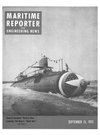
Page 32: of Maritime Reporter Magazine (September 15, 1973)
Read this page in Pdf, Flash or Html5 edition of September 15, 1973 Maritime Reporter Magazine
Marine Boilers— (Continued from page 32) perature in the boiler. The primary- limitation on internal downcomers is operating pressure, due to the reduced differential between steam and water densities as pressure in- creases. However, there is no ques- tion that conservative internally downcomer designs can be made up to design pressures of 1,500 psig and possibly somewhat higher.
Considering boiler pressure parts arrangements, some concern should be noted regarding boiler steam- drum size. With the demand for higher horsepowers, it becomes quite evident that as boiler evapo- rations increase, so do furnace depths and in large boilers with long drums, the effect of trim is indeed severe. Therefore, merely stating the minimum drum diame- ter shall be 54 inches, no longer is adequate. As a general rule of thumb, boiler evaporations exceed- ing 120,000 pounds of steam per hour, should be fitted with 60-inch nominal diameter steam drums.
Likewise, boilers in excess of 200,- 000 pounds of steam per hour should be fitted with 66-inch nomi- nal diameter steam drums.
Boiler-bank configurations are fairly well standardized. However, waterwall arrangements should be specified in some greater detail.
Tangent tube installations should be defined as tubes with % inch or less clear space between adjacent tubes. Membrane-wall construc- tion can be considered as an equal- ly acceptable alternative. The fir- ing wall or front wall could be constructed non-tangent if the spe- cification called for high-grade re- fractory backing. As regards wa- ter-cooled burner throats, for front- firing arrangements, this could be considered an excessive require- ment. However, for top-fired boil- ers, recent service feedback indi- cates that in order to minimize burner throat refractory replace- ment, water-cooled burner throats should be specified.
Regarding superheater arrange- ments, perhaps now is the time to correct a popular misconception, i.e., the cleanability of a vertical superheater arrangement versus a horizontal superheater arrange- ment. Cleanability is a function of fuel, type of atomization, tube ma- terial and gas temperatures. There is no significant advantage to either a vertical or horizontal arrange- ment with regard to cleanliness.
However, care should be taken when deciding on the superheater arrangement to be used, for as boil- er sizes increase so do furnace depths. With extremely deep fur- naces, horizontal superheater sup- port problems arise and space for removal of superheater elements becomes excessive.
Slagging and corrosion potential is a function of gas temperature and the tube-metal temperature as well as the type of fuel ash char- acteristics. Therefore, based on our operating experience and test data we agree that a tube-metal tem- perature of 1,050° F is a safe op- erating limit.
Recently, several owners have re- quired the inclusion of a means of monitoring gas temperatures in way of the superheater, during boiler lite-off. A well-proven op- erating procedure in industrial and stationary practice, this may prove a significant requirement in the fu- ture for marine applications. At a relatively low extra cost, each boil- er could be furnished with a re- tractable thermoprobe, fitted with alarms and/or recorders for moni- toring gas temperatures during lite-off. Maximum oil-firing rates during start-up could then be established safely and superheaters would not be subject to over firing at extremely low steam-flow con- ditions.
We do not agree that there should be a cutoff point, based on 850° F steam temperature, below which superheater tubes in the same superheater, should be rolled into superheater headers. We be- lieve modern marine boiler super- heaters should have all superheater tubes welded in a manner approved by the Coast Guard.
Reports from owners indicate superheater header handhole plate leakage to be a significant mainte- nance item. We therefore suggest that future specifications indicate welding of these handhole plates for 1,100 psi design pressure units and certainly for design pressures in excess of 1,100 psi.
Material selection for sub- merged-coil desuperheaters for sup- plying auxiliary steam, based on inlet steam temperature levels in existence today, (900° F to 960° F) requires a re-evaluation of poten- tial corrosion problems. Tests of various low alloys up through Cro- loy 5 have shown very little, if any, improvement in corrosion re- sistance relative to plain carbon steel. At the present time, the only material with a proven record of superior corrosion resistance in high-temperature desuperheaters is 16-1 chromium-nickel alloy (ASTM 268 TP 430). This is a premium material which will significantly reduce the corrosion problem and should therefore become a boiler requirement.
The superheat control desuper- heater can be easily located inter- pass in the superheater, such that its material can be specified as car- bon steel.
We suggest that air-cooled ther- mal sleeves be the only method employed for inlet connections.
Outlet connections should be fitted with steam cooled sleeves. Under no circumstance do we recommend water-cooled thermal sleeves.
We take exception to designing desuperheaters for full boiler pres- sure and suggest a more realistic approach of designing for differ- ential pressure.
