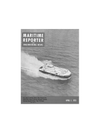
Page 34: of Maritime Reporter Magazine (April 1973)
Read this page in Pdf, Flash or Html5 edition of April 1973 Maritime Reporter Magazine
Ducted Propeller Applications
Current Investigations Into Ducted Propellers Indicate A Worthwhile
Potential Performance Advantage For A Broad Range Of Ships
Leonard Meyerhoff, John G. Hill and Stanley Meyerhoff*
The ducted propeller is now under- stood to have unique advantages. Ap- preciable power reductions are seen in the literature, indicating that an important advance for marine-pro- pulsor design may be developing. Be- cause numerous ducted-propeller con- figurations exist, each with a possibly different hull interaction, there is increasing suspicion that the full po- tential has not been explored.
In recent years ducted propellers have been installed on several large commercial ships, naval destroyers, and even torpedoes—and numerous large commercial installations are now under construction or being planned.
As seen from Table 1, the ducted- propeller applications must surely rank high among the largest overall propulsor sizes in use today. General reasons for these installations include power reductions, smaller propeller size, the opportunity which the duct affords for propulsor flow control, better utilization of wake inflow, im- proved blade loading, and the poten- tial for reducing propeller-excited vi- bration.
The highest commercial ship speed today with a ducted propeller is about 17 knots. The highest speed considered for the ducted propeller in this paper is 33 knots. It is the authors' opinion that use at even high- er speeds will be possible with excel- lent performance. •
Superior performance with good economic benefits is an important mo- tive today for the ducted-propeller commercial-ship application. For ex- ample, published trial data for the 215,000-dwt tanker Golar Nichu with a ducted propeller shows about a 0.35- knot speed increase compared with a sistership having a conventional open propeller. The propeller diameter is 25.6 feet for this ducted system com- pared with the 26.9 feet of the cor- responding open propeller. Published reports indicate reduced vibration and improved maneuverability. A recent investigation shows improved stop- ping ability compared with an open screw on a model 100,000-dwt single- screw tanker. A power saving of 5 to 10 percent is anticipated for the 131,450-dwt tanker Kronoland. *Mr. L. Meyerhoff, research director, and Mr. S. Meyerhoff, engineering man- ager, both with Eastern Research Group of New York, N.Y., and Mr. Hill, marine engineer and naval architect in private consulting practice, presented the paper abstracted here before the Annual Meet- ing of The Society of Naval Architects and Marine Engineers.
Table 1—Survey of Some Ducted-Propeller Installations
Type and Speed Duct Inflow
Name DWT SHP Knots Dia. Ft. Pattern
Destroyer 3,520 60,000 35 9.2 decelerating
USS Witek
Destroyer Escort 3,500 35,000 27 13.0 decelerating
USS Glover
Cargo Ship 8,260 5,200 16.2 15.0 accelerating
Komsomol
Bulk Carrier 25,000 9,600 14 21.3 accelerating
Ralph Misener
Tanker 131,450 25,000 16.7 27.3 accelerating
Kronoland
Tanker 215,000 30,000 16.6 30.8 accelerating
Golar Nichu
Torpedo 1.6 low high 1.75 decelerating
U.S. Mark 48
Reports of large power reductions (higher propulsive coefficients), most- ly measured under laboratory condi- tions, are beginning to dominate the growing ducted-propeller literature.
Naval ducted-propeller applications may have other priorities, such as quietness, lower noise related to vi- bration, and delay of blading cavita- tion ; even here, however, good eco- nomic performance would also be needed.
The present use of the large ducted propeller is noted mainly for high- block-coefficient ships which have high wakes. This places the ducted pro- peller in an operating regime where it has always shown advantages. The high wakes of such ships lead to a reduced efficiency for the open pro- pellers ; to obtain an improvement requires large open-propeller diame- ters and low rpm. Consideration of open-propeller design for "megaton" tankers shows the same tendencies, where diameters approaching 40 feet are predicted with triple screws and low rpms.
For high-speed containerships, con- cern arises regarding draft limits on the open propeller diameter and its ability to absorb increasing power per shaft. By using a duct to modify the inflow, possibilities occur to permit increased power absorption for a giv- en diameter as well as improved blading cavitation delay.
