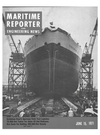
Page 8: of Maritime Reporter Magazine (June 15, 1971)
Read this page in Pdf, Flash or Html5 edition of June 15, 1971 Maritime Reporter Magazine
Fitting Stiffeners—After all the plates are welded together, the flat panel is transferred mechanically to the stiffener positioning welding station. There premeasured stiffeners are automatically aligned and hydraulically pressed to the assembly and welded auto- matically by a twin fillet-welding machine.
Prefabricated Vvebs are manually titted and weided to tne panel atter the application of stiffeners in the new panel shop at Bethlehem Steel Corporation's Sparrows Point shipyard. With the panel, stiffeners and webs, the units may weigh up to 200 tons and measure up to 60 feet by 60 feet by 25 feet high.
Sansinena II— (Continued from page 8) measured stiffeners are automati- cally aligned and hydraulically pressed to the assembly and weld- ed automatically by a twin fillet- welding machine. Manual gravity- type welding can augment the reg- ular process in times of peak loads.
Side conveyors move the panel one stiffener space, and the next stiffener is aligned, set and weld- ed. The side conveyors are control- led by an automatic indexing sys- tem to move the panel the prede- termined distance.
At the next station, prefabricated webs are brought onto the assem- bly line and are manually fitted and welded to the panel. The partially completed subassembly is conveyed through sequential welding, inspec- tion and shipping stations in the north-south leg of the shop.
When the units are completed, they are transferred either to stor- age or to the nearby blast and paint building by means of a spe- cial transfer carrier.
The replacement of the existing plate blasting and coating machine and the installation of a new shape- blasting machine was the first step in the modernization program. This equipment includes the Gyromat coating system in which the incom- ing steel is prewarmed, the paint is circulated and maintained at a constant viscosity, and the coating is applied with controlled thickness and cured in a drying oven at the end of the cycle. In addition, the conveyors are of a special design to prevent marring the finished coating system.
The 231 foot long blast and paint building has facilities for abrasive cleaning and painting of the com- pleted structural units under cover in a controlled environment. The building has two duplicate produc- tion lines, each with three major work stations.
At the first station, the unit is cleaned using four abrasive blast- ing machines that are continuously fed from a centralized storage sys- tem located on the roof. Four shot- recovery pits are located in the floor and are piped to the vacuum system. The facility is designed for using boiler slag grit for the abra- sive material but can be converted for use of steel grit.
Air is supplied at the west wall and is exhausted on the opposite side where three dry bag-type dust collectors are located.
At the second work station, four- man and one-man conventional spray-painting units are used. Fil- tered air for the paint bays is sup- plied at the west wall and is ex- hausted through wet filters on the east wall. Temperature in the bays will be kept at about 65 degrees.
At the last station, the paint is dried and cured at about 95 de- grees.
Additional modernization of the yard is now under engineering study. 10 Maritime Reporter/Engineering News
Inspection—After blasting the assembly is inspected. A newly painted assembly in the painting station is visible through the open 64 foot wide sliding doors. From here the assembly is moved to the paint curing station where the paint is cured at about 95°F.
Ship Subassemblies are transported by a special transfer carrier. Shown here is a unit being taken from the new panel shop, where it was fabricated, to the new blast and paint facility. The panel shop also was dedicated during the ceremonies.