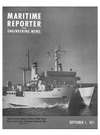
Page 19: of Maritime Reporter Magazine (September 1971)
Read this page in Pdf, Flash or Html5 edition of September 1971 Maritime Reporter Magazine
Westinghouse, Tenneco Plan To Build
Floating Offshore Nuclear Plants
Artist's concept of the proposed joint Westinghouse-Tenneco facility for the manufacture of floating platform-mounted nuclear power plants for offshore sites. Production flow of the platform-mounted plants is from left to right.
Westinghouse Electric Corpora- tion and Tenneco Inc. have an- nounced plans for jointly building platform-mounted nuclear power plants for offshore installation.
N.W. Freeman, chairman and president of Tenneco, and West- inghouse chairman D.C. Burnham, said the companies intend to build floating nuclear power plants on a production line basis in a $200-mil- lion facility that will bring together the talents of both corporations.
Westinghouse is a pioneer in the development of commercial nu- clear power. Tenneco, a diversi- fied multi-industry company, has been heavily involved in the trans- portation and production of ener- gy for many years through its natural gas pipeline and integrated oil operations. Additionally, a Ten- neco subsidiary, Newport News
Shipbuilding and Dry Dock Com- pany, is the nation's largest ship- builder.
Tenneco and Westinghouse have entered into an initial agreement which calls for the completion of technical and economic studies by year-end 1971. At that time, a pro- posal for the development, design, manufacture and sale of the float- ing power stations will be submit- ted for approval by the boards of directors of both companies.
Provided that construction of the unique manufacturing facility could begin in mid-1972 at a site yet to be determined, it is antici- pated that the first completed plat- form atomic power plant would be ready for delivery in 1979. The fa- cility would have the capacity to build four 1,200,000-kilowatt nu- clear plants a year once full pro- duction is achieved and could em- ploy more than 8,000 people at that time.
In heavily populated seaboard areas, the platform-mounted nu- clear plant provides a way to meet man's increasing power require- ments with a minimum effect on his environment, Mr. Burnham ex- plained. For those areas, the proj- ect would: (1) meet the needs of utilities in finding sites for future nuclear power plants economically close to load centers; (2) reduce the threat of future power short- ages by shortening construction time by one to two years; (3) re- duce lead time for regulatory pro- cedures by standardizing plant design; (4) reduce concentrated thermal effects of plant operation because of the vastness of the sea, and (5) reduce utility land acqui- sition costs. Some utilities now buy future plant sites as much as 10 years in advance of construc- tion schedules.
The construction facility would be equipped to install standardized components weighing as much as 600 tons on a repetitive, assembly line basis as the platform is floated from one station to another through the facility, Mr. Freeman explained. A test basin would be located at the end of the assembly area, with all non-nuclear, func- tional tests to be conducted there to demonstrate operability of the plant. Only then w®uld the plat- form reactor be towed to a utility customer's site, installed and fueled within a breakwater.
The design calls for the nuclear steam supply system, turbine, gen- erator and associated equipment to be installed on a square platform measuring 400 feet on a side. The floating platform would have a steel honeycomb construction to assure watertight security and would be designed to withstand salt water exposure for the life of the plant. The entire plant would have a displacement of 150.000 tons—about that of a large, oceangoing tanker — and would draw 30 feet of water.
When permanently installed, the platform reactor would float and be anchored in a stable, man-made lagoon isolated on four sides from agitation of the ocean surface. The breakwater's outer profile would be sufficiently gradual that an off- course ship would run aground be- fore it could hit the protective por- tion of the breakwater.
Power from the plant's genera- tor would be transmitted ashore by means of an underwater line.
L. F. GAUBERT & CO.
INCORPORATED
MARINE, ELECTRICAL & INDUSTRIAL SUPPLIES •Electrical
Cable •Control Cabl phone Cable 'Iding Cable ortable Cords
Telephone: 822-7272 700 S. Broad Street • P.O. Box 50500
New Orleans, Louisiana 70150
The s/ugger
A POWERHOUSE WINCH
THE FACTS ABOUT
JAPANESE
SHIP MACHINERY
Ship machinery from Japan powers and equips vessels of nearly every major flag you can name. In fact over 50% of all ship machinery Japan produces goes abroad.
This is one of the reasons why the more than 60 first- rate companies belonging to JSMEA (the Japan Ship Ma- chinery Export Association) are proud of their products.
They pride themselves, too, on their product quality, per- formance and reliability, and thorough servicing.
Why not find out what Japan's ship machinery industry has to offer? Just let us know what kind of equipment you are interested in, and we will put you in touch with the manufacturers who can help you, or their U.S. dis- tributors. No charge or obligation, of course.
Phone, write, or visit us anytime.
Ask for our brochure.
Ship Machinery Division
JAPAN TRADE CENTER 437 FIFTH AVENUE, NEW YORK, N.Y. 10016 (212) 683-1730
The RF 200 SS is a 229,000 lb. line pull, 2 drum side-by side type powerhouse with the built-in Red Fox prere- quisites: simplicity in design of components and superior craftsmanship:
The 200 SS is one of many
Red Fox Winches, or we can custom build for any specific line pull requirement.
Tfe
MACHINE AND SUPPLY CO.
P. O. Drawer 640 — New Iberia, Louisiana U.S.A. 70560
Write, wire, or call for literature and more information.
September 1, 1971 21