It is worth noting that the use of a duct offers the ancilliary opportun- ity of ship maneuverability control by deflecting the propeller jet. Substan- tial control forces are possible. One alternative to the steering duct is, possibly, the use of a fixed duct with moveable jet deflectors, forming part of the duct contour in the undeflected position. Similarly, a ship pitch- quenching possibility exists for use in rough seas by means of appropri- ately oriented jet deflectors driven cyclically in a special relation to the ship pitching motion.
These diverse considerations may be viewed as interesting developments for a propulsor historically applied to low-speed towing. The resurgence of ducted-propeller technology is gradually furnishing informative test data and an emerging ability to cal- culate flows by new computer methods.
Despite increasing attention, much of the available ducted propeller lit- erature is concerned with open-water test data. However, wake operation is of prime interest and the literature offers little design selection aid and does not indicate whether the known ducted-propeller performance gains are the best obtainable.
Hull - propulsor interaction must surely be influenced differently by inflow patterns ranging between ac- celeration and deceleration. For ex- ample, if the inflow is not accelerated, thrust deduction should be attenu- ated, leading to a hull efficiency in- crease and, presumably, a large pow- er reduction.
It is therefore reasonable to ask whether the ducted-propeller poten- tial is known for modern ships. To- ward this goal the paper introduces
Type-1 and Type-2 ducted propellers, which seem "generic" for wake use.
Type 1 (accelerating inflow). Flow rate and duct inlet diameter are the same as a corresponding open propel- ler to permit use of available open- propeller wake-fraction and thrust- deduction values.
Type 2 (unchanging inflow). Flow rate and duct inlet diameter are ob- tained from nominal wake-fraction values.
Considerable information on wake and thrust-deduction coefficients are available from open-propeller expe- rience. A similar use of this infor- mation would be advantageous for guiding predictions of ducted-pro- peller performance possibilities.
Ducted propellers can be designed to produce a range of inflows between acceleration and deceleration. Con- sider from within this range two me- dian systems. One system is an ac- celerating type with an inflow identical to a corresponding open propeller for the same ship ; the other is the unchanging inflow type which leaves the nominal inflow wake un- altered, as if the ducted propeller was not present.
This paper predicts the perform- ance for a wide range of hull forms and speeds. Single- and multiple- shaft cases are considered. Available towing-tank data furnish the basic hull characteristics for the studies.
Propulsive coefficients ehp/dhp are estimated from relations derived for
Types 1 and 2 ducted systems; com- parative performance tendencies are shown with corresponding open-pro- peller data obtained from model pro- pulsion tests, Table 2.
Results to be seen consistently in- dicate a power-saving potential with the ducted propeller. Flexibility of machinery selection is indicated from the allowable combinations of rotor diameter and rpm. The general supe- riority predicted for Type-2 ducted propellers appears to be a new de- velopment in terms of power-reduc- tion potential.
While duct construction is outside the scope of this paper, some perti- nent facts, can be noted. Ducted pro- pellers in the form of Kort nozzles have been in use for many years— particularly on towboats, where the shaft horsepower is in the order of several thousand and the applica- tion is for increased bollard pulls.
Ducts generally are fabricated of steel plates and shapes.
The first large-power ducted pro- pellers known to the authors are the twin-shaft units installed on the de- stroyer USS Witek, each rated at 30,000 shp. These ducts were made in three sections: the inlet, the rotor, and the exit-nozzle section containing stator vanes. Each section, made from a number of bronze castings welded together to form a ring, was bolted to the adjacent section.
When a similar ducted propeller was authorized for the single^shaft destroyer escort type, USS Glover, the decision was made to construct the nozzle as a welded unit, with some castings, but mostly rolled plates of
Superston 40.
Table 2—Hull Applications Studied
Speed No. of Block
Hull Tons Knots Screws Coeff. EHP
Series 60 26-47,000 23-14 1 0.6-0.8 6-26,000
Cargo 18,000 25.5 1 0.53 21,000
Container 38,520 25.5 1,2 0.56 31-32,000
Container 41,000 33 1,2 0.54 82-84,620
Tanker 136,000 19.25 1, 2 0.78 30,800
Tanker 500,000 16 1,2,3 0.85 47,000
Tanker 750,000 16 1,2,3 0.85 60,000
Tanker 1,000,000 16 1,2,3 0.85 72,000 36 Maritime Reporter/Engineering News