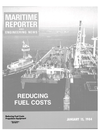
Page 19: of Maritime Reporter Magazine (January 15, 1984)
Read this page in Pdf, Flash or Html5 edition of January 15, 1984 Maritime Reporter Magazine
claiming their engines are capable of burning the lower quality fuels boast of their special cooling fea- tures, especially relative to ex- haust valves and seats. Sulfur at- tack of cylinder walls also seems to have succumbed to a commonly accepted remedy—insuring that cylinder wall temperatures are high enough to prevent sulfuric acid condensation and/or using suffi- ciently alkaline cylinder oils to neutralize the acid deposits on the cylinder walls. Obviously, if an en- gine manufacturer is designing an engine for a market intending to use a high-quality fuel, such as gas oil, it is not necessary to take these measures to insure engine compatibility with the vanadium and sulfur.
In addition to vanadium and sulfur, other fuel properties or constituents have a bearing on the operation of diesel engines. Some of these other properties or con- stituents are viscosity, density,
Conradson carbon residue, asphal- thenes, water content, ash, cata- lytic fines, and cetane number. Al- though some engines are more tolerant than others to fuel prop- erties and/or contaminant varia- tions, no engine is totally immune from highly degraded fuels.
The ingenuity of the modern- day diesel engine designer is fur- ther exemplified by the develop- ment and perfection of the super- long-stroke engines. These en- gines have not only resulted in relatively low crankshaft rpm's compatible with propellers of large dry bulk carriers and tankers but have resulted in thermal efficien- cies heretofore unattainable in a thermo-mechanical energy conver- sion device—thermal efficiencies greater than 50 percent. Nicolas
Carnot would have been proud of the modern diesel designer.
One casualty of the very high ef- ficiency of super-long-stroke en- gines is a relatively low amount of usable heat in the exhaust gases.
The very efficient expansion of the cylinder gases results in low ex- haust gas temperature, which in turn results in low exhaust gas en- ergy availability thereby reducing the amount and/or conditions of the waste heat produced steam.
Manufacturers of four stroke cycle, medium/and high-speed engines have concentrated on improving engine volumetric efficienty and air-fuel mixing as the primary means of improving engine efficiency.
Design improvements of modern marine diesel engines go beyond thermodynamic cycle advances and into the realm of engine mainte- nance. The use of hydraulic de- vices for pre-tensioning of bolts, studs, and tie-rods, as well as cus- tom rigging devices for easy han- dling of heavy components, are commonplace. Advanced designs of cylinder heads to include valve cages, which simplifies valve maintenance, are commonplace on four stroke cycle engines and two stroke cycle engines using uniflow scavenging, especially on those en-
January 15, 1984 gines designed to burn the lower quality fuels.
The responsibility for a well op- erating diesel vessel does not rest solely with the engine manufac- turer but must be shared with the ship designer, the onboard opera- tors, and the ashore support effort.
The design marine engineer re- sponsible for the systems design must pay close attention to the vessel's intended operating mode and expected available fuel. On board systems should be engi- neered with sufficient margins to allow for service growth as well as the expected and unexpected that the future holds in store. One sys- tem in particular that design ma- rine engineers should be liberal in defining system specifications is the fuel oil conditioning system.
Equipment selected should not be expected to operate at the extrem- ity of its operating range at design power. A liberal equipment selec- tion policy might be slightly more expensive initially but most likely will result in lower life-cycle costs for the vessel.
Once the ship is designed, the fate of its machinery is mainly de- pendent on the operating crews (continued on page 22)
Circle 179 on Reader Service Card 21
We'll match our ship repair people and our shipyard against anybody. Anywhere. Anytime.
We've Got ^
The Facilities:
A 300,000 square foot ma- chine shop, a foundry that can pour practically any marine casting we need with very short turnaround, an unpar- alleled steel fabrication center, a complete materials testing laboratory, a world famous school for training our own code welders.
We have been serving the shipbuilding and ship repair industry for nearly a century.
It's our life. It explains our en- viable record of fast turnaround ...our quality workmanship, our competitive prices. It explains why so many ship owners and operators rate Newport News number one.
Newport News Shipbuilding.
Newport News, Virginia 23607. (804) 380-2600/Telex 82-3453
TWX 710-880-0007.
Newport News .T„,„cpn, r .... LTENNECOJ
Shipbuilding
A Tenneco Company
Newport News
Shipbuilding is the world's largest, most diversified yard... the most experienced.
We've Got The Space: 8 piers for berthing ships to 1200 feet, drydocks from 650 to 1600 feet. We can dock fully loaded container ships, jumboize tankers, renovate or repair every aspect of any ves- sel... cruise ship, tanker, prod- uct carrier, or specialty cargo.
We've Got The
People: 24,000 skilled men and women.