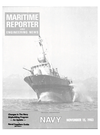
Page 40: of Maritime Reporter Magazine (November 15, 1983)
Read this page in Pdf, Flash or Html5 edition of November 15, 1983 Maritime Reporter Magazine
Productivity Advances
In Shipbuilding (continued from page 39) ship are constructed of these rela- tively easy-to-build units.
At least part of the. art of break- ing the ship up into units is to se- lect as many units as possible which can be constructed using the techniques associated with the less complicated categories. Then, again under the guidance of IHI advisors, Avondale set aside cer- tain areas of the shipyard where this type of construction would be carried out exclusively.
The result is that in the areas where this type of construction is accomplished, the workers accom- plish exactly the same kind of work each day. As they complete one section, the ship section moves to the next work site, and another section is constructed at the first site by the same people using ex- actly the same techniques. This then leads to the description of this process as a "production-line shipbuilding technique."
Outfitting
The second major change in technique is the installation of piping, ventilation and other sys- tems on each of these units as they are being constructed. Thus, after one unit of the hull reaches the appropriate level of construction, it will be moved to a location in the shipyard where the pipefitters and ventilation people and other system installers will take over and install their systems. This is called "outfitting" the unit.
Following outfitting, the section of hull may go to a different spot in the shipyard where another piece of plate will be added to cover up that area that has just been worked on. In this way, each system is installed at the point of construction where it is most eas- ily installed. One essential point to note at this point of construc- tion is that the design of the entire piping system in that portion of the ship must already have been completed.
Thus, by the time the entire unit is ready to be erected at the erection site, the majority of all the internal work has already been accomplished. All that remains to be done is to join the piping sys- tems in one unit to the piping sys- tems in another unit with short lengths of pipe called connecting pieces. The wireways for electrical installations will be installed dur- ing this period but the cables ac- tually are run after the units have been assembled.
Packaging
The third major difference in construction technique involves utilization of so-called "package units." The package unit is a com- bination of related equipment, such as pumps, controllers, gageboards, etc., constructed and installed on their foundations and all piped and wired. It is completed as a package with the entire system constructed and tested before installation.
Engineering
Now, concerning the engineer- ing efforts. This requires a consid- erably different effort on the part of the design and engineering per- sonnel in order to effect these sav- ings for production personnel.
The entire design must be vir- tually complete before production can efficiently start. For example, the first production effort related to most pieces of steel structure is to cut the piece out of a larger piece. That is also the most effi- cient point of construction to cut all of the holes which must be cut in that piece. However, in order to know where to cut all the holes, the detailed design and routing of every piece of piping, or ducting, or electrical cable which will fi- nally pass through that piece of steel must be complete.
The result of these many changes was a considerably larger engi- neering effort on this first project, compared to the "conventional" technique. However, the payoff was in the many fewer hours spent in production correcting the inter- ferences between the larger and the smaller sections of piping.
Another aspect of the design process is the need to identify all of the equipment which will be in- stalled on the ship right at the very beginning of the design pro- cess. In order to minimize the was- tage of time it is mandatory that we know precisely what pumps, what engines, what gear, etc., will be installed in the ship as soon as possible after the design effort begins.
The results to date have been very satisfying to Avondale's man- agement. Avondale's production manhours have been significantly reduced compared to the man- hours which would have been ex- pected had the ships been built in the "conventional" manner. The reduction in production manhours have much more than offset the increase in engineering manhours in this first effort to apply the new shipbuilding technique.
Needless to say, Avondale is not alone. Most other shipyards in this country are adopting the majority of these concepts in their building process today. So we can definitely say that the productivity of U.S. shipyards is improving.
Of course, production and engi- neering labor costs are not the whole cost story. Analyses of ship- building, whether in the U.S. or abroad, have demonstrated that approximately half of the cost of a commercial ship is in material.
Thus, even if we were to reduce manhours in half, we will still not be as competitive in the world market as we want to be until the material and equipment costs can be made competitive.
