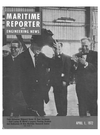
Page 37: of Maritime Reporter Magazine (April 1972)
Read this page in Pdf, Flash or Html5 edition of April 1972 Maritime Reporter Magazine
S.O.S.-Save On Slings *K. Roger Moore
Slings are perhaps the most com- mon yet least understood pieces of industrial equipment in use to- day
Each year an estimated several millions of dollars are needlessly spent to replace slings damaged by improper selection, faulty rig- ging or careless handling. The cost figures, though, don't begin to include the damage done to goods and the personal injury caused 'by unsafe slings.
After these costs begin to mount, operators quickly learn that the key to economy and safety 'lies in care- ful selection and maintenance of slings. By observing a few simple rules, they can extend the produc- tive lifetime of any sling system and protect themselves from costly damages.
Sling Selection Important
With the wide range of sling materials and styles available to- day, the right sling can be matched with each lift job for maximum efficiency, economy and safety.
Fiber or synthetic rope slings are used for comparatively light loads or when a high degree of sling flexibility is required. They are frequently soft -enough to pre- vent damage to the surface of fin- ished materials but are easily dam- aged themselves by direct sunlight, rain and humidity. Once exposed to such weather conditions, it is often difficult to judge the amount of strength left in a fiber rope sling.
Chain slings have a high resist- ance to abrasion and are frequently used on high-temperature lifts in steel mills and foundries. Since just -one weak link in a chain sling can cause failure, they require con- stant inspection and maintenance.
Wire rope slings combine the advantages of fiber rope and chain and can be used for any lift re- quiring safety, flexibility and high strength. Compared to fiber rope slings, wire rope slings are more predictable, more resistant to abra- sion and are stronger, size for size.
Wire rope may develop kinks or broken wires when improperly han- dled, but these flaws are easily no- ticed. Chain slings may have struc- tural flaws—detectable only by so- phisticated metallurgical examina- tion—which affect their strength capacity. *Mr. Moore is a graduate of the Uni- versity of Missouri, and is a registered professional engineer in Missouri. He is an associate member of the American
Society of Mechanical Engineers and a member of both the Missouri Society and National Society of Professional
Engineers. He is an application engineer for Union Wire Rope products, Armco
Steel Corporation, Kansas City, Mo.
Operation Affects Service
Proper sling design and opera- tion are necessary for maximum service and safety in any lift job.
Operators should be aware of con- ditions that affect the performance of a sling system : shape and weight of load; potentially corrosive con- ditions, and age and condition of slings.
Beware—Sharp Edges
Whenever possible, slings should be rigged on a lift to prevent con- tact with sharp edges. Sharp edges can cause permanent damage from kinking and, in some cases, can actually cut a sling.
Saddles can 'be used to prevent contact with sharp edges. A sling saddle wraps the sling around a more gently rounded surface of the load, protecting both sling and load.
Slow & Easy
Loads should be lifted slowly and carefully to avoid temporary overstress of the sling. When slings with more than one leg are used, the load should be lifted in a 'level position. When the lift points are in the same horizontal plane, and the load is uniform, sling legs should measure equal lengths. The center of gravity of the load should be directly under the sling hook to equalize the loads on each leg of the sling.
If the lift points of the load must be below the center of gravity of the load, it is important to rig the lift so that the lift points are a sufficient distance away from the center of gravity to insure stabil- ity, so that the load doesn't tip.
Don't Use A Damaged Sling
Never use a corroded sling to lift any 'load. Corrosion restricts the free movement of wire rope strands and wires, and reduces the sling's ability to withstand shock loads, making it unsafe to use. Cor- rosion is prevented by adequate lubrication and storage of slings in dry, well-ventilated areas.
The hundreds of small wires in a wire rope sling may be damaged by abrasion against other objects.
Abrasion can occur when a load is set on the floor without using elevator blocks. When one end of the sling is unhooked and pulled under the load, severe abrasion re- sults.
Lifting a load when the sling is not securely attached to the load may also cause damage. The sling slides along the load until it catch- es on some protruding object or develops enough friction to stop.
