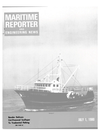
Page 23: of Maritime Reporter Magazine (July 1980)
Read this page in Pdf, Flash or Html5 edition of July 1980 Maritime Reporter Magazine
Frank McGrath Named
Chief Engineer At
Peterson Builders in 1961 as a physicist in the Elec- trical Products Laboratory, and returned to the University of
Minnesota to complete his doctor- ate in 1970. After joining the
Martin Marietta Laboratories in 1970, Dr. Mularie returned to the
Components and Devices Labora- tory of the Industrial Electrical
Products Division of 3M in 1974, and joined the Central Research
Laboratories in September 1978.
Beker Maritime Seeks
Title XI On Two Dredges
To Cost $10 Million
Beker Maritime Company, a
Bradenton, Fla., subsidiary of
Beker Industries Corporation,
Greenwich, Conn. 06830, has ap- plied for a Title XI guarantee to aid in financing the construction of two cutterhead pipeline dredges.
The 5,000-bhp vessels are to op- erate on the inland waters of
Florida.
If approved, the Title XI guar- antee would cover $8,750,000, or 87y3 percent of the total cost of $10 million.
Deliveries have been scheduled for January and April 1981; the shipbuilder has not yet been de- termined.
Frank McGrath
Peterson Builders, Inc. recently announced that a number of changes had been made within their Engineering Department.
The shifts made included assign- ing Frank McGrath to the posi- tion of chief engineer of the de- partment. He will have direct responsibility for the Hull De- partment, Mechanical/Piping/
Heating/Ventilation and Air Con- ditioning Department, Electrical/
Electronics Department and the
Engineering Group. Mr. McGrath's former duties included the respon- sibility of serving as the Patrol
Gunboat Program engineering production manager on the 190- foot Aluminum PGG program with the U.S. Navy.
Additional engineering shifts made at PBI were comprised of promotions within three of the pri- mary engineering subdivisions at the shipbuilding facilities. They included the following promo- tions to department heads in their respective divisions: Gaylen La-
Crosse-Mechanical / Piping / HV-
AC; Richard Yedica-Hull/Outfit- ting; Eugene Hody-Electrical/
Electronics. As department heads, these three individuals will be re- sponsible for all design and draft- ing pertinent to their subdivisions, coordinating the engineering data that flows to and from production areas.
W.M. Mularie Named
Research Director
For American Hoist
A 10,000-psi jet of water promises to revolutionize routine on-board maintenance... especially rust and scale removal of surfaces to be painted.
Butterworth Systems now offers a modern alternative to the age-old chipping hammer. It's their MARINE
LIQUA-BLASTER*
Dr. Wm. M. Mularie
Robert P. Fox, president and chief executive officer of Amhoist (American Hoist & Derrick Com- pany), St. Paul, Minn., announces the creation of a new Corporate
Research Department.
Dr. Wm. M. Mularie has joined the new department as director of corporate research. He joined 3M
Diesel powered pump of a
MARINE LIQUA-BLASTER onboard a vessel. ultra-high pressure water- blasting equipment.
Especially developed for shipboard use at sea, the MARINE
LIQUA-BLASTER unit uses a diesel or electric powered pump to generate a 10,000-psi jet of water that is directed by a fail-safe, hand-held gun at the surface being descaled. "White-metal" cleaning.
On a badly rusted surface, "water only" blasting removes scale and debris, leaving a surface that is acceptable for standard maintenance painting. If a moderate amount of sand is automatically added to the water jet, a surface can be "white-metal" cleaned more effectively and more efficiently than it would be with dry-sand blasting in a shipyard.
With the MARINE
LIQUA-BLASTER unit, a rust inhibitor can be added to protect the "white-metal" surface against oxidation before painting.
Introducing the Butterworth
Systems
MARINE
LIQUA-
BLASTER*
SHIP MAINTENANCE SYSTEM.
Better than dry-sand blasting.
Because of the high velocity of the water/sand jet, the sand impacts a rusted surface with a much greater force than with regular dry-sand blasting.
The end result is faster cleaning using less sand.
Respirators are not required since no dust is generated. Clean-up is also easier.
Other shipboard cleaning.
In addition to descaling rusted surfaces, a MARINE
LIQUA-BLASTER unit can be used for a number of other on-board cleaning jobs. These include cleaning condenser and boiler tubes, oil spray from machinery, galley grease filters, clogged ports, and the like. For these jobs, as well as rusted surfaces, a variety of guns, lances, round and fan jet nozzles are available.
Proven on-board use.
The experience on a 69,742-DWT tanker, is typical of other vessels that have used MARINE
LIQUA-BLASTER equipment. Here, it was first used to clean a badly rusted 550-square-meter poop deck. The job was done as routine maintenance with interruptions for bad weather and all-hands tasks. In a little over two weeks the poop deck was "white-metal" cleaned and freshly painted.
Doing the same job in a shipyard would have cost $13,750 at $25 per square meter not including the incremental lay up time to accomplish this task, jjfc wbmm, • m.
Heavily rusted deck (below), after water blasting (left), and "white-metal clean after water-sand blasting (right)."
Get all the facts.
For full details and a copy of an eight-page report, "Shipboard
Cleaning and Descaling with Ultra-high Pressure
Water Blasting", write or call today.
Butterworth
Systems
BUTTERWORTH
SYSTEMS INC. 224 Park Avenue, Box 352,
Florham Park, N.J. 07932 USA
Telephone: (201) 765-1549
Telex: 136434
BUTTERWORTH
SYSTEMS (UK) LTD. 445 Brighton Rd., So. Croydon,
Surrey CR2 6EU, England
Telephone: 01-668-6211
Telex: 946524
PARTEK CORPORATION
OF HOUSTON 3721 Lapas Drive
Houston, Texas 77023 USA
Telephone: (713) 644-3636
Telex: 762199
July 1, 1980 23