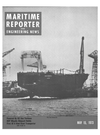
Page 9: of Maritime Reporter Magazine (May 15, 1973)
Read this page in Pdf, Flash or Html5 edition of May 15, 1973 Maritime Reporter Magazine
The 21st Annual Fort Schuyler Forum Discusses
Corrosion Control, Tank Cleaning & Inerting
Taking part in the Forum were: (seated, left to right) Philip A. Donahue, Maritime
Overseas Corp.; Rear Adm. Sheldon H. Kinney, USN (ret.), president, State University of New York, Maritime College, and Dr. John J. Foody, chairman, department of engi- neering, SUNY Maritime College; (standing, left to right) Horry H. Hunt, Marine Sur- veyor; R.L. Doyle, manager, technical sales and planning, International Paint Company, author; Jose Femenia, assistant professor of engineering, SUNY Maritime College, author;
John Antonetz, Texaco, Inc., chairman, papers and technical committee; Peter Quarter- man, marine superintendent, Dasic .International, author; E.B. Budd, chief engineer,
Wilson, Walton International Ltd., author; R.J. Walton III, president, Wilson, Walton
International Inc., author, and Joseph Thelgie, Marine Transport Lines.
Corrosion control, tank cleaning and inerting, basically as relating to tankers, were the subjects covered during the 21st Annual Fort Schuyler
Forum. These technical symposiums are sponsored by The Society of Ma- rine Port Engineers, New York,
N.Y., Inc., and the State University of New York Maritime College. The attendance at this year's forum ex- ceeded those of previous years, which indicated the importance of the sub- jects covered to the marine industry.
Dr. John J. Foody, chairman, De- partment of Engineering, Maritime
College, presided during the morn- ing session, and Philip A. Donahue,
Maritime Overseas Corporation, served in the same capacity for the afternoon session. Rear Adm. Shel- don H. Kinney, USN (ret.), presi- dent of the Maritime College, wel- comed the attendees.
The 1973 Forum Committee con- sisted of Dr. Foody and John An- tonetz, Texaco, Inc., as co-chair- men, and the following members:
Louis V. Minett, American Bureau of Shipping; assistant professor
Jose Femenia, Maritime College;
Capt. H.O. Travis, U.S. Merchant
Marine Academy; Mr. Donahue;
Joseph Thelgie, Marine Transport
Lines; Harry H. Hunt, marine sur- veyor; Edward English, Atlantic
Repair Company, and John C. Fox
Jr., Esso International, Inc.
The following excerpts from the five papers presented indicate the depth and importance of the techni- cal sessions:
Corrosion Protection toy
Robert J. Walton III
Wilson, Walton International Inc.
There are four basic methods to control corrosion attack of all metals.
The naval architect, the builder, the owner and the operator can use these tools as the practicalities and the eco- nomics of the situation demand. These methods are: 1. Corrosion resistant materials. 2. Protective coatings. 3. Treatment of the environment. 4. Cathodic protection.
Each of these methods has certain adaptabilities and advantages, but sig- nificantly none are cure-alls. For the protection of many structures, the most effective and economical solu- tion may be accomplished by using a combination of these methods. As an example, methods (2) and (4) were first used in the early 1930s for the protection of gas and oil distribution piping. At this time, these two meth- ods are being used to protect the underwater hull and the inside sur- faces of condenser and cooler water boxes.
Corrosion of the external hull has been greatly retarded by the applica- tion of exotic coatings. Most of the established owners are using these coatings on all vessels, with the pos- sible exception of smaller vessels where operation can result in periodic coating damage. To back up and pre- vent severe pitting attack at the breaks in exotic coatings, many own- ers are installing impressed-turrent cathodic-protection systems. A rea- sonable estimate of the number of impressed-current systems in use to- day would be three thousand. Nearly all newbuildings are being so fitted.
A properly designed, installed and maintained impressed-current system will permit an owner to extend dry- docking from two years to two and a half years in accordance with
Lloyd's Register 1968 Rules.
Impressed current is generally re- stricted to the external hull, its use not being permitted or its perform- ance practical inside ballast tanks. No classification society would permit us to hang high-voltage anodes in a tank filled with explosive vapors and where chlorine gas would be caused to evolve in great quantities to corrode away the upper structure.
There are presently two basically different systems of impressed cur- rent available; both can do the job and both operate on the same princi- ple, cathodic protection. The basic differences are in the choice of anode and half-cell materials, and the cir- cuitry of the power package. The anode alloys available and most gen- erally used are: lead silver, platinum clad on a base metal, and exotic coat- ings on a base metal. Each has its particular advantages and disadvan- tages.
Virtually all of the world's major shipyards are now familiar with im- pressed - current cathodic - protection systems as they are installing them in increasing numbers. Therefore, you will have no difficulties here once you have selected and purchased the prop- er equipment. "Tuning-in" the sys- tem and adjusting it for use prior to delivery after construction is the job of the supplier. Once your ship is at sea, the crew should only record daily readings of volts and amps. As op- erating problems occur, and they will, the supplier must be capable of furn- ishing men and parts on a world scale.
The frequency of service should be less than once per year.
Using cathodic protection in bal- last tanks, the corrosion rates will be reduced to 30 percent of that experi- enced in unprotected tanks. If the average loss is 0.5 mm per year (washed two sides, immersed and unprotected), this rate will be reduced to 0.15 mm per year by use of catho- dic protection in tanks. Thus, elimi- nating renewals for 20 years.
Marine Paints and Coatings by
Robert L. Doyle
International Paint Company
The selection of the antifouling coating will depend upon the operat- ing schedule of the ship. The strength of the antifoulings is determined by the toxic or active ingredients. In most cases, the main toxic for con- ventional antifouling is cuprous oxide.
Based on the ship's service, it is con- ceivable that two and possibly three antifoulings may be needed on a single hull. But generally, when deal- ing with conventional or soft-type antifoulings, a regular antifouling or low-strength 'type is used on the fiats and supertropical type from the bilge keel to the light loadline.
Assuming the anticorrosive paint, the aluminum-barrier coat, is doing its job, the repair schedule should be as follows after proper surface prep- aration : one touch-up coat of bitumi- nous-aluminum barrier, one full coat (optional) of aluminum barrier, and one full coat of antifouling.
Although the full coat of bitumi- nous-aluminum barrier coat is op- tional, it would be advisable to apply this every other drydocking, and more often if groundings warrant.
There are times when shipowners would like to extend their drydock- ing intervals, but are limited by the life cycle of the antifouling and/or the bottom requires continued atten- tion due to the corrosive destruction of the underwater hull. However, this conventional-type bottom system need not be perpetuated because we can convert this bottom to a sophis- ticated high-performance coating sys- tem with the proper surface prepara- tion and a selective high-perfor- mance coating system.
Converting to a high-performance coating system will provide an anti- corrosive barrier that will virtually stop the corrosion process and with an adequate film thickness will mini- mize the roughness of the hull. An- other benefit is the ability to use anti- foulings with long-term protective properties. The adverse effect of roughness due to corrosion and foul- ing with respect on speed is of the (Continued on page 13)
May 15, 1973 11