Meanwhile, the cutting and sliding motion severely abrades or cuts the sling.
Crushing is also a severe form of damage. It occurs when the sling is left laying unused on the floor where it can be run over by fork- lifts and other heavy equipment.
Crushing may also occur when the sling contacts unprotected sharp corners or when a heavy load is set directly on it.
A damaged sling should be dis- carded immediately. It is unsafe for even the lightest loads.
Rigging Method Affects Operation
An efficient sling, like a well- fitted suit, should be individualized.
A variety of sling end-fittings and arrangements can be combined to handle any particular load. When lifting unusual materials, special slings can be designed.
Sling design is based on the op- erating conditions which affect a particular lift: the weight of the load, the angle made by the sling and the load, the available over- head space and the necessity of turning over the load.
Depending on the weight of a load, a system ranging from one small sling to several larger ones may be required. When the weight is known, lift points are determined with respect to the load's center of gravity. The weight distributed to each leg of the sling can be determined, the sling angles calcu- lated and a design specified.
Larger slings are needed as the sling angle with the vertical be- comes excessive. Excessive sling angle is often a product of inade- quate overhead space. When lack of overhead space is a problem, a spreader bar should be used to re- duce the siing angle.
To prevent abrasion, never turn a load in a basket hitch. Instead, use a double choker 'hitch where the center of the rope passes over the hook for equalization of load weight. The load is then turned with a tight, secure rope.
Improved Handling Saves Slings
Most sling failure results from carelessness and abuse. It some- times seems as though more slings are discarded because of abuse than normal wear. Several precau- tionary measures can be taken to improve sling service, reduce costs and ensure safe operation. — Do not overload slings. When in doubt about overloading, use a sling with a higher lifting capa- city to avoid accidents. A sling which has been overstressed may not appear damaged, but may fail on the next lift at a considerably lighter load. It should be discard- ed immediately. — Avoid handling hot materials with slings. — Avoid cutting slings on sharp load corners. Use sling saddles. — Do not crush slings. Whenev- er possible, set the load on blocks.
Pulling a sling from under a load causes abrasion and kinking. — Avoid corrosion. Store slings in a dry, well-ventilated room. Ex- posure to moisture and acid fumes corrodes and weakens slings. — Do not leave slings on the floor. Slings should be hung on wall hooks when not in use. If left laying on the floor, they will be damaged by heavy Objects and equipment. —• Do not start or stop sling mo- tion suddenly. Jerky movements increase the stress and distort the proportioning of weight on the sling. —• Do not ignore sling damage.
Make periodic inspections of all slings.
Inspections Cut Operating Costs
Sling failures increase operating expenses — including equipment damage, disruption of job sched- ules and personal injury—far be- yond the cost of an adequate in- spection program and the occa- sional replacement of a sling.
Because there are several kinds of sling failure, an inspection pro- gram must be regular and thor- ough. In general, a sling should be replaced if there is any question about its safe operation. The cost of a new sling is small indeed com- pared to the cost of damaged goods and equipment or injured person- nel.
Kinked and twisted slings should be discarded. A single broken wire may not be cause for concern, but it is wise to retire any sling that is questionable. Damaged sling eyes indicate the sling is ready for retirement.
Advice about safe use of slings is available from Union Wire Rope distributors throughout the United
States. Armed with a few simple facts about the selection, operation, handling and inspection of slings, operators can reduce sling costs and enjoy more efficient and safe use.
Galveston Wharves
Names L.B. Prino Jr.
L.B. Prino Jr.
L.B. Prino Jr., manager of the
Galveston, Texas, office of Bay-
Houston Towing Company, has been appointed to the board of trustees of the Galveston Wharves.
The term of office is three years.
A veteran of 31 years with Bay-
Houston Towing, Mr. Prino will join other 'board trustees in at- tempting to maintain an undimin- ished flow of commerce through the port while reconciling and ac- commodating water front activities with ecological needs.
Mr. Prino has been a lifelong resident of Galveston and is a mem- ber of the Galveston Propeller
Club.
April 1, 1972 47