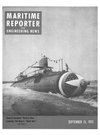
Page 30: of Maritime Reporter Magazine (September 15, 1973)
Read this page in Pdf, Flash or Html5 edition of September 15, 1973 Maritime Reporter Magazine
Babcock & Wilcox Engineers Give Design Guidelines For
Marine Boiler Specifications
The Substantial Advances Made In The Past 10 Years In Marine Boilers
Must Be Included In Specifications To Benefit The Shipyard And Owner
R.A. Grams and R. Schoen III*
The problems and concerns that are impacted by boiler design and operation on the owners and opera- tors of ships must be periodically evaluated and the solutions to these problems must be converted into design features. This can only be accomplished by constant re-evalu- ation and up-dating of marine- boiler specifications.
Of prime importance are the per- formance characteristics to which the boilers must be designed.
Marine-boiler performance should be specified as being in ac- cordance with the following SN-
A'M'E publications: 1. T&R Bulletin No. 3-11—Rec- ommended Practices for Preparing
Marine Steam Power Plant Heat
Balances. 2. T&R Bulletin No. 3-14—Boil- er Furnace Performance Criteria.
Adherence to the calculation methods outlined in these bulletins will provide the purchaser with as- surance that all competitive offer- ings are calculated in a comparable manner.
There are a number of perform- ance items worthy of detailed com- ments. Many of these can have sig- nificant effect on the cost effective- ness of the boiler design.
Until the relatively recent past the only specified criterion for fur- nace sizing was heat release rate or liberation, stated as BTU per hour per cubic foot of furnace vol- ume. A much more significant cri- terion that has come into recent use at the urging of Prof. J.T.
Holm and the boiler manufactur- ers is firing rate per square foot of radiant heat absorbing surface (lbs. oil/ RHA'S) familiarly known as furnace loading. This number is directly related to furnace ab- sorption and is an indication of heat load on the furnace and screen circuits as well as furnace exit gas temperatures. We recommend that values up to 15 pounds oil per square foot of RHA'S at AB'S maxi- mum rating be considered for nor- mal applications. Somewhat higher values can and have been used for merchant units where space limi- tations have necessitated it. Prop- er design and location of the burn- ers is, of course, a vital considera- *Mr. Grams, manager, Functional De- sign, and Mr. Schoen, manager, Ma- rine Applications, Industrial and Ma- rine Division, Babcock & Wilcox,
Barberton, Ohio, presented the paper condensed here before a meeting of the Joint California Sections of The
Society of Naval Architects and Ma- rine Engineers. tion in the design of any furnace.
Naval boilers have operated for many years with full-power furnace loadings in excess of 50.
The most important considera- tion for boilers employing econo- mizers is the proper selection of feedwater temperature. Econo- mizer tube-metal temperature is, for all practical purposes, the same as the water temperature inside the tube due to the extremely high conductivity on the water side rela- tive to the gas side. Thus, at the cold end the tube-metal tempera- ture is the same as the feedwater temperature and is independent of gas temperature. If the feedwater temperature is below the acid dew- point of the combustion gas, con- densation will occur in the form of sulphuric acid.
In order to prevent this from happening the most logical thing is to use high enough feedwater temperature to prevent condensa- tion from forming on the tubes.
Our experience has been that we have observed no failures due to external corrosion when burning
Bunker C oil when feedwater tem- perature has been maintained at 270° F or greater. We feel that 280° F would be a preferable mini- mum in view of the poor quality of many Bunker C oils 'being burn- ed today.
Another solution would be to re- duce the sulphur content of the oil to a maximum of 0.5 percent. The economics of this do not make this approach attractive. In some in- stances reduced feedwater tempera- tures have been used with low alloy or cast iron exposed tube surface. These materials can only retard the inevitable corrosion.
