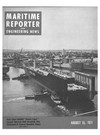
Page 7: of Maritime Reporter Magazine (August 15, 1971)
Read this page in Pdf, Flash or Html5 edition of August 15, 1971 Maritime Reporter Magazine
Part of the program tor invited guests was a presentation of photography depicting the construction of the Doctor Lykes from keel laying to christening ceremonies.
MAJOR VENDORS
Commissary Equipment
Davits & Winches
Side Loading Stores Crane
Barge Transport Rails
Butterfly Valves
Transformers
Valves
Lighting Fixtures
Radio Antenna System
Propeller
Lashing & Securing Cleats
Sideports and Hydraulically Operated Watertight Doors
Insulation
Pilgrim Propeller Nut
Electric Heaters
Casting-Rudder Stock & Main Propulsion Shafting
Ratchets
CuNi Plate
Steel Pipe
Flanges
Valves & Trap Manifolds
Boilers
Anchors & Chains
Ladders
Castings
Steel Valves
Steel Plate
Steel Plate
Steel Plate
Aluminum Gratings
Metal Joiner Doors
Furniture & Joiner Material
Smoke Detector
Rudder Stock Seal
Blickman, Inc.
Marine Safety Equipment Co.
Lake Shore, Inc.
Pierce Aluminum Company
Keystone Valve Company
Acme Electric Corporation
Walworth Company
Simes Company
ITT/MacKay Marine
Ferguson Propeller Company
A.C. Hoyle Company
Walz & Krenzer Inc.
Eastern Cold Storage Company
Marine Products & Engineering Company
Barber-ioleman Company
National Forge
American Engineered Products Co.
Anaconda Company
LaBarge Pipe & Steel Company
Standard Pipe & Supply Company
Yarway Corporation
Babcock & Wilcox
Baldt Anchor, Chain & Forge Division
Alexander Industries, Inc.
Strong Steel Foundry
Ideal Supply Company
Alan Wood Steel Company
Bethlehem Steel Corporation
Phoenix Steel Corporation
Alcoa Aluminum Co. of America
Windows & Clear-view Screens
Butterfly Valves
Emergency Diesel Generator
Ships Service Air Compressor
Bow Thruster
Valves—Steam
Steering Gear
Gyro Compass Steering Control System
Forced Draft Blowers
Air Conditioning—
Refrigeration Plants
Heeling Pump
Distilling Plant
Centrifugal Pumps
Rubber Fendering System
Main Turbines/Gears; Ship Service
Turbine Generator Sets
Main Condenser & Air Ejector
Power Panels
Group Control Center Controllers
Central Engine Room Control Console
Main Thrust Bearing
Line Shaft Bearings; Oil Lubricated
Stern Tube Bearings and Seals
Steel Castings
Barge Handling System
Gears
Jamestown Metal Div., AVM Corporation
Norris Industries
Lucian Q. Moffitt, Inc.
Singer-General Precision Inc.,
Kearfott Marine Products
Centerline, Inc.
Stewart & Stevenson Services Inc.
Ingersoll Rand Company
Bird Johnson Company
Crane Company
Jered Industries Inc.
Sperry Marine Systems Division
Green Fuel Economizer Co., Inc.
York Division, Borg-Warner Corporation
Warren Pumps
AMF Cuno Division
Aurora Pump
Johnson Rubber Company
General Electric Company
Graham Manufacturing Co.
Whitmor Co., Inc.
Cutler Hammer
Bailey Meter Company
Waukesha Bearing Corporation
Birdsboro Corporation
Rucker Control Systems
Western Gear Corporation cutting of steel plate, and 3. de- velopment of the best layout for cutting the maximum number of small pieces from each steel plate.
According to General Dynamics staffer Lennart Thorell, Lykes pro- gram manager at the Quincy ship- yard, the Autokon system has been "a real time saver" and has im- proved the fit of the hull plates. "When a ship is built in pieces, off location," he explained, "you have to be very careful with re- spect to dimensional control and how you put them together. With
Autokon you get very accurate cuts and this minimizes recutting and patching."
Other modern manufacturing processes at the Quincy yard used in constructing the SEABEEs in- clude an automatic sand-blasting unit to clean the steel modules, an all-weather priming-painting unit, and -^automated vertical welding that seals steel plates extending from the keel to the top deck.
Another example of innovative methods used in construction was the erection of the elevator plat- form. This weighed 540 tons, al- most twice the capacity of the ship- yard cranes. To raise the elevator in its installed position, the Quincy shipbuilders devised a scheme to use the ship's own power. This re- quired that major machinery be aboard the ship far earlier in the erection cycle than normal and so placed unusual demands on plan- ning and production.
Mr. Bergeson, general manager of the shipyard, said : "These extra- ordinary ships posed unique design, construction and quality control challenges. The Doctor Lykes is the first ship General Dynamics has built modularly from the ground up. To meet the tight time and cost schedule, 177 steel sections, some weighing over 100 tons each, were prefabricated offsite and moved by cranes to the ship's framework.
This technique compressed the time the ship had to remain in its building position and was a major factor in our ability to meet the delivery schedule."
The SEABEE Story
Mr. Nemec began developing the
SEABEE concept in 1964 follow- ing a trip to Russia where he ob- served Soviet maritime progress.
He was drlmayed, he said, by the advances he saw, and annoyed by the lack of such progressive think- ing in the United States.
His company, considered one of the world's most advanced ship op- erators, had just contracted for some of the first advanced auto- mated ships to be built in an
American yard. Motivated by his
Russian trip, Mr. Nemec then de- termined to force a major break- through in the state of the mari- time art. "We wanted a ship that would do what no other merchant ship had done before," he said. "We wanted a ship so flexible she could serve undeveloped coastlines and waterways as well as established ports, so economical she could out- perform other ships, so versatile she could carry all manner of car- goes in all transport modes singu- larly or in combinations."
Lykes considered many alterna- tives in seeking to find the kind of ship best suited to its needs. (Continued on .page 10)
The 45-ton Ferguson propeller being lowered sideways between the building-basin wall and the ship's cantilever stern, since normal access was obstructed by work on the 2,000-ton capacity elevator platform. The propeller has a diameter of 23 feet.
August 15, 1971 9