In designing any piece of heat- recovery equipment for use in ihigh- efficiency applications, thought must be given to the prevention of condensation of sulphur-laden flue gases. When the uptake gas tem- perature and heat-transfer-metal temperature relationship is such that condensation takes place, rapid soot buildup and corrosion of this tube metal occurs. Therefore, an acceptable metal temperature should be maintained in order to minimize corrosion. When design- ing an economizer the proper se- lection of feedwater temperature is important and the feedwater in- let temperature must be kept above the acceptable metal temperature since the tube itself is very close to the feedwater temperature.
We maintain the use of cast iron as not being satisfactory for corro- sion protection as any protection offered by cast iron is due to its mass rather than superior corro- sion resistance. The Bureau of
Mines Report of Investigation No. 4996, dated August, 1953 contains data on corrosion resistance of va- rious materials in a flue gas atmos- phere. The report states that "the corrosion rate of cast iron was about Al/2 times that of Corten and 2Yz times that of ordinary open- hearth steel, an unexpected result."
Increasingly more apparent, as the size of boilers increases, is the duty imposed on the heat-recovery equipment. Economizer sizes are such now that strong considera- tions should be given to mounting this equipment separate from the boiler. Space available in the fidley area of most vessels makes this arrangement very attractive. The economizer completely assembled and air encased could be set easily and conveniently on ship struc- tures at minimum costs.
An alternate to the economizer- steam air heater cycle is the regen- erative gas-air heater cycle. The ability of the regenerative air heat- er to operate at lower metal tem- peratures than other types of heat- recovery equipment results in addi- tional heat removed from the exit gas. This heat is transferred to the combustion air and complete com- bustion is more readily accomplish- ed. When the air temperature in- creases, the combustion process accelerates and this process can be carried out with less excess air.
If the excess air is reduced, the exit gas volume and, therefore, the heat losses are lower. Thus the efficiency of the overall boiler cycle can be increased by virtue of the lower exit gas temperature. How- ever, great care should be exercised in establishing the designed effi- ciency so that the cold-end transfer surfaces are not placed in danger from the acid-corrosion phe- nomena.
Of major importance in any boil- er design is the assurance of gas tight integrity of the boiler cas- ings. Assurance of this gas tight integrity can only be afforded by employing double casings around the boiler. Regardless of type of construction, i.e., tangent tube or membrane wall, we strongly recom- mend the entire boiler be double case and pressurized. In order to attain 130° F outer casing tem- perature, a good circulation of cooling air must be provided ex- ternal to the casings by the ship's ventilation system. An air velocity of three feet per second over the casing must be provided.
Lialbility considerations are such that insistence on complete double- cased boilers is essential.
Mountings or boiler appurte- nances are generally items that are clouded with confusion during the specification stage of any boiler ne- gotiation. It is suggested that the industry standardize on what might be called a "normal scope of sup- ply" furnished by the boiler manu- facturer. This normal scope of sup- ply would include safety valives, soot blowers and water gages, on- ly. Other mountings as necessary could be purchased directly by the shipyard or ship owner at some- what less cost.
A well-written specification should also include at this stage a well-defined list of equipment to be supplied by the boiler manu- facturer as well as a list of equip- ment to be supplied by the ship- yard or ship owner.
As in the case of some mount- ings, we feel boiler controls such as feedwater regulators, combus- tion controls, steam temperature controls and fuel-oil burner-man- agement systems should be negoti- ated directly with control suppliers.
With minimu'm engine-room man- ning and bridge control as a re- quirement, it is suggested that a complete package from a one source responsible supplier be in- vestigated.
As a result of the poor grades of fuel available to the marine in- dustry, we feel that furnace re- fractories should be considered in more detail. We recommend that boiler designs with spacing be- tween adjacent furnace tubes of % inch or less, FCE-33 refractory ma- terial be specified. We further recommend that designs with inch or more clear Spacing between tubes and in all areas of exposed refractory, PCE-34 material be spe- cified.
Of recent interest is the subject of stringent rules on working con- ditions when installing asbestos- bearing materials, imposed by the
Government's Occupational Safety and Health Administration (OS-
HA). Many shipyards have now decided that the restrictions on the procedures used when handling asbestos-ibearing materials are so difficult to comply with, that the preferalble course is to eliminate asbestos-ibearing material entirely.
We agree with this decision and suggest that insulation specifica- tions 'be revised to reflect this change.
Fuel-oil burner specifications ap- pear to us to be adequate. How- ever, we wish to point out that with any wide-range, internal-mix, steam-atomizing burner, it is avail- able to start up with steam or compressed air atomization in use, rather than straight mechanical.
Straight mechanical adaptation should be employed for emergency use only.
It is an objective of all design engineers to identify and meaisure those areas of the steam-generat- ing system that are responsible for maintenance expense. Once identi- fied, it is then incumbent upon the boiler design engineer to improve the situation. 34 Maritime Reporter/Engineering News