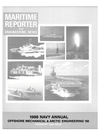
Page 21: of Maritime Reporter Magazine (February 1988)
Read this page in Pdf, Flash or Html5 edition of February 1988 Maritime Reporter Magazine
thickness of approximately 0.75 mils, and will provide corrosion re- sistance without topcoating for about one year. Jotun Valspar zinc coatings have had extensive marine service, with applications on exteri- or hull topsides, deck and cargo tanks of vessels.
A recent innovation is the intro- duction of Vepok, a unique group of protective coatings that can be ap- plied over oily, wet, rusty surfaces.
Jotun Valspar is a complete sup- plier of coatings to the marine in- dustry, and therefore in addition to the above mentioned coatings, also manufactures and provides anti- fouling points and specification coatings that are used by govern- ment agencies, including the U.S.
Navy.
PHILADELPHIA RESINS
Circle 56 on Reader Service Card
Three new materials called Super
Repair Products have been formu- lated by Philadelphia Resins, Mont- gomeryville, Pa., to resist abrasion, impact, cavitation and corrosion at elevated temperatures and in ad- verse environments. Developed es- pecially for high-temperature, high- friction aerospace, marine and in- dustrial applications, these easy-to- use materials include an alloy paste, a ceramic repair liquid and a ceram- ic repair putty.
Phillybond® Super Alloy is a tita- nium-based compound, used to re- condition compressor housings, pro- pulsion shafting, valve bodies and other equipment which must oper- ate in adverse environments with temperatures between —100° to 500° F. In addition to permanently repairing and protecting marine, in- dustrial and aircraft components made from steel, aluminum, brass, carbides, zinc and zinc alloys, this new compound bonds dissimilar metals without galvanic corrosion problems. After curing for 18 hours at 72°F, it may be machined and finished with standard metalwork- ing equipment.
Phillybond® Ceramic Repair Put- ty and Phillybond® Ceramic Repair
Liquid are specialty repair com- pounds, developed for coating, lin- ing and protecting pump casings, valves and other new or worn equip- ment subjected to friction, corro- sion/erosion and cavitation. With convenient, long-term repairs of worn metal surfaces on-site, the brushable liquid and the nonsagging trowelable putty reduce downtime in repairing vital machinery. Their useful thermal envelope is also -100° to 500°F.
No heat, pressure or special tools are needed to create an integral bond between the titanium-based, machinable repair compound (or the severe-service ceramic liquid or putty) and new or worn equipment.
The company reports abrasion re- sistance, per ASTM D406, is five times better than competitive prod- ucts.
PRC
Circle 22 on Reader Service Card
More than one million square feet
Circle 252 on Reader Service Card of Proreco® deck coating systems have been applied to exterior decks of small boats, large commercial ships, towboats, offshore rigs and military ships. Manufactured by
Products Research & Chemical Cor- poration (PRC) of Glendale, Calif., the interior and exterior Proreco® coating systems are fire-retardant, resistant to acids, caustic chemicals and petroleum products.
Proreco® III exterior coating sys- tems are used to virtually eliminate costly maintenance and down-time for working ships. The PRC Prore- co® III coating systems are specified by many naval architects and speci- fied by the military due to its known track record for corrosion control, dependability and long wear.
Proven to be the most effective, the Proreco® III coating systems have an inherent flexibility to with- stand normal stress caused by deck movement. The fire-retardant sys- tems provide the ultimate in corro- sion control and are resistant to the heaviest abrasion and impact. The advantages of the Proreco® III sys- tems over rigid coatings is the Pror- eco® elastomeric base which is not brittle and not subject to cracking, chipping or spralling.
The Proreco® I coating system is specified for habitability areas such as heads, galleys and mess decks.
Proreco® I proves itself again and (continued) • I %om ships to shore
I a stations to trans- it portable shelter
JL installations, one
Ife -II iiliBniiTl^t rece'ver has become the
B I^KSSmSh Jl Davy's designated re- \ JBa*» »»"BSE-— placement for a variety
I of aging radios. The
R-2368/URR from Harris
RF Communications.
This high-performance VLF/LF/MF/HFISB receiver employs microprocessor technology that makes the
R-2368 a snap to use. It operates from 14 kHz to 30 MHz in one Hz increments. And its rapid tune time and internal scan capabilities make the R-2368 perfect for surveillance and other applications requiring flexi- bility and adaptability.
Already, the R-2368 is the official replacement radio of Naval Commands. For ship and shore applications, it replaces the AN/WRR-3 VLF, AN/SRR-19 LF, R-390 and R-1051 MF/HF receivers.
Now the R-2368 is available for your special needs.
The ones you face today. And thanks to the R-2368's state-of-the-art design, the ones you'll face in the future. Because when the message has to get through, you need Harris RF Communications.
HARRIS RF COMMUNICATIONS GROUP
Long Range Radio Division 1680 University Avenue, Rochester, NY 14610 (716) 244-5830 1-800-4-HARRIS, Ext. 3500