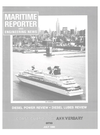
Page 55: of Maritime Reporter Magazine (July 1990)
Read this page in Pdf, Flash or Html5 edition of July 1990 Maritime Reporter Magazine
Marine Lubricants (continued) leased for removal by settling/cen- trifuge.
Corrosion is prevented by the filming action of the fuel condition- er. The additive also chemically neutralizes acids in the fuel.
Where bacteria/fungi are present, it is first necessary to remove as much water as possible from the fuel and then to treat with a biocide.
The biocide Bioclean is a "broad spectrum" biocide, meaning it is effective in killing a wide range of bacteria and fungi, an essential re- quirement for fuels since exact type of bio-activity is often not known.
Water contamination, especially saltwater contamination, in fuel can cause costly problems during com- bustion, such as high temperature corrosion of engine components by ash deposits. Fortunately, high tem- perature corrosion and ash deposi- tion problems can be terated with additives such as Burnall or Clean- burn, which are effective in both these areas. With the use of a fuel conditioner these problems as well as storage tank and pipeline corro- sion can be avoided.
Unitor also offers Gamabreak, a versatile and effective water demul- sifying additive.
VERITAS PETROLEUM
Circle 86 on Reader Service Card
Veritas Petroleum Services (USA), Inc., Teaneck, N.J., has been offering a Blend Optimization Pro- gram (BOP) to its customers for almost three years. Veritas's experi- ence indicates that many operators in the program were using 50 per- cent MDO in their BFO. With BOP, they have been able to consistently meet all quality targets using on average only 30 percent MDO.
Without BOP and a fixed blend rec- ipe, blended fuels frequently will exceed one or more specification pa- rameters.
According to Veritas Petroleum
Services, assuming an $80 ton prem- ia, an operator that uses three tons blended fuel oil per day can expect to reduce his annual fuel costs by about $10,000 per vessel.
Many vessel operators engage in on-board blending of marine residu- al fuel and diesel fuel to produce a blended fuel for auxiliary engines.
This practice became much more prevalent after the substantial price increase for petroleum products in the 1970s. Indeed a variety of com- mercial blending units are avaialble to the marine operator for this pur- pose. For operators who do on- board blending the key question is, "How much diesel fuel is required so that the resulting blended fuel meets the auxiliary engine builders fuel specification limits?" Surpris- ingly, many operators don't ask this question, and fewer still know the answer. Before this question is an- swered a number of general observa- tions on blended fuel quality and cost are required. (1) The key quality parameters of a blended fuel are almost exclusive- ly due to the heavy fuel component.
Specifically, these include carbon residue, ash, abrasive particles, va- nadium and sodium. The MDO component of the blend has a negli- gible impact on these qualities. The
MDO only influences density and viscosity. Viscosity alone is not a quality parameter. (2) Heavy fuels can vary very widely in all these characteristics.
This variation is found between suppliers within a single port, and is not necessarily consistent over time for a single supplier. (3) It is bad economics to use too much distillate fuel. The cost of blended fuel is directly related to the amount of MDO used. The equation for determining this cost is as follows: Blended Fuel Cost ($
Ton) = HFO price + (% MDO) Dis- tillate Premium/100, where distil- late premium is the cost difference between MDO and HFO.
The more MDO in the blend, the higher the price. For example, at $100/ton HFO and an $80/ton dis- tillate premium, a 50 percent blend would cost $140/ton while a 30 per- cent blend would cost $124/ton.
The operator's objective is to meet the builder's blended fuel spec while using the minimum amount of distillate fuel. To optimize a blend, the operator must know the follow- ing: (1) Before blending, the operator should make sure the components are compatible. There is only one way to reliably do this, and that is to mix the actual components and run the appropriate test on the blended fuel; (2) The engine builder's spec lim- its should be known in order to tar- get qualities for the blended fuel; (3) A complete analysis on the
HFO must be obtained; (4) The vis and density of the
MDO must also be known.
The following simple example serves to illustrate the above points.
Assume that the engine builder's carbon residue limit is 10 percent maximum. For simplicity, let us as- sume he is blending with clean
MDO. To meet the MCR limit of 10, he would require a blend with 41.2 percent MDO if the HFO has an
MCR of 17, but only 9.1 percent
MDO if the HFO MCR was 11, and 0 percent MDO if the MCR was less than or equal to 10. The answer to the question posed above is that each fuel is different, and so is each optimized blend. •
Engrave Signs When You Need Them!
To Identify
UPPER DECK ^
BALL ROOM
BURSAR
CABINS 300-345 ^
CABIN 313
To Inform
Mr. Perkins
Engrave These Signs & Name Tags Yourself. • Immediate in-house response to sign requirements. • Professional results with no special training. • Up to 50% lower sign costs. • Complete line of supplies. • Prompt delivery.
BREAKER
PANEL 17
Made In U S A
Scott Machine Development Corporation
Route 206, P.O. Box 88, Dept. 451
Walton, New York 13856-0088
Tel: 607-865-6511 Fax: 607-865-7269 Telex: 646827
Schoellhorn-Albrecht
Names Rheams
Gulf Area Sales Manager
Stephen P. Rheams
Robert Pavlisin, vice president of Schoellhorn-Albrecht Machine
Company, a St. Louis-based marine deck equipment manufacturer, has named Stephen P. Rheams as
Gulf area sales manager in Luling,
La.
Mr. Rheams will represent the firm's products and services to the inland and offshore marine indus- tries in regions of Texas, Louisiana,
Mississippi, Alabama and Florida.
Bringing 10 years of experience in the marine industry to his new posi- tion, Mr. Rheams is a past vice- president of the Greater New Or- leans Barge Fleeting Association and was director of the group's Riv- er Industry Seminar for the past two years.
Schoellhorn-Albrecht, co-owned by Mr. Pavlisin and Norman
Morgan, is a manufacturer, dis- tributor and repair facility for cap- stans, winches and deck fittings, serving the inland and coastal wa- terways with offices in St. Louis and
New Orleans, La.
MSI Offers 12-Page,
Full-Color Brochure On
Facilities And Capabilities
MarineSafety International (MSI) is offering a free 12-page, full-color brochure on its facilities and capabilities.
MSI provides man-in-the-loop simulation for research and training to government agencies and to the maritime industry. The company operates ship simulators at Kings
Point, N.Y., and Newport, R.I. En- gine room and cargo-handling simu- lators are located at LaGuardia Air- port and the State University of
N.Y. Maritime College, Ft. Schuyl- er, N.Y.
MarineSafety's state-of-the-art simulator facilities are comple- mented by experienced ships' mas- ters, hydrodynamicists, psycholo- gists and computer scientists who make up the instructional and re- search staffs.
For further information and a free copy of this well-illustrated, informative brochure from Marine-
Safety,
Circle 42 on Reader Service Card
Circle 201 on Reader Service Card 52 Maritime Reporter/Engineering News