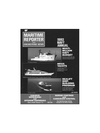
Page 80: of Maritime Reporter Magazine (February 1992)
Read this page in Pdf, Flash or Html5 edition of February 1992 Maritime Reporter Magazine
Materials Handling In The Shipbuilding,
Offshore And Heavy Industries
Fig. 1. Typical 100-ton DWB unit.
Tomorrow's shipbuilding technology for line production and materials handling is available already today, claims Stellan
Carlsson, shipbuilding specialist within The
Esab Group, in this interesting report on modern shipbuilding.
By Stellan Carlsson
It is estimated that about 5-8 per-cent of the total production time in the mechanized industry is acccounted for by operations like welding, cutting and so on.
The rest is assembly, intermedi- ate storage and handling. This means there is great potential for reducing capital expenditure in pro- duction through the correct choice of handling and transportation methods.
In this paper we shall be concen- trating on heavy materials handling within the fields of shipbuilding, offshore and similar heavy indus- tries. In this type of industry, some 75 percent of production time is ac- counted for by materials handling.
TTS—Total Transportation Sys- tems A/S in Norway is an affiliated company to The Esab Group and specializes in heavy materials han- dling and production lines for the shipbuilding and offshore industry.
It is a fact when it comes to ship- building that completed ships are — at least in the case of the largest vessels — the most massive man- made objects which have to be moved on land, although some offshore structures pose similar problems.
Until recently, the only available means of launching large vessels was to build them on inclined berths and let gravity convey them to their true element when their time came.
This could be a delicate operation and was definitely a one-way trip.
Today, as a result of experience from the offshore industry, a num- ber of techniques have been devel- oped which make it possible to move quite large ships around in a yard and to handle large prefabricated sections.
The normal handling method in a yard is to use cranes; jib-cranes for loads of up to 100 tons and gantry cranes over that weight. The largest gantry crane in use today can carry 1,500 tons. These types of crane run on rails and have a given working range.
In order to reduce the time it takes to build a ship, modern yards want a more flexible system and need to handle ship units of up to 3-4,000 tons. The basic idea is to produce the ship in the largest sections possible indoors, outfitted to the maximum level, and then to transport the sec- tions to the building berth or dock for final assembly.
TTS has developed this type of system to meet the requirements for a trackless transport system with the ability to move heavy sections or modules on a building site.
This system, the D.W.B. (Dual
Walking Beam), consists of three or more DWB units, a power source and internal control system, Fig. 1.
The DWB unit is an hydraulic- mechanical construction which "walks" at a speed of one m/min.
Each DWB unit can carry 100-400 tons (depending on the unit type); the total load capacity is a multiple of the number of DWB units in the system, Fig. 2.
The system can carry the load across uneven surfaces with coarse surface material such as gravel.
Hydraulic interconnection enables the DWB units to "float" the load, thereby preventing bumps in the road from inducing stress forces in the load construction.
The DWB system can turn and maneuver the load in very narrow areas and can also move up an in- cline, such as a slipway.
This heavy load systemnowmakes it possible for the yard to produce a complete ship indoors and trans- port it greater distances than would ever be possible using cranes.
The system has a positioning ac- curacy of within one mm.
The DWB system has been in- stalled at DCAN Cherbourg, the
French nuclear submarine construc- tion yard. The system will carry loads of up to 14,000 tons.
TTS Kenmark Docklift System
The TTS Kenmark Docklift Sys- tem is part of the cost-effective TTS
Kenmark Shiplift Concept. The new removable docklift and DWB "Loadwalkers" move ring sections from the indoor assembly floor and directly onto the keel blocks in the dry-dock. No cranes are needed for the entire operation and DWBsmove the sections without tracks across unprepared ground surfaces and permit the alignment of the sections within very small tolerances. "It is not a question of inventing something new, but rather of applying known technologies in the most efficient manner."
Since the system can be installed either permanently or semiper- manently, it permits very flexible utilization of the drydock for newbuilding, ship extensions or com- bined newbuilding and repair.
No major civil engineering work is required when installing this docklift and the compact arrange- ment makes it possible to cover the entire drydock with a movable light- weight construction building.
By employing DWB technology the ship or construction yard will im- prove its flexibility in production.
This will have a tremendous impact on the total steel manufacturing cost.
The investment level compared with a heavy gantry crane system could be reduced to about 30 percent and the handling capacity of heavy blocks for the yard will be increased.
For detailed information on this re- port contact the author at: ESAB AB,
Business Communications, Box 8004, S-402 77 Goteborg, Sweden.
Fig. 2. Basic DWB system. By combining several groups of DWB units, loads in excess of 10,000 tons can be handled.
CENTRAL CONTROL
UNIT --t- I HYDRAULIC FLOAT 3 POINT LOAD
REMOTE
CONTROLLER 80 Maritime Reporter/Engineering News