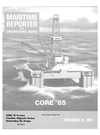
Page 30: of Maritime Reporter Magazine (September 15, 1985)
Read this page in Pdf, Flash or Html5 edition of September 15, 1985 Maritime Reporter Magazine
PROPULSION UPDATE
CGCO engineers in front of test units while the "load" is held at 115 percent of rate power
Cincinnati Gear Completes Testing
Of New, Sophisticated Marine Drive
For Navy T-AO 187 Class Oilers
Last month the Cincinnati Gear
Company successfully completed back-to-back full-load testing of a sophisticated new marine drive for the U.S. Navy's new T-AO 187 class of fleet oilers. These ships, powered by two Colt-Pielstick PC4, 16, 272- hp diesel engines, represent a giant technological step forward for the
Navy. The essential elements in the new T-AO gearboxes are the carbu- rized, hardened and precision ground (CHG) gears having a high- power density. CGCO, under con- tract to provide these main pro- pulsion gearboxes, stated they de- veloped a cost-effective, high-per- formance drive package that is stronger, quieter, and 35 percent smaller than a conventional design using through-hardened gears.
CGCO's high-performance ma- rine facility, Plant III, is utilized to manufacture and test these types of products.
Weighing 23 tons, the surface- hardened bull gear is the largest designed and manufactured in the free world. The T-AO back-to-back test stand is the seventh and largest facility of this kind that Cincinnati
Gear has designed, built and oper- ated. CGCO is the first U.S. compa- ny to offer back-to-back testing in this size range.
Incorporated into each gearbox are unique features, such as single helical coarse pitcb surface-hard- ened gearing, thrust collars for axial load canceling, integral PTO, three- point mount configuration, and an input quill shaft for main reduction pinion isolation.
The full-load, back-to-back test arrangement had the port and star- board units mounted with the input and the output shaft flanges facing each other and connected with ap- propriate couplings. The input cou- pling system incorporated a torque meter in the input quill shaft isola- tion system to monitor applied torque. The output flanges sup- ported, and were connected by, a large custom-designed hydraulic torque applier.
Final visual inspection of "power loop" before placing covers into place.
The "load loop" was accelerated to speed by a 1,000-hp variable speed motor driving the PTO shaft flange of the port unit. This motor was sized to overcome gear mesh and journal bearing power losses.
With these key elements in place, virtually any power/speed combina- tion within the design envelope could be simulated. The tests have established basic performance pa- rameters while the units were sub- jected to a closely simulated ship- board operating environment in terms of torque, speed and mount- ing arrangements.
The hydraulic load cell in this test stand in capable of applying loads in excess of 13,000,000 lb.in. torque and 25,000 horsepower. For the T-
AO test the unit operated for 25 hours at 100 percent of rated power and speed—16,272 hp at 95 rpm with 900,000 lb.ft. of torque. To demonstrate adequate design mar- gins, the unit was operated at 115 percent of rated power. This back- to-back full-load test confirmed that the units meet given specifica- tions at rated power and speed.
Full face contact of the main pin- ion/bull gear mesh was verified by dynamic strain gage measurements of a series of bull gear teeth while the test unit ran at rated power and speed. Comparison of variations in peak strain gage measurements of the bull gear teeth verified the accu- racy and correctness of the input pinion/bull gear longitudinal and profile corrections. These measure- ments confirmed that blueprint- specified tooth corrections are ade- quate to insure a uniform load dis- tribution and allow evaluation rela- tive to current ABS gearing derating factors.
The thrust collar concept demon- strated and proved the effectiveness of canceling the axial force directly at the single helical gear mesh.
Loaded thrust collar surfaces were inspected by visually comparing documented static collar pattern/ surface finish before testing and col- lar surface finish after testing.
Airborne and structureborne noise measurements taken through- out the test established a baseline data point for future large, coarse pitch, single helical, main reduction gears.
A post teardown inspection at the conclusion of the test program on both the starboard and port units provided engineering/quality assur- ance data of all gears, bearings, and thrust cones. The units were subse- quently reassembled to production configuration, packaged, and shipped.
To the military there are obvious benefits of carburized, hardened and precision ground (CHG) marine gears for applications which are sen- sitive to noise generation and/or de- tection. Currently there is a growing interest in CHG gears from engi- neers with commercial marine and other industrial applications look- ing for ways to better utilize space in a cost effective package.
For complete free literature on
Cincinnati Gear Company equip- ment,
Circle 63 on Reader Service Card
New Alarm Reduces Boiler Failures,
Diesel Failures And Repair Costs —Free Brochure Available
Since nearly the beginning of shipboard and power station boiler use, little thought or consideration has been given to boiler protection from oily condensate return caused by seal failure from the turbines.
The U.S. Navy, to protect their boilers, used double-walled boiler tubes. The weight increase, how- ever, caused weight problems in the submarine fleet. In addition, initial cost of manufacturing was much higher than for standard systems.
Where the steam pressure is higher than the lubrication pressure, no problem exists until routine boiler shutdown, then leakage may occur and is not discovered until boiler tube failure from lack of heat trans- fer.
Biospherics Incorporated, Rock- ville, Md., has now developed a self- cleaning, on-line, oil-in-water alarm which can withstand temperatures up to 250° F. This unit, placed directly into the condensate return lines, will alarm and trigger switch closure on as little as 2ppm oil-in- water, thus saving the boiler acci- dental damage.
In addition, damage to diesel en- gine cylinder walls is often due to "hot spots" created by oily deposits caused by seal or gasket failure, allowing lubrication oil to enter the cooling jackets and act as an insula- tor. The BA-200 HT, introduced by
Biospherics, is said to be ideal for diesel protection, and is already in- stalled on the diesel engines of the
Canadian Coast Guard's Ice Break- ers. The unit is unaffected by com- mon coolant additives. Although this model is a commercial one, it was found to be able to withstand the continuous shock and vibration of the Bombardier engines used in this class of vessel.
Shipowners and diesel engine manufacturers interested in obtain- ing further information on this "inexpensive insurance policy," should
Circle 62 on Reader Service Card 34 Maritime Reporter/Engineering News