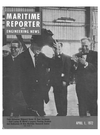
Page 20: of Maritime Reporter Magazine (April 1972)
Read this page in Pdf, Flash or Html5 edition of April 1972 Maritime Reporter Magazine
Stal-Laval Reports Experience Covering Ten Years Of
Marine Turbine Gearing
Review Of 2.5 Million Service Hours With AP-Type Turbines And
Gearing Indicate Trends For Very Large Ships With High Horsepowers.
Ingvar Jung and Per-Erik Larsson
In September 1963, a paper en- titled "Propulsion Gears for Steam
Turbines" was read before the New
York Metropolitan Section of The
Society of Naval Architects and
Marine Engineers. In this presen- tation, the combination of planetary gearing for the first reduction with parallel gearing for the final reduc- tion was introduced. In a 1966
SNAME paper, the progress of the single-plane propulsion unit employ- ing epicyclic primary gears was re- ported and alternative gear solutions for high powers and low propeller speeds were discussed.
During the past ten-year period large and rapid changes have taken place in ship sizes, propulsion power and propeller speeds, all of which have presented the gear manufactur- ers with new and interesting design problems.
Now it is almost ten years since the first designs of single-plane units employing epicyclic primary gears (designated the AP-type) were ready in principle and it appears timely to review the experience from 106 ships which were at sea at the end of 1971, representing some 2.5 million service hours and 3.1. million shaft *Mr. Jung, professor and doctor of technology, and Mr. Larsson, manager of gearing design, Stal-Laval Turbin
AB, presented the paper condensed here before a recent meeting of the New
York Metropolitan Section of The Soci- ety of Naval Architects and Marine
Engineers. horsepower. This service experience indicates the problems and changes required for future gearing and, in particular, for Very Large Cargo
Carriers (VLCC).
In addition, there are AP units of about 3 million shp to be installed in ships on order where the feedback of today's experience will be of fur- ther benefit to quality and availability.
Bearing Pressures
Bearing pressures prevent the use of the planetary-type gear for large powers and high planet-carrier speeds.
In such cases, an epicyclic gear with a stationary carrier, the star gear, has been employed. Typical applications are in triple reduction and in double reduction for high powers.
For larger powers the speed differ- ence between the h-p turbine and the 1-p turbine becomes larger and makes the use of an extra gear reduction on the h-p side economically and practically attractive.
The first units with triple-reduc- tion gears on the h-p side were com- missioned in the middle of 1967. At that time, mounting of the primary gear on the forward side even of a double-reduction h-p side became standard in an attempt to reduce the vibration sensitivity experienced with the previous arrangements.
With demand for low propeller speeds for tankers, triple reduction was the natural solution. Optimizing calculations showed that even with
VLCCs of 200,000 dwt, propeller speed should be kept below 75 rpm, and for tonnages over 300,000 dwt, the speeds used today of 80-85 rpm are still uneconomically high, Fig- ure 1.
Alignment
The original alignment instructions supplied with the gears stated the displacement of the components deliv- ered relative to an infinitely stiff foundation at a certain temperature.
This was in line with the experience and practice employed at the time of introduction of the AP type. The offset during cold alignment was mainly compensation for thermal growth.
The knowledge gained from align- ment measurements on a large num- ber of ships confirms the presence of deformations of origin other than temperature differentials, and which are of the same or greater magnitude than the thermal movements.
Alignment measurements have been carried out in about 40 ships in op- eration in order to establish the changes that take place due to load- ing, warming up, power and seaway.
Extensive instrumentation has been used to monitor the conditions in a ship during a voyage from Europe to the Persian Gulf and partly back.
Of major interest was the effect of maneuvering, of hot cargo, and of passages where rapid changes in water temperature are experienced.
Double - bottom deflections giving movements in the turbine center of 0.025 inches and movements between cold and hot conditions of 0.065 inch- es were measured.
It would be impractical to analyze all the results from these activities and only the following general con- clusions are given; 1. Ships behave as individuals, even if they are made from the same drawings. 2. The movements are repeatable. 3. Cold alignment and cold align- ment checks should be performed within narrow limits of draft and with defined temperatures in lube-oil tanks and other tanks in the engine region. 4. Checking or running alignment as well as checking of main shafting during sea trials is recommended. 5. The results have not revealed any movements that should prevent acceptable alignment of present en- gines from being obtained. The re- sults do indicate that the next genera- tion of tankers, 500,000 to 1.000,000 dwt, needs to be designed with atten- tion to stiffness in the engine region and that the engines should be de- signed to accept larger misalignments than hitherto. No doubt these prob- lems will be solved if hull and engine designers cooperate in the initial stages.
Future AP Designs
The experience reported in this paper has developed the gears and brought detail improvements in de- sign and manufacturing. Lower stress levels and close attention to founda- tion design and to alignment will further increase the safety margins.
Future gears for installations.of the kind described in this paper will fol- low the same concepts utilizing triple- reduction gears of star/planet/paral- lel type for low-speed applications.
For larger powers and generally larg- er ships a more flexible design is introduced. The first h-p gear will (Continued on page 32) 22 Maritime Reporter/Engineering News
Fuel consumption tons/h 651
Pay-off» 3.7 years with correction for increased cargo capacity nMook) e'o 7*5 7b tfe 6>0 Efe 5bPropeUer speed r.p.m. =>u | | • , Capital investment 2D 2.) 2.2 23 2A mill. $
Figure 1—Optimum propeller speed for a 200,000-dwt tanker.
Pay-off = 3.7 years