Practical attainable boiler effi- ciency is dependent on the type of cycle used and in the case of an economizer also on the feed- water temperature. The following remarks apply to the three basic types of cycles used:
Economizer-Steam Air Heater-
Terminal temperature difference between economizer exit-gas tem- perature and feedwater at 30° F to 40° F is commonly specified. This results in boiler efficiencies in the range of 88.4 percent to 88.8 per- cent when using a 280° F feedwater temperature. Efficiency is increas- ed slightly (about 0.1 percent to 0.2 percent) if based on 10 percent excess air rather than the custo- mary 15 percent. It is theoretically possible to make a small further increase in efficiency by reducing the terminal temperature differ- ence. Increases beyond these val- ues are not practical as the amount of heating surface required be- comes prohibitive.
Regenerative Air Heater—Boiler efficiencies up to about 90 percent have been used. However, this means that the average cold-end metal temperature is well below the acid dewpoint of the combus- tion gas. Corrosion problems can be alleviated by the use of enam- eled cold-end surface but it must be remembered that a wetted sur- face is conducive to soot buildup and scheduled water-washing pe- riods will be required. Corrosion does not have as severe an impact as with an economizer as the air heater is not a pressure part. Po- tential stack corrosion must be con- sidered when chasing after such high efficiency as the gas tempera- ture in the stack will only be about 220° F when considering the air leakage factor in the air heater.
Tubular Air Heater—These have become virtually obsolete due pri- marily to the extremely large space requirements and their relatively poor metal temperature character- istics. We do not feel that effi- ciencies above 88.0 percent Can be justified with this type of air heater inasmuch as maintenance would become prohibitive.
Substantial savings in cost and size can be made if the purchaser can tolerate an increase in desuper- heater outlet temperature and in pressure drop at the design rating.
We feel that in many instances this is not investigated. For example, if the desuperheater outlet tem- perature could be designed for 100° F of superheat and the speci- fications stated 50° F of superheat, it would have roughly twice as much heating surface as was really necessary. Added allowable pres- sure drop has a similar effect in reducing heating surface as it al- lows the use of increased steam mass flow with resultant increased heat-transfer rate.
Present very large crude carrier designs require considerably larger auxiliary steam demands for cargo heating and butterworthing. It is possible that if these huge de- superheated steam requirements continue to increase, external de- superheaters may become a ne- cessity.
Along with the economizer, the usual steam-plant cycle would call for a steam air heater. This type of purchased equipment is well standardized and requires little comment. However, we suggest your heat-balance engineers re- evaluate the need for the air tem- perature to be within 25° F of the saturated steam temperature sup- plied as the source of heat for this heat exchanger. Present fuel-oil burning technology is such that a 50° F differential could be tolerated without influencing the combus- tion characteristics in a furnace.
A reduction in steam air heater size would result if this parameter is accepted. The performance char- acteristics of this equipment are such that at low boiler ratings, when higher air temperatures are desirable for good combustion, the air temperature would be within 25° F of the saturated steam sup- plied.
Typical Specification
We will attempt to analyze a typical specification and point out several areas that should be evalu- ated carefully. At the present time, the only document available for guidance is Section 61 of the Mari- time Administration's Standard
Specification for Cargo Ship Con- struction. This specification, all too often, is used without modifica- tion, to the detriment of the ship- yard or ship owner.
Of prime importance at the start of any machinery selection activity is the space allowed for installa- tion. Machinery arrangement plans or at the minimum, box volume dimensions, must be provided. This would assure the prospective buy- er in obtaining the most economi- cal physical arrangement of boiler pressure parts.
A prevalent misconception re- garding boiler design is that ex- ternal downcomers are a necessity for adequate boiler circulation, par- ticularly in larger capacity units.
We have argued against this and believe that internal downcomers should be used whenever possible —that is, to arrange the design to allow the last several rows of gen- erating bank tubes to act as down- comers. In this manner the down- comers are distributed over the full length of the drum. With external downcomers the steam drum is sub- jected to end flow of water result- ing in a water-level gradient in the drum. This gradient is additive to the effects of pitch and roll of the vessel, an undersirable feature from the standpoint of steam-water separation.
Also, external downcomers are relatively expensive and contrib- ute nothing to reducing gas tem- (iContinued on page 34) 32 Maritime Reporter/Engineering News