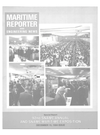
Page 33: of Maritime Reporter Magazine (December 15, 1984)
Read this page in Pdf, Flash or Html5 edition of December 15, 1984 Maritime Reporter Magazine
Artist's rendering of new bulk loadout facility designed and engineered by Soros Associates that will be constructed by Port of Corpus Christi (Texas) Authority. • _ . . .. SnMSSfcT
Corpus Christi Bulk-Loading
Facility To Be Modernized
By Col. Nolan C. Rhodes, USA (Ret.) and Richard W. Vander Laan
The Port Commission of the Port of Corpus Christi (Texas) Authority recently approved funds for mod- ernization of its existing bulk mate- rials dock. The existing facility in- cludes a bucket type unloader that is also used for loading vessels call- ing at the port. The Port Commis- sion recognized that a more efficient loadout system would better serve the present users of the facility as well as prospective users.
The Commission retained Soros
Associates, a New York-based inter- national consulting engineering firm specializing in the planning, design, and construction management of ports, offshore terminals, and bulk material-handling systems, to pro- vide the engineering and construc- tion supervision for the moderniza- tion program. Soros, working closely with the Port's staff, developed var- ious concepts that considered means to reduce ship turnaround time, in- crease operating efficiency, and con- struct a new loadout facility without disrupting the present operations.
The concept selected provides for a new loadout facility to be located west of the existing unloading dock.
A new berth able to accommodate vessels ranging from 1,500-ton barges to 100,000-dwt ships will be constructed with three breasting dolphins and two mooring dolphins along the length of the channel. A radial type Sumitomo shiploader, mounted on a curved rail in front and turntable in the rear, will have the capability to move along the length of a vessel at berth, as well as raise, lower, and shuttle the boom conveyor in and out from the bulk-
Col. Rhodes is director of engi- neering services for the Port of
Corpus Christi Authority; Mr.
Vander Laan is vice president of Soros Associates.
Dust collection during the ship- loading operation is in two modes.
In the first mode, the loading spout, inside a flexible concentric air duct, is lowered into the ship's hold with the discharge end of the spout and the air duct located in close proxim- ity to the discharged material. The dust-laden air generated at the dis- charge is drawn into the duct at approximately one-half (17,500 cfm) of the rated capacity of the dust-collection system. The spout and duct are raised simultaneously as the material is discharged into the ship's hold.
In the second mode, a trimming spoon located at the discharge end of the spout is used to throw materi- al under the vessel's hatch coam- ings. This operation generates more dust. Therefore, the dust is con- tained in the hold by strip tarps, and is exhausted from the hold through the concentric duct that is raised independently of the spout and spoon and positioned over the openings in the tarps. In this mode, the full air volume of the system (35,000 cfm) is utilized to capture the airborne dust in the hold.
This type of shiploader dust-col- lection system was also designed by
Soros Associates for the new shi- ploader at the Port of Houston, as well as at Arco Petroleum Products
Company's coke-loading facility at the Port of Longview, Wash.
The Port of Corpus Christi recog- nized the need to expand the new facility in the future without having to shut down the operation. There- fore, the design incorporates space for additional conveyor transfers for both inbound cargoes from rail and truck and outbound cargoes from areas on the site designated for future storage.
Contracts for construction of the new facility were awarded recently to the following contractors: dredg- ing, Lloyd W. Richardson Construc- tion Corporation, Arkansas Pass,
Texas; shiploader, Sumitomo Heavy
Industries Ltd., Japan; mechanical/ electrical, SCE Incorporated, Bir- mingham, Ala.; and civil/marine,
Paragon Engineers and Construc- tors, Inc., Houston.
The Corpus Christi facility is scheduled for start-up during the last quarter of 1985. head line. These shiploader move- ments will permit loading of most vessels without the need to move the ship at the berth.
The shiploader will be fed by a 48-inch-wide belt conveyor system designed to handle 1,500 tons per hours of material weighing 55 pounds per cubic foot. The conveyor system will be fed at multiple points along its length—at two points in the existing stockpile area and at a combination truck/railroad car dumping pit located adjacent to the existing railroad yard.
The pit dump, enclosed in a building, can accommodate a 100- ton, bottom-dump railroad car or three 20-ton trucks that rear-dump through openings in the side of the building. These openings will be closed with overhead doors when dumping from railroad cars. An overhead type, trolley-mounted railroad car shakeout will be pro- vided to speed up railcar unloading.
Material discharged into the dump hopper is fed onto the belt conveyor system by four variable-rate, vibrat- ing pan feeders located under the openings in the bottom of the hop- pers. The belt conveyor system will be protected from damage by tramp iron by a suspended magnet and a metal detector. An in-motion belt scale to record tonnage loaded into ships will be provided to assist in the shiploading operation.
In order to meet the standards of the Texas Air Control Board, the facility will be constructed with a dual dust control system. This sys- tem will consist of dust suppression for bulk materials such as coal and petroleum coke that can be sprayed with water, and containment for bulk materials that cannot be sprayed with water. All conveyor transfers will be fully enclosed, and all ground conveyors will be pro- vided with hood covers. Return belt scrapers and plows will be designed and installed to minimize any carry- back of material on the return strand of the belt.
SSMHH ©
FRED DEVINE
DIVING & SALVAGE, INC.
Marine Salvage*Harbor Clearance*
Wreck Removal*Pollution Control-
Diving Services-Ocean Engineering-
Fire Fighting-Tanker Lightering-
Ocean Outfalls-Flyaway Salvage Crews-
Anchor & Chain Recovery
Write for full capability information and specifications on the
SALVAGE CHIEF, the finest salvage ship afloat.
DEVINE
DIVING & SALVAGE, INC.
Headquarters 6211 N. Ensign, Portland, OR 97217 (503) 283-5285
Telex 36-0994 DEVINESALV
Quick, effective response to any marine casualty worldwide. —_ w..., ' - • < '-ft v*
A-
Circle 128 on Reader Service Card
December 15, 1984 35 1