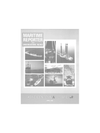
Page 59: of Maritime Reporter Magazine (April 1988)
Read this page in Pdf, Flash or Html5 edition of April 1988 Maritime Reporter Magazine
PROPULSION
UPDATE
Schaffran Offers Advanced,
Compact Controllable Pitch Propeller compactness and reduction of parts in the driving mechanism, which in fact contributes to reliability and easy assembly and servicing.
For free color literature on the
Schaffran Compact VK Controlla- ble Pitch Propeller and other pro- pulsion systems from the company,
Circle 36 on Reader Service Card
Bath To Build
Aegis Cruiser
For $226.1 Million
Bath Iron Works (BIW) Corpora- tion, Bath, Maine, has been awarded a $226.1-million Navy con- tract to build an Aegis guided-mis- sile cruiser (CG-47 Class). —Color Literature Available—
Since delivering their first con- trollable-pitch propeller (CPP) sys- tems to Menzer Werft for use aboard a new 22-knot police boat two decades ago, Schaffran Propel- ler Lehne & Co. GmbH & Co. KG,
Liibeck, West Germany, has been designing, developing and manufac- turing advanced and innovative
CPP systems for the worldwide ma- rine market.
One of the most innovative CPP designs offered by Schaffran is the
Compact Hub Type VK. Used in
Finnish winter shipping for several years, these Schaffran systems proved to be extraordinarily sturdy and reliable, even under the most severe ice conditions. One of the most recent ships to be fitted with a
Schaffran CPP system is the Thea
S. Built with an asymmetrical stern for fuel economy by the Heinreich
Brand yard in Oldenburg, she was fitted with a four-blade 4.5-meter
CP propeller.
The basis of this CPP system's design is the integral hub unit which is calculated and optimized in ac- cordance with finite-elements meth- ods. The blade base bearings as well as the servo-piston guide are con- tained in the component. Thus, pos- sible faults in the plane are avoided in the otherwise common plane parts, the maximum comparable stresses are reduced and distributed over the whole length of the hub, so that in an emergency, exceeding the yield point or even failure point can be avoided. From a hub diameter of 1,000 mm the servo-piston guide is housed in a separate hood construc- tion.
The thrust of the servo-piston is transferred directly to the crank arms of the fork-shaped variable flanges, via rigid arms of a flanged to crossbar, which enclose a highly load-bearing and impact resisting universal joint for each controllable pitch propeller blade. Thus, the thrust is directly transformed into the required blade spindle torque.
With this design, the servo-pis- ton, with its widely spaced guides at the piston skirt and at the piston rod guide, remains practically free of radial forces, so that the only fric- tion is in the universal joints and the blade base bearings.
The inherent low number of force-connected parts in the design of the propulsion components pro- vides for solid construction so that the whole servo power can be con- centrated on one single crank steer- ing, without stressing any part of this driving chain beyond its yield point.
The individual blades are fixed on the outside with high-tensile CrNi steel bolts. The inner blade base remains untouched when changing blades, so that in some cases even underwater blade replacement is possible.
With a maximum hydraulic oil pressure of only 20 bar, the life expectancy of the unit's complete hydraulic system is considerably in- creased.
In addition, as a safety precau- tion, in case of a sudden drop in hydraulic oil pressure, the existing pitch position is maintained for a longer period of time by an auto- matic blocking device with a hy- draulic valve in the servo-piston, closing immediately with a tight- fitting piston ring gasket.
For bridge remote control of pitch and rpm, fine pneumatic control valves for impulse and profile manometers for indication are pre- ferred. Pitch and speed can be regu- lated together or individually de- pending on the type of operation required.
The patented Schaffran CP Pro- peller VK represents an innovative development towards increased , UNIT OP GENE BIONAl
HENSCHEL
Digital Master
Clock System
The Henschel Digital Master
Clock System provides a syn- chronized display of time in various shipboard locations. The master clock displays both local time and Greenwich Mean Time (GMT).
This crystal controlled, microcomputer based master clock transmits multiplexed time (hours, minutes and seconds) and date (month, day and year) information to a maximum of 40 remote repeater clocks and/or data and bell loggers. l b 3 H 5
The remote repeater clocks display either local time or GMT in various mounting configurations to suit most appjications.
Time is continuously displayed on both the master and repeater clocks by red, 6 digit LED displays, easily viewed up to 25 feet away. The date is displayed on the master clock by use of a front panel switch. This calendar function is set to maintain the correct date for changes in month, day, year and leap year.
Battery back-up is provided to maintain both time and date in the master clock and in a few selected repeater clocks during any loss of input power.
Clock accuracy is maintained independent of the input power frequency by a self-contained crystal oscillator. Time and date are easily set by means of pushbuttons on the front panel. When changing time zones, hours may be changed independently of minutes and seconds so that time accuracy is not lost.
HENSCHEL
Henschel 9 Hoyt Drive
P.O. Box 30
Newburyport, Massachusetts 01950 U S A (617) 462-2400 Telex: (RCA) 294074
CP.Propeller Type VK Control Unit Type T Control Unit Type G
Circle 268 on Reader Service Card 59