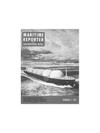
Page 5: of Maritime Reporter Magazine (February 1973)
Read this page in Pdf, Flash or Html5 edition of February 1973 Maritime Reporter Magazine
Figure 3—The 1 25,000-cubic-meter LNG ships have been designed by General
Dynamics for the maximum standardization of the production process and flow. Unique methods have been developed for manufacturing the aluminum
February 1, 1973 7 spheres, and a mechanized process line will produce the major portion of the hull structure. Development of specialized manufacturing facilities and improve- ments which will involve substantial capital investment have commenced. tanks in existence, to design and installation of the regasification components of LNG systems.
The theory of constructing ma- jor components of ships at remote locations is not new, but it has par- ticular application to LNG carriers and especially to the new mammoth capacity ships which utilize free- standing tanks as LNG containers.
As noted by William Thomas and
Alfred Schwendtner in their recent comprehensive study, "LNG Car- riers : The Current State of the
Art" (see MARITIME REPORT-
ER/Engineering News issue of
January 1, 1972), the LNG tanks represent probably the most dis- ruptive process to a shipyard's normal building schedule. Remote construction of these special con- tainers for installation at the ship- yard or at another site offers many advantages.
The plan chosen by Quincy Ship- building Division of General Dy- namics and PDM is based on con- structing complete free - standing tanks at a manufacturing facility having clear access to water trans- portation and then barging the tanks to General Dynamics' ship- yard at Quincy, Mass. The manu- factured tanks will be spheres based on the Moss-Rosenberg tech- nique as designed by GD with as- sistance from Det norske Veritas.
The material used in the spheres, described in Figure 1, will be 5083- 0 aluminum.
Subassembly will be done in an enclosed shop, with final assembly outside as shown in Figure 2.
When ready for shipment to
Quincy, the spheres will be loaded on barges as shown in Figure 2.
These spheres will be unloaded from the barges and placed into the ship's hull with a unique 850- ton-lift overhead crane specially de- signed to handle the spheres. This crane is one of the largest present- ly planned to be available in a U.S. shipyard. The use of this crane will simplify the loading operation and expedites completion of the ship. A view of the total LNG ship configuration with a cutaway of the LNG tanks as installed is shown in Figure 3.
Among the advantages of the
Quincy Shipbuilding Division of
General Dynamics-PDM program for constructing LNG ships using spheres manufactured at a remote site are:
The ship's hull structure is built by shipbuilders and the LNG con- tainers are built by qualified ex- perienced cryogenic tank builders.
Special techniques are required to build very large free - standing tanks. These techniques are avail- able without special training by
PDM, whose normal business is building tanks and other large structures.
A special manufacturing facility can be custom-built to maximize the efficiency of construction of the required spheres. An artist's draw- ing of the proposed manufacturing plant is shown in Figure 2. The plant has separate areas for the forming and trimming of plates, subassembly of sphere sections and final assembly. It should be noted that the production system makes use of parallel assembly bays to eliminate bottleneck operations.
Raw material is delivered to the plant by rail and barge, and the finished product is shipped to Quin- cy by barge as shown in Figure 4.
The spheres are loaded on the barges without the use of lifting equipment.
An important benefit gained from using a remote manufacturing fa- cility for the LNG containers is that a separate quality control pro- gram can be maintained in the ship- yard and in the tank shop. This is an improvement over trying to mix quality control unique to the two types of work. It is also an ad- vantage to be able to create a man- ufacturing environment which is tailored to the product by design- ing equipment that is used for only one basic material. Such a plant affords the quality of control of the working environment that is neces- sary for insuring high-grade alumi- num welding.
A very important consideration which favors a remote LNG con- tainer manufacturing site involves the manpower required to build the tanks. The skills required and the job classifications necessary to build cryogenic tanks are not the same as those required to build ship hulls. The ability to train workmen to manufacture contain- ers which are constructed of ma- terials different from ship steel provides the advantage of having men picked for and judged in ac- cordance with a specialty. It is im- portant, of course, to choose a tank manufacturing site near a good source of efficient labor.
The Quincy Shipbuilding Divi- sion of 'General Dynamics Corpora- tion-PDM plan is designed to im- prove the quality of LNG ship con- struction and to add reliability to the ship delivery schedule. The final product, the LNG ship, will truly represent the best efforts of proven experts in each of the major areas of construction—the ship hull, and the LNG container. 24 PL' S.
Figure 1—The tanks manufactured by Pittsburgh-Des Moines Steel will be spheres based on the Moss-Rosenberg technique. The material used will be 5083-0 aluminum.
Figure 4—The finished LNG spheres will be shipped from the manufacturing plant to
Quincy by barge. At the yard, the spheres will be unloaded and placed into the ship's hull using a unique 850-ton-lift crane especially designed to handle the spheres.
PL'S. 25.000 M3 LNG SPHERE