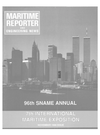
Page 85: of Maritime Reporter Magazine (November 1988)
Read this page in Pdf, Flash or Html5 edition of November 1988 Maritime Reporter Magazine
As new rules now on the drawing boards go into effect—probably within the next two years—opera- tors of barges carrying gasoline and other petroleum products will find it necessary to ensure that their ves- sels are vapor tight.
Oceangoing tankers for some years now have been required to keep cargoes of crude oil or oil prod- ucts hermetically sealed from the atmosphere and blanketed with a protective inert gas which does not contain enough oxygen to permit ignition. The rules now being pro- posed for barges used on inland waterways do not include the use of inert gas, but are designed rather to protect workers and the environ- ment from any emissions of hazard- ous or noxious fumes.
Various government agencies are included in promulgating the new directives. Principal among these is the U.S. Coast Guard's Chemical
Transportation Advisory Commit- tee (CTAC). This group is currently planning to issue an initial draft on hydrocarbon emissions in February 1989, with the Final Rule to follow around February 1990.
The Environmental Protection
Agencies of several states are also working on similar rules, which may in some cases be more stringent and may come into effect earlier than those of CTAC. These states include
New Jersey, California, and Louisia- na. It is estimated that in 1987, four trillion gallons of gasoline were shipped from New Jersey alone.
One of the problems which can be foreseen in the conversion of liquid- carrying barges to vapor-tightness is the reluctance of employees to ac- cept all of the changes in operating procedures that will be required.
Barge operators are for the most part trained on the job, and often by their own fathers and grandfathers.
This results in a great reverence for doing things "the way they've al- ways been done."
Other factors to be considered be- fore beginning the conversions in- clude the four important ways in which barges differ from river boats or oceangoing ships. These are: 1) barges are unpowered; 2) they are unmanned; 3) their tank bulkheads are of relatively low strength; and 4) they are often laid up with little or no maintenance availability.
Therefore, the converted barge must be designed to operate simply, reliably, with little pressure differ- ential between inside and outside, without any need for power, and— as much as possible—just as it was before being sealed.
November, 1988
The actual sealing up of the barge's tanks is a fairly straightfor- ward engineering task. Obviously, all outlets to the atmosphere must be sealed off in some manner. This requires merely the closing of all openings and the judicious selection and proper installation of the most suitable cargo venting system, over and under pressure protection and level monitoring and sampling sys- tem.
Because of the flammable nature of gasoline and the other "White
Products" covered by these regula- tions, proper grounding procedures must be followed at all points where static buildup might cause a spark.
The system should be designed so that incoming cargo forces vapor displacement, keeping the tank pressure slightly above that of the atmosphere. This will assure that any gas movement will be toward the outside of the tank, rather than risking air leakage to the inside so as to create a potentially explosive mixture.
It is important that vapor headers should be routed so that all vapors (or vapors plus liquid, in the event of an overfill) will be discharged into an overflow containment tank rath- er than into the atmosphere or the surrounding water. All shore con- nections should terminate in a de- tonation arrestor and a stop valve.
A more complicated decision to be made is that of selecting a meth- od of measuring the levels of the tank contents. Here the options pre- sent various degrees of complexity, and the goal must be to choose a reliable system which is not so com- plicated that it inspires resentment among the crew who must utilize it.
The most common method used today for determining the cargo lev- el as the barge is being filled is known as "counting the rungs"— which is a literal description of the process. The tankerman merely opens a hatch and observes how high the liquid has risen on the access ladder. CTAC and the state
EPAs are certain to take a dim view of the fire safety, operator working conditions, and environmental im- pact of this traditional mode of measurement.
Some acceptable systems, howev- er, are not too drastically different from rung counting.
One solution is to install a dual set of sight glasses in the hatch over the cargo tank. This allows the tankerman to "count rungs" as be- fore, but he is protected from the cargo vapors by a solid barrier. The dual glasses provide one for sighting and one for introducing light. Each port should have a wiper assembly to remove condensed vapors on the cargo side, and a cover should be used to protect the ports when not in use.
A second, more efficient measur- ing method is one in which a porta- ble, battery-operated electronic sen- sor is lowered through a sealed valve port on a measuring tape. The sen- sor produces different audible sig- nals when its tip is in contact with air, liquid hydrocarbon, or water. It can be introduced through valves as small as 1 inch in diameter up to 4 inches simply by selecting the prop- er fittings.
These systems—known as Her- metic UTI-GT (Ullage, Tempera- ture, Interface Detector—Gas
Tight)—are manufactured and dis- tributed by Tanksystem SA of
Bulle, Switzerland. The exclusive agent for the United States and
North America is American United (continued)
New Rules To Mandate
Sealing Of Barges
By John T. Lombard, Vice President,Sales,
American United Marine Corporation,
And Bruno Klaus, Managing Director, Tanksystem SA
Here'is how
SWAGELOK® Tube Fittings reduce costs in your hydraulic system
SWAGELOK Tube Fittings help you fight costs five ways by reducing your...
Hydraulic Fluid Index. Reliable containment at every connection stops leakage.
System Construction Time. Easy installation, with fewer connections throughout tne system, lets your fitters move fast.
System Test Time. Gageability assures sufficient pull-up, cutting time spent looking for leakers.
Maintenance Time. Re-makeability speeds component replacement.
Repair Costs. Resistance to hydraulic surges and vibration lowers the risk of blowout and fatigue failure.
SWAGELOK Tube Fittings are stocked by Authorized
Sales and Service Representatives...always available during construction, operation and overhaul of your system. •986 SWAGELOK Co all rights reserved C 81fa
TUBE FITTINGS
SWAGELOK Co.
Solon, Ohio 44139
SWAGELOK Canada Ltd., Ontario
Circle 34 on Reader Service Card 87