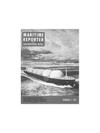
Page 14: of Maritime Reporter Magazine (February 1973)
Read this page in Pdf, Flash or Html5 edition of February 1973 Maritime Reporter Magazine
Lykes SEABEE Barge
Ships Container Cargo
Direct St. Louis-Europe
The Port of St. Louis recently took another step forward in becom- ing a major inland seaport as Lykes
Bros. Steamship Co., Inc. sent one of its SEABEE barges to St. Louis,
Mo., to load containers and breakbulk cargo for North Europe and the
United Kingdom.
The movement, according to the
Chamber of Commerce, marked the first time that containerized cargo was shipped directly to Antwerp and
London via the all-water route from
St. Louis on a single carrier bill of lading.
The containers were stowed with chemical products manufactured by the Monsanto Chemical Company, and they were loaded aboard the highly sophisticated Lykes SEABEE barge at the St. Louis Terminal Com- pany port facility. This also marked the first time that a SEABEE barge had taken on cargo as far up the
Mississippi River System as St. Louis.
SEABEE barges are a vital part of the new Lykes SEABEE System operating between U.S. Gulf termin- als at Galveston, Texas, and New
Orleans, La., and SEABEE terminals in Northern Europe and the United
Kingdom. Each of Lykes's new $33- million intermodal SEABEE trans- ports can load as many as 38 SEA-
BEE barges.
The SEABEE System links the vast Mississippi River waterways sys- tem in the United States with the
Rhine River and its tributaries in
Europe, thus making it possible for barges to be loaded deep in the in- terior of both the United States and
Europe for shipment across the At- lantic aboard a SEABEE transport.
Shippers in increasing numbers are moving their cargoes via Lykes SEA-
BEE because the system offers speed, efficiency and safety to a greater de- gree than has ever heretofore been possible.
Lykes recently opened a full serv- ice office in St. Louis and exporters and importers in the greater St. Louis area interested in the Lykes SEABEE
System may obtain full details from
Tim Parker, manager of the Lykes office.
Shlemmer To Head
Two Divisions For
Western Gear Corp. our compact 400 marine water heater never runs hot and cold.
J. David Shlemmer
The appointment of J. David
Shlemmer as manager of industrial power transmission equipment and related commercial systems for two divisions of Western Gear Cor- poration has .been announced by
Saleem Naber, group vice president.
A mechanical engineer, Mr.
Shlemmer will manage the Indus- trial Products Division, Belmont,
Calif., and the Southwestern Divi- sion, Houston, Texas. Both opera- tions are involved in the manufac- ture and marketing of industrial gear drives.
Mr. Naber said the appointment of Mr. Shlemmer, a Western Gear employee since 1953, is planned to combine the design and develop- ment activities of the two divisions, and to consolidate their marketing capabilities under a single group- ing. He added: "We expect to broaden the penetration of the di- visions in their industrial and ma- rine markets, thus gaining greater strength and a wider base for both operations."
Manufacturing operations will continue to be based at the Belmont and Houston plants, but engineer- ing under Robert Malcolm, and marketing under Ray Pickel will be centralized in Lynwood, Calif. Del
Dishno will continue to direct ac- tivities in Belmont, while Fred La- moureaux will continue to manage the Houston plant.
PATTERSON-KELLEY COMPANY
EAST STROUDSBURG, PENNSYLVANIA 18301
Manufacturer of water heaters • heat exchangers • steam generators • blenders • dryers • corrosion-resistant cements
Its Unique Anticipator® Control System makes sure of that. The Anticipator, acting as a nerve center, continuously senses heat demand based on inlet water flow and temperature. The result is a constant supply of hot water to shipboard fix- tures, with temperature controlled to ±5°.
Packaged for quick installation — only five connections — the Compact 400 saves on labor costs. Routine inspection just means pulling out the tube bundle. And servicing is easy because the gaskets are all inde- pendent.
Compact but powerful, the marine 400 does the work of a conventional unit four times its size, delivering up to 660 gpm. For maintenance access, it requires a maximum of only 36" frontal clearance and no overhead clearance. You can even mount it on a bulkhead or hang it from the overhead.
Nonferrous Materials of construction fea- ture an SB-96 copper-silicon shell. All P-K Com- pact 400s are built to ASME and ABS standards as well as to U.S. Coast Guard regulations. And all reflect our 93 years' experience in engineering and manufacturing reliable heat transfer equipment.
Send for Bulletin 400. 16 Maritime Reporter/Engineering News