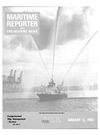
Page 28: of Maritime Reporter Magazine (January 15, 1985)
Read this page in Pdf, Flash or Html5 edition of January 15, 1985 Maritime Reporter Magazine
REDUCING FUEL COSTS
Diesel Engine Manufacturers
Continue To Improve The Fuel
Efficiency Of Their Engines
As we enter 1985, marine power plant designers continue the general practice that became common in the 1970's, that is the practice of design- ing power plants for high thermal efficiency. Low fuel consumption, over a wide range of operating pow- ers, became and continues to be of paramount importance. The prac- tice of designing for high thermal efficiency resulted in the nearly uni- versal use of diesel prime movers for main propulsion. During this transi- tion period, a period of approxi- mately one decade, the marine com- munity experienced a significant degradation of fuel oil quality which caused a level of trepidation relative to choosing internal combustion en- gines such as the diesel engine. As a result of aggressive research and de- sign efforts undertaken by the en- gine manufacturer, prudent deci- sions concerning fuel selection by the operators, and advances in ship- board fuel treatment techniques, the modern diesel-powered mer- chant ships are very capable of oper- ating economically on available ma- rine fuels. During the decade, the engine manufacturer even suc- ceeded in significantly reducing en- gine specific fuel consumption as demonstrated by the long stroke en- gines.
It appears marine engineering de- sign efforts in the near future will continue the trend to convert the maximum amounts of the available energy in the fuel to usable energy.
Marine engineers will continue to adopt the most efficient engines available to the industry and will develop system designs that will re- sult in overall fuel consumption at such low levels that they nearly cut in half the levels common in the
U.S. merchant fleet prior to 1973.
These systems will probably incor- porate multi-pressure waste-heat steam generators, induction tur- bines for driving the ship service generator and jacket water moti- vated auxiliaries such as distilling units and absorption type air condi- tioning systems. Although the re- cent stabilization, and lowering of marine fuel oil prices have reduced the immediate incentive for design- ing power plants for ultra-low fuel consumption, the industry has been forcibly conditioned to accept power plants with the lowest possible over- all fuel consumption. Owners know that low fuel consumption normally converts to lower required freight rates and will continue purchasing vessels with the lowest possible an- nual fuel costs.
Concurrent with the operator's 30 desire to keep overall fuel consump- tion to a minimum there exists the requirement to maintain high equipment reliability and system availability. High equipment reli- ability and system availability de- pend on two critically important cri- teria; sound design and intelligent operation. Sound design involves in- dividual system components and system integration of the required components. Marine engineers need to augment conventional design considerations (thermal, fluid, ma- terial, strength requirements, etc.) by reliability and value engineering analyses in order to better serve the needs of the owner. Weak links in marine systems must be eliminated by improving specific component designs or eliminating components when appropriate. The design ma- rine engineer must continually con- sider the shipboard environment— which includes the vessel, the sea and the crew—when developing the design. Intelligent operation in- cludes basing normal operating de- cisions on sound engineering princi- ples and thorough knowledge of components and systems. To achieve intelligent operation of modern power plants designed for minimum fuel consumption the owner must insure that pertinent technical information is aboard each vessel and that the crews under- stand how to use the technical infor- mation to optimize the plant's oper- ation.
For an owner to optimize his op- eration it is not enough to specify a vessel design with ultra-low fuel consumption, but it will be neces- sary to insure that the vessel is attended to properly. The ashore personnel's responsibility centers around supporting the sea-going personnel in achieving maximum fuel efficiency. Ashore personnel must analyze all suggestions thor- oughly before making a decision to implement or not. Remember, not implementing a suggestion may re- sult in reduced present expendi- tures but it may also eliminate long term savings. Another responsibility is to foster a climate of high techni- cal awareness. It is only through sound technical awareness that operators can adapt to changing technical and operation require- ments. A few thousand dollars spent on honing a chief engineer's techni- cal skills may manifest itself as an annual fuel savings worth many times more. The prevention of the degradation of a plant's efficiency of a mere one percent, may save an owner $50,000 in annual fuel costs, let alone the potential maintenance costs resulting from poor operating practices.
