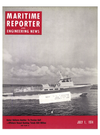
Page 12: of Maritime Reporter Magazine (July 1974)
Read this page in Pdf, Flash or Html5 edition of July 1974 Maritime Reporter Magazine
1NCO Engineers Survey Current Practices To
Evaluate Your Shipboard Piping Systems
Based On First Cost Versus Annualized Cost
A.H. Tuthill and S.A. Fielding*
There has been a considerable upgrading of shipboard piping sys- tem materials especially in the larger, more expensive modern cargo and tanker vessels in the last decade. This upgrading has, in all too many cases, fallen short of the improvement in reliability and reduction in maintenance the ship operators expected. The rea- sons for specific shortcomings vary widely, but 'the result has been premature failure and substantial maintenance in systems the owner expected to last the full life of the vessel.
A key problem appears to be a lack of understanding on the part of those developing the piping spe- cifications, and on the part of the yards building to these specifica- tions.
For example, a logical decision to paint a steel or cast-iron water- box to extend its life can and has led to: premature localized pitting- type failure of the waterfbox itself; increased failures of aluminum- brass tubes; increased dezincifica- tion of naval brass and Muntz- metal tube sheets, and partial blockage and additional condenser tube failures as the coating 'begins to fail and spall toward the end of its normal useful life.
Another logical decision that has led to seemingly unassociated, and certainly unanticipated results, is the decision to upgrade from steel to nonferrous piping but stay with standard "off-the-shelf" marine brass and bronze pump and valve components. Upgrading to nonfer- rous piping deprives the "standard marine" brass and bronze alloys of the cathodic protection they re- quire to reduce their normal corro- sion rates in seawater to the point where they give useful service.
In another category is the deci- sion to automate sections of the auxiliary seawater cooling system so that banks of unneeded heaters and coolers are taken out of serv- ice and the flow increased propor- tionately through the heaters and coolers left in service. Such auto- mation has resulted in excessive ve- *Mr. Tuthill and Mr. Fielding of the
International Nickel Company presented the paper condensed here before a re- cent meeting of the Eastern Branch,
U.S.A., of The Institute? of Marine Engi- neers. The full paper contains many tables on corrosion rates and costs. locities and turbulence failures in small diameter (principally 4-inch and smaller) nonferrous piping.
Other problems encountered in- clude : nonferrous pipe failures from turbulence downstream of short-radius fittings or downstream of internal obstructions from poor- ly fitted, field-fabricated tees and
Y's; condenser-tube failures from excessive air entrainment in cer- tain higher-speed cargo vessels with bottom^itted scoop injection; tube failures from polyethylene bags entering the condenser in ships with no provision for removal of entrained debris; tube failures from biofouling growth in bare steel, coated, or rubber-lined steel waterboxes and piping, and prema- ture failure of brass and bronze alloys in modern, high rotational speed pumps.
There is also the matter of cost.
When an owner pays a premium to obtain a high reliability piping system that is expected to last the life of the vessel, he naturally ex- pects to receive a system that will not fail prematurely, require costly shutdowns, or necessitate early replacement. Owners have few, if any, reliable published standards for piping systems that will insure this result. They can incorporate such piping standards as the naval architect has develop- ed in the invitation to bid. Alter- nately, the owner may simply ac- cept the successful bidder's "stand- ard vessel" piping system.
In either case he is often request- ed by the shipyard to approve alternate materials if he wishes to avoid a delay in vessel delivery.
Given the present design and pro- curement system, the variations in component availability and cost, and the numerous side effects of changes, it is little wonder that there are some modern multi-mil- lion dollar vessels with leaking pipes, condensers and heat ex- changers.
There are really only two pos- sible seawater piping systems.
First, there is the older style, "low" first-cost system based on coated steel pipe and waterboxes, brass tube sheets, and aluminum-brass tubes. Second, there is the high reliability, minimum maintenance system based on copper-nickel pipe, waterboxes, tube sheets and tubes.
Both the low first-cost and the high reliability systems are true systems in that each component interacts with and directly affects the performance of other nearby components —• galvanic, biofouling, and corrosion products. There are also two additional interactions arising from the detailed design of the system and the inherent properties of the materials used— velocity and debris. All interac- tions occur in both systems and each has a pronounced effect on condenser performance. These in- teractions are summarized as fol- lows :
Biofouling Interaction — Bare steel, coated, or rubber-lined water- boxes and piping provide a benign habitat where marine organisms attach, grow, and multiply within the system itself. Attachment oc- curs primarily at flow rates below three feet per second. This hap- pens when the ship is in port and the circulating-water system is shut down. Once attached, and attach- ment occurs in a matter of hours, the organisms remain attached and grow at the normal operating flow rates. Ultimately the marine organisms die and are swept into the condenser—plugging tubes, re- ducing flow, and increasing tube failure rates. Ships operating in different trade routes develop these internal colonies of marine organ- isms at different rates, depending upon the number of calls 'they make to ports with relatively clean water in temperate and tropical areas where the incidence of these organisms is greatest.
Two countermeasures have been used or advocated—physical ream- ing out of pipe and waterboxes, and chlorine injection. Chlorine injec- tion units are produced and pro- moted for shipboard use, especially in Japan where a high percentage of ships are still fitted with steel circulating-water system piping.
While there is no cost data avail- able to the authors on these ship- board units, Dow Chemical Com- pany has estimated a capital cost of $25,000 for a chlorination sys- tem in a coastal plant suitable for treating 14,000 gallons per minute of seawater in a 36-inch-diameter intake pipe. Chlorine costs (at six cents per pound) are reported as $8,700 per year. Manhours per year are estimated as 250. It is reason- able to expect shipboard chlorina- tion costs would be comparable.
The proponents of shipboard chlorination clearly recognize that biofouling control within the piping system is necessary to improve condenser performance. What is not so clearly recognized is that effective biofouling control can be achieved by the use of 90-10 copper- nickel piping and waterboxes and that the use of 90-10 copper-nickel for the pipe and waterbox results in much improved condenser-tube per- formance. Just how much condenser performance can be improved by the use of fouling resistant 90-10 copper-nickel piping is easily ap- preciated when naval experience is evaluated. The 0.27 percent 20- year condenser tube plugging rate reported can be credited in consid- erable measure to the use of foul- ing-resistant 90-10 copper-nickel piping on these and all naval ves- sels. The authors believe that simi- lar condenser-tube performance can be achieved by any shipowner with a properly constructed, reasonably well operated system fitted with fouling-resistant 90-10 copper-nick- el pipe and other high reliability system components.
Galvanic Interaction—Seawater is a low resistance electrolyte and intensifies the galvanic interaction between nearby components of dif- ferent composition. In seawater circulating systems the galvanic in- teractions of primary concern are those between valve bodies and the piping, between valve trim and the valve bodies, between the wa- terbox and tube sheet, and between the tubes and tube sheet. Adverse galvanic effects can be costly when the owner or shipbuilder fails to consider fully the relative potential and the relative area ratios as they influence galvanic corrosion in evaluating alternative materials for use in the various components of seawater piping systems.
Corrosion Product Interactions —The voluminous corrosion prod- ucts generated when steel or cast- iron pipe corrode are sufficient in themselves to plug condenser tubes and increase tube failure rates.
However, the ferrous ion released in the corrosion process has a bene- ficial effect on both the formation and the stability of the protective corrosion-product film on which aluminum-brass tubing depends for its performance. So pronounced is the effect of ferrous ion that one of the leading authorities on con- continued on page 19) 10 Maritime Reporter/Engineering News