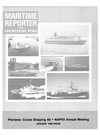
Page 41: of Maritime Reporter Magazine (January 1988)
Read this page in Pdf, Flash or Html5 edition of January 1988 Maritime Reporter Magazine
Repowering The QE2 (continued) burning 700 est heavy fuels.
Each engine is directly resilient mounted on the ship's foundation and flexibly coupled via Vulkan-
Rato couplings to two-bearing total- ly enclosed, water-cooled, salient pole, three-phase, synchronous
GEC alternators, each rated 10.5
MW, 10 kV, 60 Hz. Each alternator is rigidly mounted on the ship's foundation.
The power generated is supplied to a common 10-kV busbar system divided into two separate GEC main switchboards, installed in two sepa- rate compartments. Each of the main switchboards is again sub- divided in two bus-sections allowing a variety of operating modes.
This common busbar supplies power at 10 kV directly to the two
GEC 44-MW, 60-Hz synchronous motors running at 144 rpm. These motors are among the largest ever supplied for a marine propulsion plant, each weighing 340 tons with a length of 5.5 meters and a width of 8.5 meters. Electric power to all ship and domestic consumers are also supplied from the common busbar via two GEC liquid-cooled 10 kV/3.3 kV transformers of 11 MVA capac- ity each. With this arrangement a redundancy of 100 percent is avail- able for the ship's load.
To allow the ship to operate a high efficiency even at low speed and during maneuvering, the nor- mal constant propeller speed of 144 rpm can be reduced to 72 rpm. This is achieved by two GEC synchro converters of 11 MW each. These converters are also used for starting and speeding up the synchronous motors. The driving power of the synchronous motors is transmitted via a new twin shaft arrangement to two new 5.8-meter-diameter Lips five-bladed CP propellers.
Optimized Auxiliary Systems
For the operation of this power plant, optimized auxiliary systems were installed. All engines per en- gine room have a common central cooling system. For example, two separate, independent central cool- ing systems were provided. This ar- rangement allows the heat to be dis- sipated from the engine jacket water and charge-air cooling to be utilized.
This is accomplished by having two
Serck (four in total) freshwater gen- erators per engine room. This waste heat produces 250 tons/day fresh water per unit or 1,000 tons/day total.
At lower ship's speed, with a re- duced number of engines in opera- tion or at partial loads, the lack of waste heat supplied to the cooling system can be compensated for by one steam-heated booster heater per unit. This means that the total freshwater requirement can still be produced at sea.
The central cooling system is de- signed for 32 °C seawater tempera- ture and the low temperature circuit for 38°C. For each cooling system there are three two-speed seawater pumps, each with 50 percent of rated capacity. This arrangement,
January, 1988 combined with the Engard pump control system from Alfa Laval, pro- vides huge energy saving potential.
This is possible because the sea- water quanity varies in a wide range depending on the seawater tempera- ture, the total engine load and the degree of waste heat recovered.
With this system, the capacity of seawater required can be matched optimally with the demand.
Similar to the cooling system, the fuel systems are also split into two separate systems, one per engine room. These two fuel supply sys- tems are designed to accommodate
CIMAC K55 fuels with a viscosity up to 700 est. The systems operate with fuel pressures of six to eight bar and a final fuel temperature before engine of 147°C.
Each engine has its own separate lube oil supply and treatment sys- tem with electrically driven lube oil pumps.
To meet the noise criteria, an exhaust gas system with three
Huss silencers per engine was sup- plied. Each exhaust gas system is equipped with a Sunrod exhaust gas boiler to use the exhaust gas ener-gy-
The completion of the complex conversion, the largest ever under- taken by a German yard, by Lloyd
Werft of Bremerhaven marked the culmination of a unique human and technical achievement and the be- (continued)
THREE IMA BUSINESS REPORTS AVAILABLE
International Maritime Associates, Inc. (IMA) special business reports will help keep you informed of developments in the marine business. More than 410 companies are among our subscribers. They include most of the major firms in the marine industry.
Report No. 7107 Projected U.S. Marine Market: 1987-1991
A 200+ page report covering each of 20 market segments. These segments include coastal tankers, specialty ships, ferries, offshore rigs, naval ships, Army craft... The report examines current business conditions, potential developments, future construction and main- tenance demand and projected equipment requirements. Key points of buying control, buy American rules and likely competitors are iden- tified. $350.00 per copy. *****
Report No. 7103 U.S. Navy Ship and Equipment Procurement
Quarterly series monitoring spending projections, contract oppor- tunities, contract awards and business contacts in this $34 billion annual market. Most current quarterly report issued in October 1987. $380.00 for series of four quarterly reports
Report No. 7104 U.S. Navy Ship Maintenance & Modernization
Quarterly series covering ship maintenance schedules, contract awards, future spending and business contacts in this $6 billion annual market. Most current quarterly report issued in November 1987. $380.00 for series of four quarterly reports
To order please cafl or write:
International Maritime Associates, Inc.— 835 New Hampshire Ave., N.W.
Washington, DC 20037
Telephone: (202) 333-8501—Telex: 64325 IMA—Telefax: (202) 333-8504.
Circle 136 on Reader Service Card 53