A Low-Cost System For Ocean Transportation Of Iron Ore "Marconaflo" Proves Successful This New Method Of Handling Ores Will Make The Multi-Purpose Ship Of The Future A Tanker Thousands of tons of slurrified iron ore are pumped from the SS Oread into storage pond at Oregon Steel Mills. Slurried ore is reclaimed by the dredge on the pond. A new low-cost system for ocean-transportation of iron ore which has revolutionary economic im-plications for the world's steel-makers and all raw material ship-ping has been announced by Mar-cona Corporation, San Francisco, Calif., prominent mining and trans-portation company. C. W. Robinson, Marcona presi-dent, said use of the system, named "Marconaflo," in a successful July 3 delivery of 4,000-long-tons of Marcona superconcentrate iron ore from Peru to the new Portland, Ore., plant of Oregon Steel Mills demonstrates its commercial via-bility. Marcona has recently concluded a contract calling for delivery of more than two-millions-tons of slurried iron^ore concentrate to Oregon Steel, an affiliate of Gil-more Steel Corporation of San Francisco. I t C. W. Robinson President, Marcona Corp. Marconaflo, which permits load-ing and discharging of iron ores and other mineral concentrates in slurry form, makes it possible to transport these materials in large, high-economy tankers, rather than by traditional bulk carriers. An im-portant element in this system is the method of slurrying cargo after it has hardened or compacted in the ship's hold. Using Marconaflo, large tankers can now make deliveries anywhere in the world, lie offshore in deep water, and pump slurrified cargo into a pipeline, rather than relying on conventional port facilities that often cannot handle the big eco-nomical bulk carriers. "Marconaflo reduces direct pow-er and handling costs of loading and discharging iron-ore concen-trates by as much as 90 percent from the cost of conventional ship unloading systems," Mr. Robinson said. "It is that reduction, coupled with the minimal facilities required for pipeline loading and discharg-ing, which lends significance to the development of this system." The new superconcentrate iron ore being produced at the San Ni-cholas Bay, Peru, facility of Mar-cona Mining Company has iron content of approximately 70 per-cent compared with standard con-centrates of 65 percent iron or less. "This new, higher concentration ore, coupled with the benefits of Marconaflo slurry delivery, will en-courage development and construc-tion of smaller, regional steel mills throughout the world," said Mr. Robinson. "This type of mill will eliminate requirements for the high cost of a blast furnace and related facili-ties by using the direct reduction process in combination with an electric furnace and continuous casting. Held in storage tanks or ponds after delivery, the ore can be pelletized, subjected to direct reduction, then fed to electric fur-naces for steel production." The system also offers a signi-ficant advantage in reduced raw material transport costs for coastal plants refining and processing non-ferrous minerals, such as copper, lead, zinc, manganese, and so forth. "The need for greater economy and efficiency in handling ores and mineral concentrates was our basic reason for developing the new pro-cess," said Mr. Robinson. "It is now possible to gain such savings in the ocean transportation of these commodities that many marginal ore deposits will become econom-ically attractive." He predicted that use of Mar-conaflo will make the multi-pur-pose ship of the future a tanker, carrying petroleum products to one port, with return cargoes of slur-ried iron ore or other mineral con-centrates. The tanker will be "the dry cargo vessel of tomorrow going to a? much as 500,000 dwt without port limitations, since the entire cargo can be discharged in slurry form from offshore deep-water moorings." Prior to development of the Mar-conaflo system, it was not practical to ship fine ore concentrates in slurry form due to their extremely dense compaction in transit. Ship-pers were compelled to use dry-bulk handling techniques, which meant loading from conventional docks, deeper dredging of harbors with increased ship size, and cum-bersome, expensive dockside equip-ment. In the Marconaflo process, ore concentrates are pumped aboard ship at approximately 75 percent solids. After settling, most of the water is drawn off, leaving a non-shifting cargo of over 92 percent solids, or less than 8 percent water ?only slightly above the water content of conventional bulk con-centrate shipments. On arrival, special high-pressure water jets developed by Marcona are employed in the ship's cargo holds to liquify the cargo for pump-ing ashore. Research on the Marconaflo pro-cess has been conducted since 1966 at the company's San Francisco headquarters, with development carried out at the San Nicholas Bay, Peru, facility of Marcona Mining Company. Marcona Mining has extensive iron ore holdings in Peru and currently plans a $25-million expansion of its processing plants there. In the experimental phase of Marconaflo, one hold of the com-pany's SS Allen D. Christensen was modified for slurry handling. On June 8, 1968, that vessel dis-charged the world's first slurry shipment of iron ore at the Chiba Works of Kawasaki Steel Corpora-Peruvian iron ore pouring into storage pond at Oregon Steel Mills. tion, Japan?some 3,000-tons of ore. Renamed SS Oread, the same vessel made the July 3 delivery to Oregon Steel Mills. Work is now underway at the Asa no Dockyard of Nippon Kokan, Japan's only integrated shipbuild-er-steelmaker, to convert Marcona's SS San Juan Merchant for trans-portation of slurry by the Marcon-aflo system. The vessel will then be the first carrier capable of transporting 50,000-tons of ore, slurry, or oil. Conversion is sched-uled for completion by November of this year. Nippon Kokan built the original vessel for Marcona in 1959 as an ore/oil carrier. This ves-sel will be employed for delivery of ore concentrate under contract with Oregon Steel Mills. Marcona is one of the world's largest mining and ocean trans-portation firms and is owned prin-cipally by Utah Construction & Mining Co. and Cyprus Mines Cor-poration. In 1968, the company shipped nearly 13.5-million-tons of iron ore from Peru and Australia. From 1952 to 1968, Marcona mined and shipped 70-million-tons of iron ore from Peru. The largest individual supplier of iron ore for Japan's steelmakers, the company supplied that nation with 11.8 mil-lion tons in 1968. The Marcona-operated fleet in-cludes 40 ships totaling more than 2.5-million deadweight tons, with three 130,000-dwt ore/oil carriers now under construction in Japan for delivery in late 1969 and early 1970. The company also ships large quantities of oil, coking coal, alumina, salt and other cargoes. 34 Maritime Reporter/Engineering News