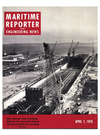
Page 21: of Maritime Reporter Magazine (April 1976)
Read this page in Pdf, Flash or Html5 edition of April 1976 Maritime Reporter Magazine
Vancouver Shipyards Moves 457-Foot Ferry
To Launching Position On Film Of Water
The 3,500-ton ferry, Queen of Alberni, is shown being positioned on launching ways by using the Aero-Caster System, developed by Aero-Go, Inc.
In February, shipbuilders and drill-rig manufacturers from several countries gathered at
Vancouver Shipyards, North Van- couver, British Columbia, Can- ada, to watch a 7,000,000-pound ship transferred to launching position on a film of water 5/1000 of an inch thick. It was the heaviest weight ever to be moved by the newly developed fluid-film method. A week later, the ferry was launched.
The vessel is a trailer ferry, 457 feet long and 89 feet in beam, one of three of the same hull size constructed for the British Co- lumbia Government Ferry Sys- tem. The almost completed ferry weighed 3,500 tons when it slid along its smooth, level concrete pad to launching position. Pulling power was supplied by a con- verted log skidder exerting ap- proximately 7,000 pounds of force or about one pound of force for every 1,000 pounds of ship's weight. So frictionless is this transfer system that precautions must be taken to hold ships' hulls against forces exerted by sudden gusts of wind.
The transfer operation and the launching mark the culmination of a $4.5-million expansion pro- gram for Vancouver Shipyards from its planning stage in 1974.
The yard's fluid-film transfer op- eration takes place on smooth con- crete runways forming a grid in the construction area. The system recently developed by Aero-Go,
Inc. of Seattle, Wash., is designed to move large units by use of a series of 40-ton-capacity, 4-foot- diameter waterfilm bearings. The bearings are essentially inflatable "doughnuts" manufactured of flexible nylon-neoprene and hypa- lon materials. When inflated with water at a pressure of 50 pounds per square inch, each bearing lifts 40 tons. The total thrust exerted by all the bearings raises the load approximately two inches.
At this point, water seeps from a contained supply in the center of the "doughnuts" onto the level concrete runway. The ship's hull, mounted in its wooden cradle, is now free-floating on a paper-thin film of water, and is ready to be transferred.
The ferry hull was constructed in seven different sections or mod- ules, each of which was trans- ferred to join the others by means of the fluid film system.
President of Vancouver Ship- yards, Allen Fowlis, expressed satisfaction with the new ship- yard arrangements: "The fluid- film transfer system and our side-launching facility make it possible to compete effectively with shipbuilders anywhere in the Pacific Northwest," he said. "In two years we have doubled our shipbuilding facilities, as well as adding a capacity to build ships up to 500 feet in length and 100 feet in beam."
He commented in particular on the flexibility of the construction system. "We have avoided com- mitting ourselves to a more rigid system such as graving dock and end-launching facilities," Mr.
Fowlis said. "What we have now is something close to an assembly- line system. We can build ships' modules under cover, move them into desired positions around one another, past one another, or joined to one another."
Aero-Caster waterfilm load module used by Vancouver Shipyards is 4 feet square, 3 inches thick, and weighs 170 pounds.
One of the Aero-Casters in position and under water pressure is shown between concrete runway and ship cradle.
He said that if supply prob- lems delayed the construction of one vessel, it could be moved aside to make way for other con- struction. The resulting savings in time and money are substan- tial, and efficiency is substantially improved.
The vessel is among the largest double-ended ferries in the world and is the largest vessel ever con- structed by Vancouver Shipyards.
Its engines develop 11,000 shp and will provide a service speed of 20 knots. It has a passenger capacity of 350 and can carry either 58 forty-foot trailers or 145 automobiles. Soon to be com- missioned by the provincial gov- ernment, the ferry will go into service between Vancouver and
Vancouver Island.
The Aero-Caster® System is the exclusive development of
Aero-Go, Inc., 5800 Corson Ave- nue South, Seattle, Wash. 98108, with international sales of both water- and air-inflatable handling products. Floating heavy loads on fluid-film systems so nearly elim- inates the friction under them that only a gentle one-pound push for every 1,000 pounds of load weight is needed to move them in any direction and speed desired.
To move varying section sizes and weights, the proper number of Aero-Casters are used. They are positioned under loads in rec- tangular arrangements for load balancing. The lift capacity of a fluid-film system is unlimited.
Flow control valves at each Aero-
Caster automatically gage the water flow needed by the caster to lift the load weight above it.
Once the Aero-Casters are in position, there is no need to man- ually adjust pressures to move a hull unit as its weight changes during completion.
Todd Shipyards Corporation's
Seattle yard was the first ship- yard in the world to use an Aero-
Caster transfer system to build vessels in the 1,000-ton range.
Their Aero-Caster system pro- vides the capability of easily transferring ship subassemblies from rail and wheel bogies onto waterfilm. It also includes a waterfilm turntable for 90-degree rotation of ship assemblies weigh- ing up to 500 tons. Todd has had as many as four 228-foot-long by 44-foot-wide ships side-by-side at one time parallel to their side- launchways moved into position on waterfilm.
Since December 1974, Brown &
Root, Inc. in Houston, Texas, has been using an Aero-Go waterfilm pallet system to move offshore oil-drilling platform decks. Weigh- ing up to 2,000 tons, steel decks are floated from inside their fab- rication building on air film and throughout their outside yard and onto barges on waterfilm. Move distance is approximately 500 feet. Deck sizes are typically 60 feet high by 72 feet wide by 163 feet long. Two fluid-film pallets are inserted in recessed feet un- der each of the deck's eight co- lumnar legs.
Several foreign yards are using
Aero-Go systems to move heavy equipment within shops and to position engines. At Sasebo Heavy
Industries, Japan, Aero-Casters are inverted atop pedestals to float steel deck-plate assemblies above them to join them for welding. Aboard ship, air film is used to install prefabricated cab- ins and auxiliary equipment.
Aero-Go introduced the Aero-
Caster air-film device in 1967 and the waterfilm Aero-Caster in 1971.
Systems are now in use in hun- dreds of diverse industries world- wide, ranging from total in-plant air-film production-conveying lines to the shock-free movement of 1,000-pound sensitive elec- tronics.
April 1, 1976 23