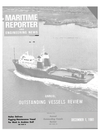
Page 15: of Maritime Reporter Magazine (December 1981)
Read this page in Pdf, Flash or Html5 edition of December 1981 Maritime Reporter Magazine
maneuverability, propeller cavi- tation and oscillations, exhaust gas flow, and wind load. Equally exhaustive tests were made re- garding static and dynamic be- havior of the structural elements.
Noise, vibration, and ventilation tests were conducted with full- scale, mock-up cabins.
When the Europa was de- signed, special attention was paid to environmental protection, and as a result the ship satisfies all conceivable national and interna- tional requirements.
Wind tunnel tests were con- ducted so that passengers would not be exposed to exhaust gases on the open-air decks. This was achieved. The design and dimen- sions of the funnel keep away all exhaust gases.
Engine exhaust outlets: noise and dirt on open-air decks is min- imized by combining various sound-reduction units. Engine ex- haust outlets have separate noise- reducers. There are a total of 11 exhaust outlets: two for the main engines, five for the diesel gen- erators, one for the port emer- gency diesel, two for the auxil- iary boilers, and one for the gar- bage incinerator.
Exhaust gas outlets from the garbage incinerator: soot and odors from this unit are also nonexistent on the open decks.
The garbage incinerator is fitted with nine parallel cyclones which separate ash on the gravity prin- ciple.
Three sewage treatment plants are provided for waste disposal.
The following installations are provided to prevent oil pollution: two sloptanks for the storage and interception of bilge water; two oil extraction units for the sep- aration of bilge water. The de- oiled water conforms to the latest
IMCO regulations for coastal wa- ters (oil residue of less than 15 ppm ; and water pumped over- board by the extraction units is continually monitored. If per- mitted levels are exceeded, the in- stallations automatically stop the discharge of oil-polluted water.
Oil residues are burnt in the gar- bage incinerator.
Garbage is collected by means of a shaft running underneath all the accommodation decks.
Facilities are also available aboard the Europa for the dis- posal of noncombustible solid ob- jects such as bottles and cans.
Award RCA $339 Million
In Contracts For Navy's
Aegis Weapon Systems
RCA Missile and Surface Ra- dar, Moorestown, N.J., has re- ceived $339 million in contracts for Aegis weapon systems for three additional U.S. Navy ships in the Aegis class of guided mis- sile cruisers.
The awards cover production and integration effort for the third and fourth cruisers in the series, CG 49 and CG 50. Delivery of the weapon systems for these ships is scheduled for 1983-84.
The awards also encompass long-lead production items for CG 51, the fifth cruiser in the class.
The Aegis class's first ship,
Ticonderoga, was christened
May 16, 1981, by First Lady
Nancy Reagan. Ticonderoga will be commissioned and join the fleet in early 1983.
The Aegis weapon system, which is the nucleus of the cruis- er's combat system, was devel- oped by RCA. Radar-based and computer-controlled, the system is capable of automatically de- tecting, tracking, and engaging multiple missile, aircraft, and surface threats simultaneously.
RCA produces AN/SPY-1A ra- dar systems for the Aegis weap- on systems which are assembled and tested — less ordnance — at
RCA's Moorestown plant prior to delivery to Ingalls Shipbuilding.
RCA is also responsible for en- gineering and integrating the complete ship combat system.
Aegis cruisers form a new class of gas turbine-powered ships based on the proven hull and propulsion system designs of the
Spruance-class destroyers. The
Navy plans to build at least 18 of the Aegis cruisers during the 1980s. The $338.9-million awards include previously announced funding of $109.7 million for long-lead production for the third and fourth systems.
Increase Profits The REEL-©-fTlflTIC Way! ** srsTtms. mcotfO««TED **
TAKE-UP, PAY-OUT & COIL YOUR
WIRE, WIRE ROPE, CABLE AND
OTHER FLEXIBLE MATERIALS.
Shaftless Pay-Out & Take-Up Machinery
ROM's WT (Walk-Through) Pay-Out and WTCD (Walk
Through Center Drive) Take-Up Series machinery allows the machine to be bolted right to the floor. When the reels are loaded and unloaded they sit directly on the floor. No pits, ramps or shafts - jus,t labor saving speed and safety. Lifting and Stub Shaft (pintle) positioning is achieved by an independ- ent hydraulic system.
UP TO 20,000 LB. CAPACITIES*
Stationary Reeling & Coiling Machinery
For those applications needing the benefit of a stationary reeling and coiling machine, the RSVSISeries is the answer.
This model utilizes a hydraulic jack for raising and lowering the reel. The RSVSISeries is specifically intended for use in heavy duty applications and under maximum load conditions.
UP TO 5,000 LB. CAPACITIES*
Floor Mounted Pintle Take-Up & Pay-Out Equipment
Ji ri
The FMPT 5M shown above is a floor mounted pintle type shaftless take-up machine. Lifting and stub shaft (pintle) positioning is achieved by hydraulic cylinders with a touch of a button.
A hydraulic motor for power winding the material onto the reel is used. The FMPT, like much of
ROM'S product line, requires a single operator.
UP TO 20,000 LB. CAPACITIES*
TWO YEAR WARRANTY ON ALL PRODUCTS
CALL (717) 252-3614 About Your Special Applications ® Or Write: 418 Hellam St.
Wrightsville, Pa. 17368 REEL-o-mnnc
SYSTEmS. IfKORPORRTSD
December 1, 1981 Write 385 on Reader Service Card Write 403 on Reader Service Card 69