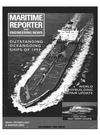
Page 44: of Maritime Reporter Magazine (December 1992)
Read this page in Pdf, Flash or Html5 edition of December 1992 Maritime Reporter Magazine
Falcon Maritime Ventures Licenses
Innovative Aluminum Boat Building
Process To Yamaha Motor Company
Who says all the fun is on shore.
Foreign Spares
Fremd O Etranger O H W-
Straniero O Utlandsk O Fremmed
Extranjero O hhoctpahhbie
Strain • Eedoo • Ulkomainen
Order all your foreign spare parts directly from Arnessen
We have everything you need, now and in the future.
Just a representative sample includes European and Japanese electrical parts.
European and Japanese cargo plugs and watertight material. Portable hand- lamps Every fuse Ma^ you might ever need. Weatherproof fSj^l sirens, and even Aldis signalling lamps and parts.
No matter what you need, and no matter where in the world you are, call or fax Arnessen today.
We deliver.
VV Tokyo London Rotterdam ••1 THC* C03P0371TI0M 1100 Walnut Street, Roselle, NJ 07203 • Telephone: (908) 241-3535 • Fax: (908) 353-8090 • Tx: 23-2028 651 Richard St., Suite 2B, New Ofleans, LA 70130 • Telephone: (504) 522-8942 • Fax: (504) 522-8943
Circle 203 on Reader Service Card 46
Falcon Maritime Ventures, of Fort Lauder- dale, Fla., has entered into a licensing agreement for the technology of its advanced aluminum boat construction process with Yamaha Motor Com- pany, Ltd., of Japan, according to Falcon's senior representative, Anthony Barrois. Yamaha's
Marine Group produces more than 16,000 boats annually, representing two-thirds of the Japa- nese pleasure boat market.
A radical departure from previous construc- tion techniques, the Falcon process is a techno- logically innovative method of building alumi- num boats developed and patented in 1988 by
Dan Johnston, an inventor and boatbuilder who became Falcon's president. In essence, the process is an application of the monocoque con- struction process. Overall construction is simpli- fied, requiring less material, manpower and vir- tually no fairing.
Through the Falcon process, hull panels take on induced curvature in either concave or convex shape. Therefore, builders are able to develop complex shapes with greater ease at less ex- pense.
The need for internal framing is substantially reduced due to the Falcon process's plate-to-plate compressive loading of hull panels. The frames are attached to the hull plate only at keel, chine and gunnel. The longitudinal members are used solely as panel stabilizers and are not attached to the hull plate.
In the process, all distortion created by the welding is controlled, while the significant re- duction in welding drastically reduces the stress points. Because the process minimizes welding, the anti-corrosive properties normally lost in conventional construction methods are preserved.
Also, as the shell plate is self-supporting, there is virtually no need for internal framing and the buckling normally created by welding aluminum is eliminated. This significantly reduces the fairing process that normally doubles the man hours required to finish a boat. Where a boat in the 100-foot class might normally require several tons of fairing compound, a boat constructed with the Falcon process would require less than 500 pounds of fairing compound.
A compound of silicon-based elastomer is in- jected between the skin and the framework. This allows the plate to yield and work against prede- termined load points. Therefore, the hull is immune to the negative effects normally caused by thermal expansion.
The Falcon process reduces overall weight by as much as 75 percent over the total structure weight of the boat. Consequently, less fuel and
Astano Receives Bardex
Turret Turning-Locking
Systems Controls
Bardex Corporation, of Goleta, Calif., has shipped to Astilleros y Talleres del Noroeste, SA (Astano) the intrinsically safe control system for the turret turning and locking system to be used onboard the Tentech 850C floating production vessel being built at Astano's El Ferrol shipyard in northwest Spain for Ocean Production and
Smedvig.
The control system, suitable for use in a Zone
One hazardous area, consists of the following components: a local enclosed, fully integrated electric control panel equipped with the actua-
Hull interior of the Global I, built using Falcon Maritime Ventures' patented aluminum construction process. smaller engines are required, creating greater accommodations space.
Several prototypes have passed rigorous tests, including an evaluation by the U.S. Navy. The
Navy's craft was a 30-foot, rigid-bottom inflat- able boat constructed with the Falcon process and outfitted with Falcon's patented shock-ab- sorbing seating system. The vessel was rated as an "extremely sturdy, well-built craft" and re- ceived the highest possible Naval Sea Systems
Command test score available. Major interna- tional boat manufacturers are currently working with Falcon on various ventures and licensing agreements.
The Falcon aluminum boatbuilding process significantly lowers total construction time, ma- terials and cost, while increasing the finished vessel's performance potential by creating a smaller engine plant, less machinery and re- duced manpower.
Through the process, boat manufacturers cre- ate a stronger, lighter and more flexible hull which requires little fairing, and is easier and less expensive to construct and repair. Falcon is offering boat manufacturers plagued by high material and labor costs an opportunity to reduce their overall construction costs and delivery times, while increasing profitability.
In addition to its Fort Lauderdale headquar- ters, Falcon Maritime Ventures also maintains offices in Colorado Springs, Colo., and Seattle,
Wash.
To receive additional free information from
Falcon Maritime Ventures about its new alumi- num boatbuilding process,
Circle 42 on Reader Service Card tors and display necessary for either automatic or manual operation of the system; a control cubicle complete with programmable controller, logic relays and proportional control valve elec- tronics; and pressure compensating proportional valve units.
Bardex also is supplying four hydraulic grip- per-jack assemblies for rotating the floating pro- duction vessel's turret in either direction and locking it in position. The Bardex advanced turret system will reportedly be capable of rotat- ing the turret at speeds of as much as 360 degrees in 25 minutes.
For additional free information about Bardex's turret turning/locking control system,
Circle 11 on Reader Service Card
Maritime Reporter/Engineering News
Circle 240 on Reader Service Card
Marine antennas from Naval Electronics are bringing shipboard television entertainment to naval personnel around the world.
Naval Electronics has designed and installed inte- grated broadcast distribution systems for such vessels as the USS Independence, Ticonderoga, Nimitz, Wasp,
Spruance, Stark...
Find out how easy it is to take TV to sea. Write for our free brochure.
Naval Electronics, Inc., 5417 Jetview Circle,
Tampa, Florida, 33634. ^(8]3)885-609Io electronics
Or fax (813) 885-3789.
Naval