National Marine Names
Mangan Service Manager
Phillip S. Mangan
Phillip S. (Scott) Mangan has been named Service Manager of
National Marine Service Incorpo- rated's East Coast Operations. He will be headquartered at National
Marine's new diesel engine repair and parts facility, 4580 Village
Avenue, Norfolk, Va. 23502, and reports directly to the regional manager, Bill Dotson.
Mr. Mangan joined National
Marine in 1974 at its shipyard en- gine repair facility in Hartford, 111.
After an initial assignment as a mechanic, he was appointed to a lead foreman position, traveling worldwide on commercial and gov- ernment marine engine overhauls, troubleshootings and other re- pairs. He will be responsible for all service work/repair crews assigned to the Norfolk facility and operat- ing at the shop or at job locations along the East Coast and overseas.
National Marine Service, one of the Nicor basic energy companies, is a leading supplier of liquid bulk transportation services on the
Mississippi River system and Gulf
Coast. The company's shipyards at
Hartford, 111. and Harvey, La., of- fer full-service facilities for barge and towboat repairs. Its diesel en- gine repair services are widely rec- ognized in the United States; its repair crew services the needs of customers in all parts of the world.
Fetterolf Acquires
Stacey Valve Products —Literature Available
Fetterolf Corporation of Skip- pack, Pa., has acquired the Stacey
Value product line, and is cur- rently manufacturing and market- ing Stacey® Line Blinds on a worldwide basis.
J.W. Williams, president of Fet- terolf Corporation, stated in an in- terview: "Up until now, our en- deavors have been concentrated in severe service/lethal gas applica- tions. Now, with the Stacey prod- uct line, we have the products to meet the requirements of the all important Maritime Industry."
Proven Stacey Line Blind Valves provide positive, dead-tight shut- off of liquids, gasses or slurries in standard piping from 1 inch through 36 inches. Other sizes can be custom made to meet any spec- ification. The Line Blind Valves are available in all ASNI pressure ratings in a wide variety of sizes and body materials for service temperatures from cryogenic to 1400° F. Fetterolf has unique coating technologies to allow the valves to perform in the most se- vere salt water environments.
In addition to dead-tight shutoff,
Stacey Line Blinds are easily op- erated. Mr. Williams states: "With the Stacey, one man can position a blind in a matter of minutes. It usually takes three men up to an hour. Even at a distance, a glance is all it takes to determine whether a Stacey valve is open or closed.
This is another important safety feature. Safety is finally easy."
For additional information on
Stacey/Fetterolf valves,
Write 24 on Reader Service Card
North Florida Shipyard
Acquires Floating Drydock
North Florida Shipyard at Com- modore's Point in Jacksonville has acquired a floating drydock to ac- commodate vessels to 475 feet long and 68 foot beam. The drydock has a lift capacity of 6,500 tons; a length of 448 feet; width of 97 feet and a draft of 16 feet.
Exclusive representative for the shipyard is Richard F. O'Boyle,
Inc., New York, N.Y.
Charles Hall Appointed
Sales Manager-Marketing
Development For Petromar
Charles LeBlanc, chairman and president of Petromar Corpora- tion, Rockport, Texas, has an- nounced that Charles Hall has been appointed to the newly cre- ated corporate position of sales manager-marketing development. "Charles Hall brings a vast amount of marketing, business de- velopment and general opera- tional planning experience to our company," Mr. LeBlanc said. "He will assist us in the growth and expansion of the firm."
Mr. Hall, recently affiliated with
Halter Marine, Inc., of New Orle- ans in marketing and sales, has an extensive marketing back- ground in both domestic and inter- national fields of marine ship- building. He is a member of The
Society of Naval Architects and
Marine Engineers, and the Marine
Technology Society. He will be based in Petromar's corporate headquarters in Rockport.
Petromar operates a fleet of anchor-handling tug/supply ves- sels in the North Sea, Southeast
Asia, West Africa and the Middle
East. 40 Maritime Reporter/Engineering News