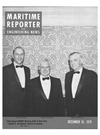
Page 36: of Maritime Reporter Magazine (December 15, 1970)
Read this page in Pdf, Flash or Html5 edition of December 15, 1970 Maritime Reporter Magazine
Syncrolift System Employed In Unusual Dockings
At Lemont Shipbuilding And Repair Company
Some of the barges dry-docked at Lemont Shipbuilding and Repair are placed upside down (as the one shown above) on the 1,700-ton Syncrolift for downhand welding and less hazardous working conditions.
Marine Steam Powerplants— (Continued from page 37) "The PPR (Positive Protection Reheat) concept was devised," according to the authors, "utilizing means both internal and external to the boiler for protecting the reheater. The basic design features of this boiler, shown in Figures 2, 3 and 4, could be used to an operating pres- sure of 1,485 psig and an output equivalent to 40,000 shp per boiler."
The authors then described several boiler de- signs and concluded that with sound engineer- ing and operating practice, with emphasis on oil burner and water-chemistry control tech- nology, modern marine boilers should provide unlimited availability and designed efficiency throughout the life of the ship.
Applications
Mr. Spears spoke on the applications of pres- ent designs of steam propulsion systems. He said, "While there has been a general trend to higher and higher powers, the developments of the past few years have been astounding. A number of recent inquiries have considered power levels to 200,000 hp. This power has been distributed on two or three propellers.
The message I want to leave is that the steam propulsion-plant designs to provide power this high, or higher, economically and reliably are available whenever you need them. Turbine and gear designs are available and good boil- ers are available to provide steam. The feed pumps, fans, condensers and other auxiliaries have been designed and performance data are ready. "As an example of what has been done, the curves numbered 1 in Figure 5 show the ex- pected fuel consumption of non-reheat steam plants up to 200,000 hp. Curve numbered 2 gives the same data for a reheat plant. You will note that in both cases the fuel perfor- mance continues to improve as the power in- creases."
Summary
Mr. Simpson summarized the seminar as fol- lows: "We find ships to be inherently complex and the environment unusually difficult. We believe that progress will result from building on what we know with hard work and good management. From that perspective, we have attempted to demonstrate that steam plants are available now for whatever application you need. Time and money-consuming develop- ments are not needed. We all have a wealth of experience to profit by. The hardware and systems are proven in the environments."
Wilson Issues Bulletin On New
Handhole Seat Grinding Kit
Thomas C. Wilson, Inc., Long Island City,
N.Y., has announced publication of Bulletin TC- 7007 which details their new handhole seat grind- ing kit for restoring boiler handhole seats. The kit described in the bulletin features a portable, air-driven motor complete with all accessories that might be required to restore to as-new con- dition corroded, pitted, scratched or fluid-abraded seats of virtually any size or shape in boilers or ferrous pressure vessels. Designed for use in ship- yards, on board ship, and in power plants, the kit features rugged construction, rapid grinder align- ment, accurate control of cutting, interchangeable roll guides and quick setup.
Copies of Bulletin TC-7007 may be obtained by writing Thomas C. Wilson, Inc., 21-11 44th
Avenue, Long Island City, N.Y. 11101.
Lemont Shipbuilding & Repair Company, a modern, fully-automated shipyard located at
Mile 300 on the Illinois Waterway, services dry cargo barges, tank barges, river tugs, and Great
Lakes tugboats. The company has a 1,700-ton rated capacity Syncrolift dry dock designed by
Pearlson Engineering Company, Miami, Fla., as the hub of their entire operation. The shipyard complex is headed by Ken Blackburn, and he states that they can now dry-dock every type of vessel that plys the inland waterway system. He has found their dry dock to be the most valued piece of equipment in the shipyard, and some of the best "workhorses" on the river have al- ready been lifted on the Syncrolift platform.
The Syncrolift dry dock installation was com- pleted in October 1969, and during its first month of operation, 20 commercial vessels were dry- docked. Since then, the transfer area has been extended, and several barges and tugboats are handled simultaneously.
Barges dry-docked in the conventional upright manner can sometimes involve time-consuming preparation of high blocking to provide working space. Hazardous working conditions and over- head welding can be eliminated by inverting the barge and placing it in dry dock upside down.
With this procedure no high blocking is needed,
No. Calif. Section Discusses
Design Of Special Ships
To Transport Forest Products
Pictured left to right: Graham Fraser, past chairman,
Paceco; Vincent Van Riper, principal surveyor, American
Bureau of Shipping; Henry Kozlowski, Technical and re- search chairman, Matson Navigation, and J.H. Troyer, secretary treasurer, Todd shipyards.
The November dinner meeting of the North- ern California Section of The Society of Naval
Architects and Marine Engineers was attend- ed by 62 members on November 12 at the En- gineers Club in San Francisco.
Section vice chairman Arthur Haskell pre- sided at the meeting. A paper describing the design of special ships for the Swedish Forest
A huge barge under repair at Lemont Shipbuilding over- hangs the 220-foot Syncrolift platform by 86 feet. and work can be carried out in a safer, more effi- cient manner.
It is interesting to note that although the Syn- crolift dry dock platform is only 220 feet long, barges over 300 feet in length are easily handled.
Read-outs on the panel of the control center in- dicate the actual loading at each Syncrolift hoist.
Safety provisions in the control center prevent any hoist from being overloaded.
Pearlson Engineering Company, designers of the Syncrolift dry dock, supplied the hoisting equipment and electrical components. All other materials and their installation, was accomplished by Lemont Shipbuilding and Repair Company.
Products Company, Svenska Cellulosa AB (SCA), was presented by Robert W. Herbert, a San Francisco naval architect. The paper emphasized that the ships involved were re- garded simply as a part of a new distribution system in their design and construction. The owners distribute about 800,000 tons of forest products annually, principally newsprint, from
Sweden to the United Kingdom and Central
Europe.
Shown at the San Francisco meeting, left to right: Nor- man Thompson, papers chairman, Marcona Corporation;
Arthur J. Haskell, vice chairman, Matson Navigation;
Robert N. Herbert, author; Joseph H. Busch Jr., meetings chairman, H.J. Wickert Co., and J. Randolph Paulling
Jr., academic liaison chairman, University of California,
Berkeley. 38 Maritime Reporter/Engineering News