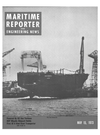
Page 4: of Maritime Reporter Magazine (May 15, 1973)
Read this page in Pdf, Flash or Html5 edition of May 15, 1973 Maritime Reporter Magazine
The Iron Monarch is guided to the fitting-out wharf following its launching. Note the canted stern door opening and gantry for the stern ramp to be used at normal wharves.
Australians Develop World s First Unitized
Ro/Ro System To Transport Steel Products
Australia's only steel producer, largest miner, oil and natural gas producer, builder of the coun- try's biggest ships, and operator of the largest privately owned shipping fleet, The Broken Hill
Proprietary Company Limited of Melbourne, will introduce this year to the Australian industrial scene unitized transportation of steel products, based on the Ro/Ro system.
BHP transports more than 40 percent of its products by sea—a much greater proportion than overseas steelmakers. However, in recent years spiralling costs have tended to erode the advan- tages of long hauls by sea. The wide range of steel sections, sizes and qualities of finished steel products and the handling of small customer lots makes the loading and unloading of steel cargoes carried by ship less efficient than homogenous car- goes. The resulting lower ratio of vessel sea time to port time plus the rapid increase in stevedoring costs has eroded the cost advantage of long-haul transportation by sea.
In the continuing effort to develop the most economical means of transporting steel, BHP un- dertook a searching analysis of the movement of steel from the mill to the customer. The plan which emerged represents the first attempt in the world to implement a unitized Ro/Ro system for a full range of steel products.
The system initially will include two ships, bol- sters (open containers), improved terminal facili- ties, specially designed handling equipment and systematic terminal storage and ship stowage ar- rangements. The cost of implementing the plan is some $31 million including $24 million for the two vessels.
The two 10,000-ton cargo ships are nearing completion at BHP's Whyalla shipyard.
General Electric Company's Gas Turbine
Products Division in the United States manufac- tured the 19,000-hp Model 5000, regenerative cycle, two shaft heavy-duty gas turbine which powers each ship. These powerplants will provide a service speed of 20 knots under all load and weather conditions. The main cargo stowage areas are the lower hold and the vehicle deck—both completely enclosed. Straddle carriers will move the loaded bolsters from the terminal marshalling area to the vehicle deck via the ship's stern ramp.
Shipboard overhead travelling cranes will stack the bolsters in cells in the lower hold. Bolsters also will be stowed on the vehicle deck.
In addition to the built-in cranes, three straddle carriers are carried on each vessel, making it in- dependent of shore-based handling equipment. The 100-foot long articulated stern ramp is designed to allow the vessel to load and unload at a con- ventional berth.
The vessels represent considerable capital out- lay, being larger than conventional vessels of sim- ilar lifting capacity and fitted with more powerful engines and costly equipment such as the stern ramp, watertight stern door and built-in overhead cranes. However, the investment was considered a necessary premium to pay to ensure rapid vessel turnaround, efficient stevedoring and proper pro- tection for the cargo.
The type of bolster which will be used for most products is 20 feet long, 8 feet wide and 4 feet 3 inches high. Drop-down end walls and remov- able side walls are resigned to simplify the loading and unloading. Steel products will remain in the bolster from mill to distribution terminal.
Designed around a 30-ton all-up weight, this type has a tare weight of four tons and a maxi- mum load capacity of 26 tons. With the end walls down, a bolster can carry structural up to 60 feet in length. A locking device at each corner ensures stable stacking of the bolsters. Specially designed covers will be available for products such as tin- plate which require protection from rain damage.
Two additional bolster types have been devel- oped, one for wide tinplate coils and one for plate up to 106 inches wide.
Covered storage sheds and marshalling areas will be available at Melbourne and Adelaide. Each bolster and contents will be identified and stored at the terminal and on the vessels in such a way as to enable loading and unloading in the most efficient and orderly manner possible. Bolster iden- tification also will enable the programming of deliveries from the terminals.
Unloading a Ro/Ro vessel will be completed in one day and the cargo cleared from the terminal within three days of the ship's departure.
Each ship will have an overall length of 588 feet 3 inches, a length between perpendiculars of 553 feet 3 inches, a beam of 82 feet, a depth of 57 feet, and a loaded draft of 30 feet. The GE gas turbine drives a controllable-pitch propeller through reduction gearing. The designed output of this system is 19,000 shp.
The first of the two ships has been launched at the Whyalla Shipbuilding and Engineering
Works. The first ship was christened Iron Mon- arch. The second ship will be named Iron Duke.
A Broken Hill Proprietary Company official stated : "Every aspect has been designed to fif into the total system."
Straddle carrier moves towards open-ended bolster loaded with steel beams. The hinged ends of the bolster have been dropped to allow carriage of beams up to 60 feet long. 6 Maritime Reporter/Engineering News