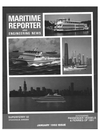
Page 14: of Maritime Reporter Magazine (January 1992)
Read this page in Pdf, Flash or Html5 edition of January 1992 Maritime Reporter Magazine
MS
STEEL SPRING
FLEXIBLE COUPLINGS
HF (HUB-FLANGE)
ARRANGEMENT
LO-REZ helical steel-spring couplings, with their low, constant and accurately controlled torsional stiffness factors, provide excellent torsional characteristics for marine reciprocating propulsion systems, engine and r eciprocating compressor drives of many varieties, locomotive drives, etc., throughout the world.
LO-REZ was one of the first coupling manufacturers in the early fifties, to recognize the importance of torsionally-soft coupling in power transmission systems, particularly in reciprocating, variable speed systems and those involvinggearing.
Circle 232 on Reader Service Card
STEEL SPRING
VIBRATION ISOLATORS
LO-REZ manufactures both the conventional untuned viscous dampers and its new mechanically -tuned visous dampers.extensive research has shown that the single and compound tuning methods, as developed, reduce resonant amplitudes by at least 40% and 60%, respectively, of the untuned values.
Circle 271 on Reader Service Card
UNTUNED & MECHANICALLY-TUNED
VISCOUS TORSIONAL
VIBRATION DAMPERS
LO-REZ manufactures a broad line of steel-spring and rubber vibration Isolators.
The BR series steel-spring isolators (shown here) with their ample thrust capacity and rubber-cushioned, adjustable stop (to limit excess vertical excursion ) are widely used for marine auxiliary and other mobile applications. No external chocks are required. BR series isolators. They are ideal isolation supports, also, for machinery rafts in ships.
Circle 272 on Reader Service Card
Designed & Manufactured by
LO-REZ VIBRATION CONTROL LTD. 156 West 8Hi Avenue,
Vancouver, B.C. Canada V5Y 1N2
Phone: (604) 879-2974
Fax: (604) 879-6588
BR4-LS SERIES
VISCOUS
DAMPER
TYPE DT
Contamination Of Diesel Fuel:
Impact, Causes & Prevention*
There is an interesting paradox regarding the microbial contamination of diesel fuels. Although the adverse impact of microbial contamination in diesel fuels has been thoroughly documented, and a variety of products and procedures are available for minimizing this impact, of the nearly 12 billion gallons of diesel fuel consumed annu- ally in the U.S., less than one percent is treated with an antimicrobial agent. One explanation for this paradox is that few marine, railroad and truck fleet operators recognize the economic im- pact of uncontrolled microbial contamination.
The effects of microbial contamination are often subtle, and rarely identified by system operators as the cause of defined fuel performance stability problems.
Impact Of
Microbial Contamination
Problems arise from both the direct and indi- rect effects of microbial growth in diesel tanks.
For example, the biodegradation of fuel, in sup- port of microbial growth, is a direct impact of contamination. Color, heat of combustion, pour point, cloud point, detergent and anti-corrosive properties change as microbes selectively attack fuel components.
Some of the indirect effects of microbial con- tamination of diesel fuels include: (1) Microbially influenced corrosion; (2) Biofilms; (3) Corrosive acids; (4) Hydrogenase-caused depolarization of metallic surfaces; (5) Transfer-line flow restric- tions; (6) Filter plugging; (7) Engine wear; (8)
Corrosive deposits on engine parts—injectors, cylinder linings, etc.; (9) Reduced heat of combus- tion; (10) Fuel property changes—color, pour point, cloud point, thermal stability, etc.; and (11) Loss of additive performance.
Filter clogging, increased engine, piston and cylinder wear rates and increased torque on camshafts translate into increased maintenance costs and engine failure.
If engine failure occurs to a marine diesel during operations in restricted waters or heavy seas, the impact can be catastrophic. As anti- corrosive additives are biodegraded, and organic acids accummulate in fuel, the probability of corrosion deposits on pistons, cylinders and in- jectors increases.
Contamination
Prevention & Control
There are four primary aspects of contamina- tion prevention and control. They are: (1) Engi- neering; (2) Monitoring; (3) Maintenance; and (4)
Treatment.
Each aspect contributes to successful minimi- zation of microbial contamination problems, and consequently to reduction of operating costs at- tributed to these problems.
Engineering
Fuel systems can be divided into storage, trans- fer, purification and delivery/combustion compo- nents. Storage takes place in tanks. The oppor- tunity for contamination and the facility with which contaminants are removed are, in large part, a function of tank design. Small service tanks should be equipped with a drain at their lowest point. Service tanks should be mounted so that water and sediment bottoms can be drained off easily. Tank vents should be equipped with filters to prevent particles from being drawn in as fuel is removed.
Large tank design should follow the same principles as those recommended for service tanks. In larger tanks it is even more critical to provide a means for removing water and sludge from the bottoms at regular intervals. Drain systems must be designed to minimize the risk of accidental release of contaminated bottoms into the environment. Tanks also need access for periodic inspection and maintenance.
Monitoring
There are four objectives of fuel monitoring programs: (1) To indicate whether fuel systems are contaminated; (2) To provide information to facilitate trouble-shooting, when necessary; (3)
To determine whether stored fuel has deterio- rated beyond acceptable limits; and (4) To pro- vide criteria for scheduling preventive mainte- nance on fuel and fuel systems, thereby avoiding unexpected failures during operations.
During monitoring, sampling procedures must ensure that representative proportions of fuel/ bottoms-water are collected. The data collected during analyses must provide an indication of the suitability of the fuel for its intended use, the storage conditions or some other relevant perfor- mance criterion.
Maintenance
Perhaps the single most effective maintenance practice is to minimize the exposure of distillate fuel to water. Tank insulation, recycling through water separators and routine discharge water bottoms all minimize water accumulation in fuel- storage tanks. Systems designed for water re- moval can also be equipped to remove particu- lates—including biomass—from fuel. Sludge should also be removed from tanks regularly.
In addition to processing stored fuel, and purg- ing bottoms water and sludge, periodic tank inspection and cleaning should be scheduled.
Periodic treatment with preventive doses of ap- proved fuel preservatives should prolong the interval between most of these labor-intensive maintenance activities.
Treatment
Treatment refers to both chemical addition and mechanical processing of the contaminated fuel and associated water bottoms and sludge.
The mechanical phase of the treatment process is similar to that described under "Maintenance."
To be effective, microbiocide is metered into the fuel as the fuel is pumped into a clean storage tank. Before being used again, heavily contami- nated tanks should be cleaned thoroughly.
A number of factors should be considered in evaluating biocides to be used as fuel disinfec- tants and preservatives. Key considerations in- clude water/fuel solubility, speed of kill, persis- tence of effect, compatibility with fuel and other additives, compatibility with other system com- ponents, handling and disposal safety consider- ations, and industry and regulatory approvals.
Biocide manufacturers provide instruction for the safe handling and disposal of their products.
As antimicrobials, these products are, by defini- tion, toxic. So, however, are a variety of regularly used household products such as chlorine bleach, ammonia, etc. When used as instructed, biocides represent no more risk than do these household products.
Fuel performance, system integrity, filter life and engine life can be degraded significantly by the direct and indirect effects of microbial activ- ity. Consequently, treatment with a fuel preser- vative can have a positive economic impact on bottom-line operational costs.
For more information on biocides for fuel pres- ervation,
Circle 54 on Reader Service Card 'Editor's Note: This article is excerpted from a report by Frederick
J. Passman, Angus Chemical Company, Northbrook, III., and
Stephen R. Burak Ferrous Corporation, Bellevue, Wash. 16 Maritime Reporter/Engineering News