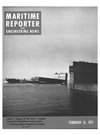
Page 11: of Maritime Reporter Magazine (February 15, 1971)
Read this page in Pdf, Flash or Html5 edition of February 15, 1971 Maritime Reporter Magazine
-m
Isllllllfee Sift a -i" i
Pictured at the meeting, held in the Seamen's Church Institute, left to right: (standing)
H.J. Karsch, J.J. Henry Company; Henry M. Tiedemann and Monroe Macpherson, members of the Section's executive committee, and Charles W. Wilson, secretary- treasurer of the New York Metropolitan Section; (seated) W.J. Dorman, J.J. Henry
Company, author; Norman R. Farmer, Section vice chairman; Warren I. Signell, chair- man, and Robert G. Mende, national secretary of The Society of Naval Architects and
Marine Engineers.
Containership Design- (Continued from page 10) ing of a hold up to the bulkhead deck. They must ke kept as narrow as possible in the transverse dimen- sion in order to avoid wasting valu- able ship beam space. As a result, these girders are of little use in com- pression, and are often prevented from taking excessive compression loads by fitting suitable "slip" con- nections at their span ends. They are ignored in the hull girder section- modulus calculation as making no contribution to the overall strength of the vessel.
Container Strength—The depth of the ship determines the number of tiers of containers that can be stacked below deck. Current contain- er design standards are based on the assumption that they are stacked to a maximum of six high. Increasing the number of tiers decreases the need for a high deck load and, therefore, affords better container protection and simplifies the lashing problem.
However, it decreases the initial sta- bility due to a rise in the KG of the light ship and also increases the load- ing-cycle time.
An increase in ship's capacity will require the stacking of containers more than six high in the holds. The use of reinforced containers for cer- tain locations would appear the ob- vious answer. However, this places an additional constraint on the load- ing operation which may well render this economically not feasible. As an alternative, it may be practical to provide a system of intermediate hinged brackets over the lower five containers in a hold and have these brackets support an additional three or four tiers. Such a support system may be space consuming and may require remote control, but it can pos- sibly be justified after suitable re- search.
Shoreside Handling Facilities—
A very deep ship requires greater ver- tical movement of the containers.
Time for this greater movement is a definite consideration. Increased hull depth as a characteristic of a "big- ger" ship automatically involves in- creased beam as well as increased length. Our current knowledge of ex- isting shoreside container-handling facilities indicates that a beam of 112 feet is the maximum that can be han- dled from one side of a containership, and such a facility only exists in a few of the major seaports.
Length and Beam—The length and beam of a containership is cur- rently limited by the following con- siderations : 1. The constrictions of the Pan- ama Canal have an impact on U.S.- flag shipping and the ships of other flags. 2. The large containership usually is required to enter a port where there are physical constraints.
Seaway Stresses
The forces acting on a very big containership are no different than those acting on a very big tanker.
However, the structural resistance to these forces by the hull of the con- tainership is much more difficult to achieve.
In longitudinal bending a tanker presents an evenly balanced hull gird- er with a full, solid deck and equiva- lent bottom shell. The containership has a stiff double bottom for the bottom flange of the hull girder, and this must be balanced as much as possible by two compact longitudinal box girders, with open hatchways to- taling often more than 80 percent of the beam.
The containership, due to the ar- rangement of its structure, is at a disadvantage in torsion. Not only does it have to resist the same tor- sional moments as the tanker but due to the location of its shear center at or below the keel, the horizontal loads create, in addition to horizon- tal bending moments, additional tor- sion moments of considerable magni- tude with attendant large warping stresses and deflections. The axial stresses due to warping cause a rela- tive movement between the port and starboard sides which, except for the closed ends forward and aft, is re- sisted only by the transverse deck girders supporting the hatches. High stress concentrations may be expected at the connections of the transverse deck girder to the longitudinal box girder.
