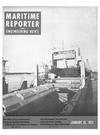
Page 5: of Maritime Reporter Magazine (January 15, 1973)
Read this page in Pdf, Flash or Html5 edition of January 15, 1973 Maritime Reporter Magazine
pany is steadily increasing its capa- bilities to ibuild a more efficient and profitable maritime industry.
Cecil M. Keeney
The New Orleans shipbuilding facilities of the company and its executive offices are located on that city's Industrial Canal, in the heart of the marine industry on the Gulf
Coast. The plant occupies 38 acres of land fronting on the heavily in- dustrialized waterway, with easy access to the Gulf of Mexico and world ports through the Mississip- pijGulf outlet and Intracoastal Wa- terway.
The plant is completely equipped for the new construction, conver- sion, and repair of marine floating equipment and for the fabrication of structures for the petroleum in- dustry.
Equitable Equipment Company's facilities contain 170,000 square feet of covered warehouse space, and approximately 241,000 square feet of open, paved yard area- Fab- rication of all types of steel floating equipment up to 2,500 tons can be handled, and there are two marine railways docks, one of the Crandall launching and rehaul type of 1,000- ton capacity, and one made up of a series of 12 steel cradles mounted on inclined tracks, permitting side launching of vessels up to 325 feet by 90 feet by 2,500 tons.
Machinery and equipment in use in the plant includes stationary and mobile cranes with capacities to 50 tons, a stiffleg derrick with a 100-ton capacity, gantry unit, crawler, mobile, bridge and loco- motive cranes, presses, brakes, plate rolls, shears, air compressors, and the usual complement of heavy machinery necessary for efficient production of the company's prod- ducts.
The company will spend approxi- mately $2 million in 1973 to de- velop additional areas of the ship- yard for new construction, repairs, and conversion work.
The design and fabrication of heavy and light equipment for in- dustry and marine interests is done at the New Orleans shipyards.
Products produced by the company include derricks with capacities up to 10,000 pounds, diving bells, pon- toons, decompression chambers, packaged block ice plants, hatch covers, offshore platform quarters, watertight doors, portable dredges, buoys, petrochemical vessels and special process equipment, process pressure tanks, large diameter pipe, and other types of equipment. The company builds to ASME, API,
ABS, and USCG requirements.
Farm tractors, long hollow steel shapes, 20-foot container, sacked cargo behind which Beefeater's gin was transported, and machinery parts are just some of the many cargoes being transported by LASH.
A LASH lighter stowed out 1 00 percent with a cargo of tea. Rapid discharge and load- ing rates are possible by the easy vertical load stow design conditions of the lighter.
The cargo is worked from the top down for effective and safe stevedoring operations.
Ten LASH barges each week are completed, under cover, on this production line at Equitable's New Orleans yard.
Seen in the foreground is one of the heavy lifts which was in excess of 255 long tons. Portable extension posts are shown fitted to the LASH lighter lifting posts which allow for the transport of lifts under deck up to 22 feet in height. $35.3 Million To
Bath To Build Fourth
States Steamship Ro/Ro
A contract valued at $35.3 mil- lion covering the construction of one of the largest roll-on/roll-off ships to be built in the United
States was recently signed in
Washington, D.C.
Bath Iron Works Corp. of Bath,
Maine, will build the 18,000-dwt ship for States Steamship Co. of
San Francisco, Calif., which will use the new vessel—along with three others ordered from Bath last
June—in its U.S. Pacific/Far East service.
According to Robert J. Blackwell,
Assistant Secretary of Commerce for Maritime Affairs, who signed the contract for the Government, the price of the vessel ordered re- flects a $2.5-million reduction in the per-ship price for the first three
States ships. As contrasted to a $16.2-million subsidy payment on each of the initial ships, the current contract provides for a subsidy of $14.3 million. "This decline in subsidy graphi- cally illustrates the productivity gains being made by the Bath ship- yard in terms of lowering its costs.
Because of these gains, the subsidy rate has been lowered from 43 per- cent to 40 percent of the price of this last ship," Mr. Blackwell ex- plained.
The subsidy, he said, is calcu- lated by subtracting the equivalent foreign cost of the ship, which in this case was estimated to be $21 million in a Japanese shipyard, from the domestic price.
Like the first three, which cost $37.8 million each, the latest ves- sel will be 684 feet long, 102 feet in beam, and 32 feet in draft, with a speed of 23 knots.
Mr. Blackwell noted that this contract brings the total value of shipbuilding awards under Presi- dent Nixon's two-year-old mari- time program over the $1.7 billion mark, with 37 new vessels and 13 ship conversions ordered to date.
Representing in excess of 3,000 man-years of work for the Bath,
Maine, shipyard, the four States ships are scheduled for delivery be- tween 1975 and 1977.
These roll-on/roll-off ships load and discharge their cargoes of truck vans through a stern ramp-
Zapata Corp. Plans
To Build Self-Propelled
Shipshape Drilling Unit
Zapata Corp., Houston, Texas, has announced that it plans to construct a self-propelled shipshaped drilling vessel for use by one of the com- pany's offshore drilling subsidiaries,
Zapata North Sea, Inc.
The ship, to be designed for year- round operations, with quarters for 90 men, will be capable of operating in 600 feet of water, drilling to a depth of 20,000 feet, and remaining moored in 60-foot seas. Additional equipment would render it capable of operating in 1,000 feet of water.
The vessel will be 427 feet long, 75 feet wide, and 32 feet deep.
January 15, 1973 7