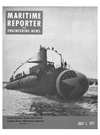
Page 4: of Maritime Reporter Magazine (July 1971)
Read this page in Pdf, Flash or Html5 edition of July 1971 Maritime Reporter Magazine
Gulf Section Spring Meeting (Continued from page 8) few ships should be helpful for all merchant vessels in the future.
The paper presented guidelines that are simple and readily applicable to two-shaft gas- turbine installations. Ratings, fuel consump- tion, fuel service system, heating steam, ship's service electric power, starting and cranking, weights and dimensions and recent develop- ments are all discussed in the paper. 2. "New Concepts in Machinery Protection
Aboard Ships" by H.W. Kinne, Reliance Elec- tric Company, Westerville, Ohio. The follow- ing is a condensation of this paper.
This paper discusses the instrumentation techniques available to protect rotating ma- chinery against: a. Unexpected downtime, b. High maintenance costs, c. Shortened operating life, and d. Catastrophic failure.
The techniques that are generally used are lumped into the general category of "machin- ery protection."
In general, machinery protection includes the parameters of temperature, vibration and speed. Temperature and speed have been widely used in the marine industry for some time. Temperature for such things as bear- ings, motor windings and pump cases—speed for such things as drives, turbine overspeed and turbine start-up. Vibration is the new item and is the main thrust of this paper.
Some things about vibration are not all bad.
It is common to all rotating equipment—a given malady looks the same on a kitchen fan as it does on a high-speed turbine. This makes it an exact science, founded on physical law.
In relation to revolutions-per-minute, each spe- cific problem, i.e., imbalance, misalignment, mechanical looseness, non-concentric gears, etc., always have a specific, predictable am- plitude frequency relationship. Therefore, if we are monitoring a piece of machinery and an alarm tells us that the vibration of the in- board bearing has exceeded a preset limit, we can find out why. This is done by tuning a filter to the offending frequency, much as one tunes his radio to a specific station. Given the available information as to amplitude, di- rection and frequency we can pinpoint the cause. This would allow the engineer in charge to shutdown at a convenient time and do only the maintenance necessary. A further advantage is that he can predict the amount of downtime needed since he will have pre- determined the time needed to solve a specific problem, as opposed to hit and miss mainte- nance techniques.
How do we monitor vibration? We do it generally by using a vibration transducer on the machine to convert either a displacement, velocity or acceleration signal into voltage which in turn read out on a meter in terms of displacement, acceleration or velocity. Two limits are generally used and an alarm is sounded when vibration exceeds a preset lim- it. Further, a second alarm is sounded and/or the machine is shutdown when the vibration becomes so excessive as to make us fear a catastrophic failure.
Usually there is little time for long discus- sions about whether or not a machine should be allowed to continue its operation. In the case of the shipping industry, large sums of money can be lost because of delays due to the outage of a key piece of equipment, either at sea or in dock. If we look at the case of in- dustrial users of vibration monitoring, par- ticularly in the process industries, an unex- pected shutdown causes emergency dumping of costly intermediates of feed stock which results in a total loss. This condition has led to buttons with the legend "Emergency Stop" and with a warning alongside reading
LNG ship designed by four University of Michigan stu- dents participating in the Armco program. The ship has a cargo capacity of two million cubic feet, a speed of 20 knots, a length of 850 feet, a beam of 1 1 0 feet, and a displacement of 56,100 tons.
Unique salvage system shown by students at Gulf Section spring meeting uses 800,000 plastic balls pumped into the holds and six nets attached to a sunken 600-foot ship to provide negative buoyancy to raise the ship for towing. "Think!" Pushing this button costs $27,000.
A key question before shutting a machine down, obviously, is what is the problem? If it is an unbalanced condition in a turbine, perhaps you can slow the turbine down to partial speed and still maintain operation until it is convenient to bring it off the line. On the other hand, if it's high vibration that is caused by a gear box with the gear teeth already sheared off, perhaps your ability to decide is limited to "let's shut it down."
The objective is to strive for a minimum "regret factor." This is different from mini- mum cost because the decision maker does not control the incurred cost. The solution is to be as certain as possible that no addi- tional cost is incurred through that decision making. 3. "LASH Containerization and the Cradle/
Crown Traction Concept" by William A. Barr,
Milwaukee Gear Company, Milwaukee, Wis.
The following is a condensation of this paper.
Although we are usually not conscious of it, history is often taking place before our eyes. Here is a recent, but rather vital, entry in the master log of good ship containerization.
It all started a generation back on the campus of one of our marine engineering uni- versities. A professor advanced the propo- sition that it would pay more to invest in methods of fast port turnaround rather than invest in horsepower to increase ships' cruising speeds.
Today we are seeing such thinking mani- fested in several ways, but each with the purpose of moving the cargo on and off ships faster, and each under the general term—con- tainerization.
One outstanding example is the LASH (Lighter Aboard Ship) concept of the New
Orleans naval architecture firm of Friede and
Goldman.
The unique elements of the LASH concept are the containership and the huge length- traversing gantry crane. This association, it turns out, is much easier to describe than to bring about.
The large crane manufacturers of our coun- try and their industry follow standards and practices which are necessarily and generically different than those of the shipbuilders. It is a challenge for the crane manufacturer to sea oil drilling was designed to be towed to a drilling site in a horizontal position and then flipped to an up- right position. The project was part of the third student marine-design program sponsored by Armco Steel Corp. develop such a radical new gantry crane. But the joining of the two dissimilar elements in- to a common system is an ambitious, if not an audacious undertaking.
The LASH design calls for a deadweight crane lift of 450 tons and for a leg span of 70 feet. The crane rails on each side extend for 600 feet. Traction for this movement requires the engagement of four 150-hp motor-driven pinions (two port and two starboard) with straight racks.
Specifications originally called for 8-inch wide tracks with teeth mounted vertically, 1 diametral pitch, and 17-tooth pinions capa- ble of swivelling to accommodate the inevi- table alignment variations resulting from many ship and crane tolerance accumulations and deflections.
After receiving bids from six gear manufac- turers, one proposal stood out as being unique.
Whereas five manufacturers proposed racks with machine-cut teeth with an 8-inch face, one company offered flame-cut racks with a 7-inch face.
To the credit of the engineers at the ship- yard, an opportunity was afforded the rack and pinion manufacturer to justify its bold proposal; bold, not only because the teeth were not machined, but because the rack is made up of two longitudinal tiers cemented together.
To their credit, the attitude of the ship- builder was not so much, How are the racks made?—but rather, How will they perform?
With this objectivity, it was possible for the gear manufacturer to conceive and develop for the first time what is now known as the
Cradle/Crown Traction Concept.
The Acadia Forest is the first LASH ship and was Japanese built. She and her sistership have machine-cut racks. It is a commentary on the low Japanese manufacturing costs that such a luxury could be afforded. However,
American shipyards are faced with the chal- lenge for something better, yet cheaper. In- genuity is our only weapon against low-cost foreign labor and material.
I submit that the Cradle/Crown concept, the rack/rail alignment concept, and the pre- cision flame-cut racks with overlapping two- tiered sections, is a fitting example of this required ingenuity and economy. 10 Maritime Reporter/Engineering News