The determination of sea loads and stresses follow at first the convention- al procedure, namely, the calculation of the still water bending moments and poising the ship at a heading of 180 degrees on a wave equal to the ship's length. Due to the fineness of the ship, one finds that the maxi- mum allowable longitudinal bending stresses, instead of reaching a peak amidships, as on a tanker, are difficult to keep from exceeding the maximum over the midship half length. This is one of the reasons that this procedure of determining wave-induced stresses is not sufficient for a containership.
Although the longitudinal bending moments do not change appreciably due to a change of heading of say ?0 to 30 degrees, the horizontal bend- ing and torsion moments increase con- siderably and may cause stresses reaching a maximum at about the quarter length of the ship, superim- posing some of their components on the longitudinal bending stress. So far, only static stresses have been considered. Thanks to the latest de- velopments of the strip theory, it is now possible to determine, presuma- bly with a fair degree of accuracy, the dynamic and hydrodynamic forces acting on the hull. By calculating these forces due to waves of varying direction and length, the short-term distribution of stresses may be de- termined by superposition. Subse- quently, the short-term distributions obtained are superimposed with the aid of seaway statistics to one singu- lar long-term frequency distribution.
On the basis thereof is then deter- mined the stress value that is on an average exceeded once during a giv- en number of load cycles.
In addition to the stresses so ana- lyzed, the high-speed containership may be subject to another phenome- non, namely, stress magnification due to wave-excited two-noded hull vi- bration. Although the ship speeds are still low enough so that the frequency of encounter of resonance occurs at the low energy part of the sea spec- trum, the magnification still could be considerable. Unfortunately, the cur- rent state of the art does not permit a rigorous analysis.
Stability
The large, fast containership has all the trim and stability problems in- herent in other ship types and then some. The large sail area presented by the high freeboard and a high deck load of containers has a pro- found effect on the required GM.
On the other hand, beam restrictions do not permit ample waterplane in- ertia. The result is a ship with a high KG and relatively low GM. Ex- cept for ballast conditions, the GM for various loading conditions varies in a rather narrow range since the weight of the fuel consumed is com- pensated for by taking on ballast water. Maximum flexibility dictates minimim use of fixed ballast. High speeds require large bunker capacity and the desirability of a clean ballast system usually makes it difficult to find adequate space for liquid ballast.
Another aspect of the high KG and relatively low GM is the large heel angle experienced by the ship when traveling at high speed caused by sudden large rudder angles. (These maneuvers can be quite dangerous, especially if the helms- man tries to correct the situtation by giving opposite rudder.)
Vibrations
Aside from any mechanical unbal- ance of the propulsion system, the propeller is the source of vibrations.
The fact that, due to high power and low draft, most high-speed con- tainerships are twin-screw is a bless- ing and at least reduces the propeller excitations due to wake inequality.
It is unfortunate that little or no full-size experience is available for contra-rotating or overlapping pro- peller arrangements.
It has been determined that hori- zontal vibrations are more difficult to endure by the human body than vertical vibrations. Unfortunately, the containership response is much more susceptible to high horizontal vibrations due to its low torsional rigidity and considerable coupling of horizontal and torsional vibrations.
The torsional shaft vibrations gen- erally pose no problems since in most containerships the shaft is fairly long and flexible, causing a resonance at low rpm and low power. The lateral and longitudinal shaft vibrations may be difficult to avoid. It is here that a decision must be made regarding the number of propeller blades so as to keep resonance away from the op- erating rpm. It is difficult to provide a thrust bearing and supporting foun- dation stiffness so as to place longi- tudinal shaft resonance above the operating rpm, particularly with pro- pellers with a large number of blades.
It is often necessary to accept this resonance within the operating range.
In that case, it must be placed at the lowest possible rpm.
The high powers of modern con- tainerships make it necessary to in- vestigate vibration characteristics that a few years ago were scarcely considered. Not that these phe- nomena were not there but they were of no consequence. The constant in- crease in power will make it neces- sary to go into a more and more de- tailed vibration analysis.
Conclusions
We have briefly mentioned some of the problems that arise in the de- sign of a containership and have shown some of the characteristics of the latest generation of container- ships. The future expansion of con- tainership terminals will most likely result in the design and construction of still larger ships and will require more problems to be solved.
February 15, 1971 13