The following is a compendium of the state-of-the-art components and systems available for powering mod- ern vessels with reduced fuel costs.
ALCO POWER
Circle 1 on Reader Service Card
Alco Power Inc. is currently in- volved in a project that will add increased fuel efficiency to its model 251 diesel engine, as well as de- crease the amount of time re- quired to achieve rated horse- power and speed from engine idle speed. This is accomplished by the application of the model 131 tur- bocharger on the Alco 16-cylinder, model 251 CE diesel engine. This is now being tested in towboat ser- vice on the lower Mississippi and is receiving very favorable results.
Alco is also involved with the development of a new piston de- sign to further increase fuel effi- ciency over its current valve-pock- eted design. Although this is in its preliminary stages, Alco hopes to have it out in the marketplace shortly.
Other developments on the ho- rizon include continued experi- mentation with heavy fuels, cam- shaft design changes, and experimentation with turbochar- ger application, all of which will add up to increased fuel efficiency.
B&W ALPHA
Circle 2 on Reader Service Card
B&W Alpha Diesel A/S of Fred- erikshavn, Denmark, is a com- pany of the M.A.N.-B&W Group that designs, manufactures, mar- kets, and services complete vessel propulsion systems. Last year the company completed the integra- tion of the in-line and V version of the 20/27 M.A.N.-B&W diesel en- gine and the in-line version of the 32/36 M.A.N.-B&W engine with existing Alpha controllable-pitch propellers and gearboxes. This has resulted in four-cycle diesel pro- pulsion systems developing as lit- tle as 680 bhp at 1,000 rpm, which can burn heavy fuel oil up to 2,100 sec. Redwood 1 at 100 F.
A new series being offered is the 20/27-VO propulsion system. While the engine itself is not new, the system incorporates the new Al- phatronic I and Alphatronic II— the company's latest electronic re- mote control systems.
BERGEN DIESEL
Circle 3 on Reader Service Card
A.S. Bergens Mekaniske Verk- steder (Bergen Diesel) of Norway has used heavy fuel in its engines for more than 20 years and has very solid experience in this field.
Some 500 engines, both propulsion and generator sets, are in opera- tion on heavy fuel, with the long- est running times in excess of 100,000 hours. The company's U.S. subsidiary, Bergen Diesel, Inc., is located in Kenner (New Orleans), La.
The thermal efficiency of Bergen
Diesel's K-range of engines is as high as today's state of the art will allow, giving a realistically low specific fuel consumption over a wide load range. Furthermore, the
K-type engine is the product of more than 20 years of heavy fuel operation experience, and is thus capable of burning low-grade, high- viscosity heavy fuels while main- taining extremely long component overhaul intervals and component life.
To be able to operate vessels at or near the point of optimum fuel efficiency, Bergen Diesel has de- signed sophisticated engine sys- tems that have been put into suc- cessful operation. For fishing vessels, systems with high-output shaft generators, driven via two- speed gearboxes from engine front end power take-offs, allows the use of shaft generators at two engine speed modes, i.e., the free-running and the trawling speed, for inex- pensive, main-engine-generated electric power. Hybrid power sys- tems, being a combination of die- sel-electric and diesel-mechanical power transmission to the propel- lers, give offshore supply and an- chor-handling vessel operators the possibility to utilize the advan- tages of both systems.
CATERPILLAR
Circle 4 on Reader Service Card
Caterpillar 3500 Series marine engines have set new standards for fuel savings—savings that can actually allow repower with full payback in less than IV2 years.
Fuel savings may in fact exceed 35 percent at all operating loads, not just within a limited range or at "rated" load.
Designed for tighter oil control than two-cycle engines and most four-cycle engines, the 3500s can save several thousand dollars a year in lube oil costs alone.
For simplified maintenance, front-mounted governor and side- mounted oil, water, and fuel trans- fer pumps improve accessibility.
Fuel filters, oil, and oil filters can all be changed at the same time.
Access covers near the camshaft and in the crankcase allows sim- ple and effective visual inspection.
These and other 3500 Series de- sign features translate into less
Maritime Reporter/Engineering News